Текст книги "Большая энциклопедия техники"
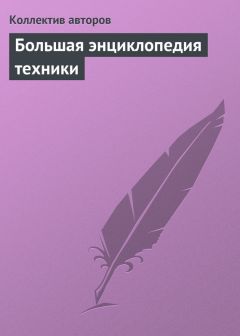
Автор книги: Коллектив Авторов
Жанр: Энциклопедии, Справочники
Возрастные ограничения: +12
сообщить о неприемлемом содержимом
Текущая страница: 34 (всего у книги 179 страниц) [доступный отрывок для чтения: 58 страниц]
Таль
Таль (от голл. talie) – подвесное грузоподъемное устройство, содержащее лебедку для подъема груза и тележку. Таль выполняют в основном в четырех вариантах. Первый вариант: соосно двигателю располагают барабан с тросом и редуктор. Двигатель в данном варианте имеет подпружиненный конусный ротор. При включении двигателя ротор втягивается в статор и тормоз размыкается. При включении двигателя ротор под действием пружины перемещается влево, и тормоз автоматически замыкается. Второй вариант: двигатель тали непосредственно встроен в барабан, и его статор вращается вместе с барабаном. В корпусе редуктора дополнительно установлен тормоз. Третий вариант: барабан тали в виде обечайки без торцовых стенок установлен на подшипниках. Двигатель в этом варианте с неподвижным корпусом встроен в барабан. Четвертый вариант: двигатель тали встроен в барабан и соединен с планетарным трубчатым редуктором, установленным в отдельном корпусе. В различных отраслях промышленнохозяйственного комплекса России широко применяются тали рычажные марки ТР-1М и шестеренчатые ручные тали. Технические данные рычажной тали ТР-1М таковы: грузоподъемность – 1 т, максимальная высота подъема груза (при длине цепи в 5 м) – 2,2 м; усилие на рукоятке (при номинальном грузе) – 0,26 кН (0,27 кг/с), шаг грузовой цепи – 25 мм; расстояние между крюками: максимальное – 2500 мм, минимальное – 455 мм. Основные размеры: длина (с рукояткой) – 510 мм, ширина – 170 мм; масса (с грузовой цепью – 19,6 кг). Технические данные шестеренчатой ручной тали: грузоподъемность – 2 т, максимальная высота подъема груза – 12 м, тяговое усилие на цепи – 0,49 кН (50 кг/с), масса 75 кг.
Тельфер
Тельфер – грузоподъемный механизм, включающий такие элементы, как:
1) электродвигатели – 2 шт.;
2) редукторы – 2 шт.;
3) лебедку;
4) трос или цепь с крюком и стропами для захвата груза;
5) пульт управления электродвигателями (дистанционное управление);
6) тележку, перемещающуюся по направляющим (направляющие выполняются из швеллера шириной 80 мм).
Один из электродвигателей приводит в движение тележку тельфера (через редуктор зубчатой передачи). Второй двигатель, смонтированный в одном узле с лебедкой, через второй редуктор зубчатой передачи осуществляет вращение барабана лебедки с последующей намоткой троса (или цепи) при подъеме груза или размотку троса при опускании крюка со стропами для обеспечения захвата груза. Лебедка вместе с электродвигателем перемещается вдоль поперечной балки тельфера с помощью четырех небольших колес, выполненных в виде дисков. Тельфер имеет максимальную грузоподъемность до 5 т, а высоту подъема до 6 м. Тельферы обычно устанавливаются в складских помещениях предприятий и рассчитаны на выгрузку-погрузку малых партий груза в виде металлических труб небольшого диаметра, а также металлопроката (уголки, прутки, балки, швеллеры и т. д.). Под лебедкой тельфера устанавливается ограничитель подъема груза.
Тормоз
Тормоз (от греч. tormos – «отверстие для вставки гвоздя, задерживающего вращение колеса») – устройство для уменьшения скорости или полной остановки машины. Тормоза являются очень важным составным элементом грузоподъемных и транспортных машин, железнодорожного подвижного состава (включая тепловозы, электровозы, мотодрезины и др.).
Тормоз грузовой
Тормоз грузовой – устройство, предназначенное для удержания от вращения вала грузоподъемной машины; подразделяется на:
1) ленточный;
2) колодочный;
3) дисковый;
4) конусный.
Тормоз грузовой включается при отключенной системе питания привода. Выключают такой тормоз путем размыкания колодок или ленты (специальной тормозной). Управление тормозом грузовым выполняют с использованием:
1) электромагнитов;
2) гидроцилиндров;
3) центробежного толкателя или других устройств в зависимости от конструкции грузоподъемной машины.
Электромагниты по-разному осуществляют управление тормозом:
1) элементы электромагнита непосредственно воздействуют на два рычага и, сжимая две пружины, раздвигают тормозные колодки;
2) электромагнит установлен между двумя коромыслами; при включении электромагнита одно коромысло притягивается к другому и через толкатель первое коромысло воздействует на пружину и раздвигает колодки.
От гидроцилиндра управление тормозом производится через пространственный механизм, при этом воздействуя на специальный рычаг, раздвигают тормозные колодки. В другом варианте пружины и гидроцилиндр размещают между рычагом и стойкой, при этом также оказывается воздействие на тормозные колодки через рычаг. В системе тормозов ленту (специальную тормозную) или колодки замыкают обычно пружинами. Например, лента тормозная огибает шкив, а через два рычага она соединена с коромыслом, взаимодействующим с магнитом. Три звена (коромысло и два рычага) образуют двухкоромысловый механизм, при этом два рычага соединены пружиной. Третий рычаг и вторая пружина используются для того, чтобы при отключении тормоза отводить ленту от шкива. Тормоза у железнодорожного подвижного состава образуют целую систему, в которой они связаны между собой и управление осуществляется совместно или раздельно по группам. Такая система из нескольких тормозов состоит из: пневмоцилиндров, балансирных звеньев, нескольких тяг и рычагов с выходом на специальные тормозные колодки, охватывающие колеса вагонов. (Тормозные колодки для подвижного железнодорожного состава выполняются из специальных марок чугуна, причем для тепловозов и электровозов они делаются усиленными.) В данном случае тормозные колодки связаны шарнирно со всем семизвенным механизмом, в который входит и пневмоцилиндр. В процессе управления тормозной системой колодки при соответствующем положении звеньев прижимаются к колесу (при включении системы тормозов для выполнения торможения) или удаляются от него. Кроме того, семизвенный механизм обеспечивает самоустановку колодок в зависимости от положения оси колеса.
У транспортных средств тормозные системы устроены по-разному. Простейшая система тормозов автомобиля управляется раздельно педалью и специальной рукояткой. В данном случае тормозная система включает в себя: тяги, рычаги, троса, кулачки управления колодками (тормозными), тормозной барабан. В другом варианте автомобильная система тормозов выполнена вакуумной и состоит из: педали, рычагов, тяги, пневмораспределителя (соединяющего полость цилиндра с всасывающим трубопроводом), поршня, кулачка, колодок (тормозных автомобильных), тормозного барабана, цилиндра. Поршень под действием атмосферного давления перемещается, поворачивает рычаг и через тягу поворачивает кулачок, который раздвигает колодки и прижимает их к тормозному барабану. При отпускании педали она возвращается в начальное положение, при этом пневмораспределитель соединяет полость цилиндра с атмосферой и тормозная система выключается. В тех случаях, когда тягач и прицеп составляют автопоезд, для управления тормозами используется специальный тормозной пневматический кран. Последовательность включения тормозных систем при различии времени их срабатывания обеспечивает синхронность подачи воздуха к тормозам тягача и прицепа.
Торсион
Торсион – торсионный вал (от фр. torsion – «скручивание», «кручение») – гибкий вал, служащий для передачи вращающих моментов. Торсион представляет собой пружину или тонкий металлический стальной стержень, работающий на кручение. Такой вал применяется в тех случаях, когда выполнение жесткого вала по конструктивным причинам затруднительно, например, для соединения станочных автоматических систем управления с приборами (например, рабочих органов механических систем с рычагами управления). Торсион применяется чаще всего в торсионных подвесках – подвесках ходовых колес. Во второй половине ХХ в. торсионные подвески использовались в легких танках и в некоторых автомобилях с небольшой полной массой.
Трансмиссия
Трансмиссия (от лат. transmissio – «переход», «передача») – устройство, предназначенное для передачи вращения от двигателя к потребителям энергии. Обычно под трансмиссией понимают силовую передачу для параллельного или смешанного соединения нескольких потребителей с одним двигателем. Примером трансмиссии является, например, трансмиссионный тормоз – устройство для торможения транспортной машины, устанавливаемое обычно на выходном валу коробки передач и приводимое вручную перемещением рукоятки управления. Трансмиссионный тормоз состоит из рукоятки управления, защелки, сектора, пружины, рычагов, подвижных звеньев, толкателя, колодок, шариков, тормозного шкива, связанного с валом. Торможение в трансмиссионном тормозе осуществляется следующим образом: от рукоятки движение через подвижное звено и один из рычагов передается толкателю, в свою очередь толкатель перемещает шарики, которые раздвигают колодки до их контакта с поверхностью тормозного шкива, связанного с валом. Начальное положение тормозных колодок в трансмиссионном тормозе регулируют с помощью специального кланового механизма.
Транспортер
Транспортер (от лат. transporto – «переношу», «перемещаю», «перевожу») – устройство, предназначенное для транспортировки каких-либо материалов (например, сыпучих) или грузов на небольшое расстояние. Транспортеры разных видов и типов широко применяются во многих отраслях промышленно-хозяйственного комплекса России. Самый простой и небольшой по размерам транспортер винтовой применяется на многих станках-автоматах. Такой транспортер устанавливается в верхнем корыте основания станка под зоной резания металлических заготовок и предназначен только для удаления сыпучей стружки (в частности, стружки ступенчатой). Еще в 70-х гг. ХХ в. был создан конструкторами Союзводоканалпроекта скребковый транспортер для прямоугольных отстойников, который предназначался для очистки дна нефтеловушек и нефтеотделителей от выпадающих из жидкости осадков. Такой транспортер сгребал илистые осадки с горизонтального дна секций к специальным приямкам. Дальнейшее удаление осадков из приямков производится через донные клапаны и илоотводящий трубопровод. Скребковый транспортер применялся и применяется в настоящее время на нефтеперерабатывающих заводах для очистки оборотной воды от всплывающих нефтепродуктов. Такой транспортер представляет собой две шарнирно-пластинчатые цепи, к которым по их длине через 2—4 м прикреплены скребки из досок. Цепи приводятся в движение электродвигателем через редуктор и звездочки, закрепленные на четырех валах. Валы вращаются в самоустанавливающихся подшипниках, расположенных на кронштейнах, прикрепленных к стенкам. Один из четырех валов монтируется на подвижных подшипниках с направляющими, что позволяет натягивать цепи. Привод скребкового транспортера осуществляется от электродвигателя КОМ-22-6 мощностью 1,7 кВт с частотой вращения 930 мин-1 через редуктор ГТ-V-175,6 с передаточным числом i = 175,6 и цепные передачи с общим передаточным числом i = 16. При разгрузке сыпучих грузов из вагонов и полувагонов широко применяются шнековые транспортеры, главным элементом которых является вращающийся шнек, с приводом от электродвигателя. Такой транспортер состоит из металлического желоба, в котором установлен шнек с некоторым зазором от основания желоба. Шнек по концам закреплен в подшипниках качения. Транспортеры ленточные широко применяются в различных предприятиях аграрного сектора хозяйственного комплекса России. Данные транспортеры оснащены резинотканевой транспортерной лентой, опирающейся на ролики; кроме того, на самой ленте прикреплены поперечные планки, удерживающие какой-либо груз на поверхности. Подобные транспортеры применяются, в частности, на птицефабриках и животноводческих фермах. На элеваторах и в зернохранилищах применяются в основном шнековые транспортеры, предназначенные для перемещения зерна, например при загрузке автомашин-самосвалов или специальных зерновозов бункерного типа. Автомашины-зерновозы также имеют небольшой шнековый транспортер, применяемый при выгрузке зерна или комбикормов потребителю. Шнековые транспортеры также широко применяются на предприятиях стройиндустрии России.
Трикотажная машина
Трикотажная машина – то же, что и вязальная машина – машина для изготовления трикотажных полотен и различных изделий. В зависимости от способа прокладывания и провязывания нитей (пряжи) различают трикотажные машины поперечного вязания, на которых проложенная нить провязывается на всех иглах последовательно, и трикотажные машины продольного вязания, на которых одновременно прокладывается большое число нитей (каждая на свою иглу), а затем они провязываются в петли. Трикотажные машины характеризуются классом (число игл, приходящееся на единицу длины игольницы) и подразделяются на плоские; круглые; одинарные; двойные. По назначению такие машины делятся на:
1) машины, предназначенные для выработки трикотажных полотен (гладких и рисунчатых);
2) автоматы для вязания штучных трикотажных изделий или отделки деталей изделий (так называемый регулярный трикотаж), гладких или рисунчатых;
3) полуавтоматы для изготовления трикотажных изделий или их частей, требующих последующего подкроя при окончательном пошиве какого-либо трикотажного изделия (полурегулярный трикотаж).
Тумблер
Тумблер (англ. tumbler, от tumble – «опрокидываться»), малогабаритный переключатель на два либо три положения с рычажно-пружинным приводом. Тумблер применяется главным образом для коммутации цепей управления (реже цепей питания) в электротехнических аппаратах, приборах и устройствах и в радиоэлектронной аппаратуре. Устанавливают тумблер обычно на панелях и щитках управления приборов (аппаратов) и пультах управления. Максимально допустимое напряжение 380 В, ток 3А.
Фальцовка
Фальцовка – производственный метод сгибания листа или изделия, которое производится с помощью специальных устройств, используя материал с плотностью до 200 г/м2.
Разработаны устройства, способные создавать четыре параллельных и два перпендикулярных фальца, перфорацию или биговку, на бумаге плотностью 80—170 г/м2.
Фальцовка применяется для изготовления буклетов, лифлетов, тетрадей, журналов, каталогов и т. д.
Фальцирующий механизм
Фальцирующий механизм – устройство, предназначенное для выполнения сгиба листа бумаги, широко применяется в полиграфических работах.
Данный механизм функционирует следующим образом: лист бумаги перемещается при вращении подающего цилиндра в положение, при котором линия сгиба располагается между захватывающими валиками.
Фальцирующий нож при этом выходит из продольной прорези барабана и образует сгиб листа. Далее лист захватывается валиками, складывается вдвое и перемещается.
Валики установлены на специальных рычагах и поджаты один к другому пружиной. Для привода фальцирующего ножа применяется планетарный зубчатый механизм. Водило фальцирующего механизма жестко соединено с цилиндром.
На указанном водиле установлены зацепляющиеся сателлиты (два). Один из сателлитов взаимодействует с неподвижным центральным колесом, а на втором сателлите жестко закреплен нож. Передаточное отношение между двумя колесами при остановленном водиле равно двум. При таком условии и длине ножа аω (омега), где аω – межосевое расстояние планетарной передачи, конец лезвия ножа во время фальцовки листа бумаги движется строго по вертикали.
Фрикционная передача
Фрикционная передача – механическая передача, служащая для передачи вращательного движения от одного вала к другому с помощью сил трения, возникающих между дисками, цилиндрами или конусами, насаженными на валы и прижимаемыми друг к другу. Фрикционную передачу используют в бесступенчатых передачах, фрикционных прессах и фрикционных молотах. В большинстве случаев фрикционную передачу применяют в малонагруженных механизмах.
Фрикционная передача характеризуется тем, что допускает относительный поворот валов за счет незначительного проскальзывания сопряженных поверхностей трения при возрастании передаваемого крутящего момента выше предельной величины, из-за высоких скоростей вращения валов или из-за увеличения нагрузки на весь механизм в целом.
При расчете фрикционной передачи обязательно определяют крутящий момент, учитывая инерционные явления в период установившегося движения всех элементов какого-либо механизма (станка, машины, механической системы).
Фрикционная передача, выполненная в виде бесступенчатой передачи с соответствующим регулированием работы какого-либо механизма, имеет целый ряд преимуществ перед ступенчатыми передачами:
1) облегчение возможности автоматизации и управления на ходу, например для поддержания постоянства скорости намотки пряжи в шпули, бумаги в рулоны, постоянства скорости резания при обточке нецилиндрических поверхностей заготовок или деталей на станках токарного типа, что приводит к значительному повышению производительности работы (примерно в два-три раза);
2) повышение качественных показателей:
а) получение наивысшей чистоты поверхностей, обработанных на станках токарного типа;
б) повышение точности работы испытательных машин;
в) выход из области резонанса;
3) повышение производительности и экономичности вследствие возможности выбора наиболее целесообразного режима процесса, в частности с наиболее полным использованием мощности электродвигателя (в том числе реверсивного).
Фрикционный механизм
Фрикционный механизм – устройство, в котором передачу движения, разгон или торможение осуществляют благодаря силам трения между прижимаемыми друг к другу элементами. Во фрикционном механизме, состоящем из жестких элементов (в передаче, муфте, тормозе фрикционного исполнения), минимальное требуемое усилие прижатия N = F21 / f0, где F21 = -F12 требуемая окружная сила, f0 – коэффициент трения покоя. При этом определяют момент трения, передаваемый благодаря силам трения. Для фрикционной передачи: Т1 = F21R1, T2 = F12R2, откуда Т1 / Т2 = R2 / R1 (только без учета потерь на трение).
Для колодочного тормоза тормозной момент T = f0Nr, для дискового тормоза зависимость такая же, но R (R2 – R1) / 2 – радиус, для которого определяется равнодействующая сил трения. В ременных передачах, ленточных конвейерах, тормозах и муфтах натяжение в ветвях S1 и S2 обеспечивает прижатие ремня или транспортерной ленты (резинотканевой) к шкиву. Если T = 0, то S1 = S2 = S0, а при T ≠ 0 из условия равновесия S1 – S2 = F, где F = T / R – окружная сила – сила трения между гибким элементом данного механизма и шкивом. При этом справедливо соотношение S1 / S2 = ef0α (формула Эйлера), где α – угол охвата шкива гибким элементом.
Суммарное начальное натяжение в ветвях S1 и S2 остается неизменным при приложении момента Т.
Наиболее широко в различных машинах, установках, станочных автоматических линиях применяется такой вид фрикционного механизма, как фрикционная муфта (от лат. frictionis – «трение») – устройство, предназначенное для соединения двух валов с передачей вращающего момента благодаря силам трения между пластинами или дисками, связанными с этими валами. Фрикционная муфта позволяет осуществлять плавное сцепление вращающихся валов, уменьшает динамические нагрузки при пуске, предохраняет привод от перегрузок. Другим примером фрикционного механизма является синхронизатор (от греч. synchronos – «одновременный») – устройство для безударного и бесшумного переключения с одного режима на другой коробки передач. Действие такого фрикционного механизма основано на предварительном уравнивании угловых скоростей соединяемых деталей. На валу синхронизатора устанавливается колесо таким образом, что оно может вращаться. Это колесо соединяют с валом посредством муфты, содержащей два звена. При осевом перемещении второго звена оно движется совместно с первым звеном благодаря фиксации шариком. Сначала в контакт вступает специальный фрикционный элемент, не рассчитанный на передачу рабочей нагрузки, но способный уравнять скорости звеньев – первого и третьего (в виде колеса, установленного на валу). При дальнейшем перемещении второго звена шарик отжимается и это звено (т. е. второе) входит своими зубьями во взаимодействие с зубьями указанного колеса. В результате полученное соединение обеспечивает передачу вращения от вала зубчатому колесу.
Храповый механизм
Храповый механизм – устройство, в котором относительное движение звеньев возможно только в одном направлении, а в другом направлении звенья такого механизма взаимодействуют благодаря давлению их элементов и не могут перемещаться относительно друг друга. Храповый механизм применяют в качестве задерживающего устройства в грузоподъемных механизмах. Храповым механизмом является, например, грузоупорный тормоз – фрикционный тормоз, управляемый автоматически в зависимости от вращающего момента на входном звене. Грузоупорный тормоз выключается только при наличии вращающего момента на входном звене, достаточного для преодоления сил сопротивления, приведенных к входному звену. Грузоупорный тормоз включается при отсутствии вращающего момента на входном звене. Храповый механизм применяется также в передачах периодического вращательного движения, в частности в устройстве для преобразования качательного движения в однонаправленном движении и т. д.
Правообладателям!
Данное произведение размещено по согласованию с ООО "ЛитРес" (20% исходного текста). Если размещение книги нарушает чьи-либо права, то сообщите об этом.Читателям!
Оплатили, но не знаете что делать дальше?