Текст книги "Инновации от идеи до рынка"
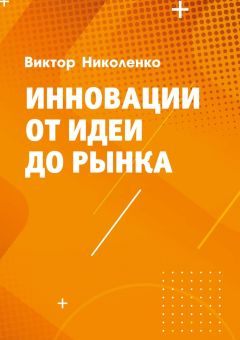
Автор книги: Виктор Николенко
Жанр: Прочая образовательная литература, Наука и Образование
Возрастные ограничения: +16
сообщить о неприемлемом содержимом
Текущая страница: 19 (всего у книги 32 страниц)
В новых проектах нужно использовать ПИ, как один из эффективных способов достижения удовлетворенности клиентов на рынке, прибыльности и качества.
4.3 Проектирование под заданную стоимость
Следующим инструментом получения инновационных продуктов в заданные сроки и при располагаемом бюджете является проектирование под заданную стоимость, или дизайн для производства. В этом разделе книги использованы материалы из [8].
Ценность продукта или услуги является довольно сложным понятием и отличается для разных точек зрения.
Потребительская ценность определяется путем оценки ценности системы клиентом на основе ее объективно измеримых выгод (например, сэкономленного времени, полученной прибыли, и т.д.).
Потребительская стоимость отражает оценку свойств потребительских товаров покупателем (например, экономии времени на процедуре очистки традиционной кофемашины, при переходе приготовления эспрессо к капсульной кофемашине) и услуг (например, экономия времени или затрат на оформление покупки и транспортировку при доставке еды на дом). Кроме того, покупатели могут основывать свой выбор на концепции ценности уважения к бренду (качество, эстетика, роль статуса, и т.д.).
Рыночная стоимость представляет цену, которую потребитель ожидает заплатить, учитывая оценку ценности и использования системы в сравнении с конкурирующими альтернативами.
Процесс изменения затрат на продукт можно разбить на возможные варианты влияния действий компании:
1. Снижение затрат за счет изменения свойств и привлекательности продукта до такой степени, что его цена снижается. В итоге это сохраняет клиенту часть средств, а фирме сулит меньшую прибыль.
2. Снижение затрат трудоемкости, которое не меняет восприятие продукта клиентом и его потребительскую стоимость. При этом фирма может держать ту же цену, увеличив прибыльность товара.
3. Увеличение затрат для создания добавочной ценности, которое приводит к улучшению продукта, и, соответственно, увеличению стоимости.
Рассмотрим детали этих предложений:
• Получение того же продукта по более низкой цене. Перед командой стоит задача проанализировать элементы спецификации системы и предложить изменения, которые не изменят ни функции, ни архитектуру системы, а только отдельные компоненты. Например, замену материалов, поставщиков, технологии процесса, отмену предыдущего выбора ПКИ «сделать или купить», и изменение детального проектирования компонентов (например, формы, размеров, допусков). В частности, конструкторы, не уверенные в надежности детали, выбрали дорогой материал с высоким качеством от поставщика с хорошей репутацией. Опыт эксплуатации может подсказать более дешевое решение. При решении указанных задач время, затрачиваемое на анализ, проверку жизнеспособности решений и их принятие, может быть весьма существенным. Поэтому целесообразно вводить мероприятия только, если ожидаемые выгоды (выраженные в процентах экономии на единицу продукции) окажутся оправданными. Это может быть рентабельным в отношении продуктов, объем выпуска или стоимость единицы продукции которых достаточно высоки, чтобы оправдать затраченные усилия.
• Получение тех же функций с меньшими затратами. Это предполагает относительно глубокую переработку системы. Общие функции продукта или услуги не изменятся, равно как и его архитектура. Компоненты следует анализировать один за другим с целью замены, подразумевая изменение выбора варианта реализации. Например, электромеханическое реле можно заменить дешевым электронным твердотельным реле. Диапазон доступных вариантов обычно невелик. Команды стремятся сосредоточиться на нескольких ценных компонентах, которые можно заменить функциональными эквивалентами.
• Получение улучшенных функций по доступной цене. Отличается существенной переработкой системы. Целесообразно проводить ее на начальном этапе разработки для функций, которые реализуют базовые компоненты (что определяет полезность и ценность продукта). Каждая функция (и связанный компонент) изначально определяется полезностью (имеет значение для потребителя), а ее реализация будет характеризоваться стоимостью (которая, напротив, имеет значение для производителя). Соответственно, следует изучить и попытаться сбалансировать стоимость и полезность функций и компонентов, чтобы добавочная ценность улучшенного продукта скомпенсировала понесенные затраты разумным увеличением цены.
В современных условиях выполнения ОКР под жестким давлением сроков и бюджета важен подход к проектированию инновационных продуктов и систем, с учетом проектного ограничения себестоимости, которое рассматривается в качестве равноценного требования, предъявляемого к изделию или системе. Успех изделия на рынке определяет соотношение показателей его качества и цены. Следовательно, себестоимость не должна превышать заданного максимального значения затрат. Так как она на 70…80% определяется заложенными проектными решениями, то на этапе детального проектирования и разработки любого компонента системы очень важно убедиться, что:
• компонент будет соответствовать своим функциональным характеристикам,
• может быть легко изготовлен,
• его можно легко собрать в узел, к которому он принадлежит, чтобы выполнить функцию системы, с наименьшими затратами и сроками на сборку.
Проектирование под заданную стоимость (ПЗС) иногда называют проектированием для (удешевления) производства. Целью метода является понимание и оптимизация будущих производственных процессов продукта на этапах проектирования. В результате команда может минимизировать производственные затраты и максимизировать качество продукции.
ПЗС на базе системного подхода сегодня является основным инструментом для оптимизации затрат и эксплуатации предприятия. ПЗС рассматривают как интеграцию дизайна продукта и планирования процессов производства, чтобы разработать продукт, который можно было бы легко и экономично производить. Важность ПЗС подчеркивается тем фактом, что около 70% производственных затрат на продукт определяется его проектными решениями (стоимость материалов, обработка и сборка), а производственные решения составляют лишь около 20% затрат (например, планирование процесса или выбор станка).
В своей упрощенной форме ПЗС представляет собой правила и рекомендации проектирования, которые может применять конструктор, работая в единой связке с технологом. Также структурирована процедура оценки сборки узлов и продукта в целом. При оценке сложности производства продукта, часто используют время сборки и время изготовления в качестве количественного показателя. В продвинутых вариантах используют сочетание моделирования, производственного опыта, правил и анализа сборки, чтобы обеспечить малозатратную стратегию производства.
Характеристики «элегантного» ПЗС продукта, удовлетворяющего требования производителя и потребителя, включают следующие целевые позиции:
1) работоспособность, когда система выполняет желаемые функции с ожидаемым результатом;
2) робастность, если система не должна радикально отклоняться от ожидаемого поведения в ответ на реалистичные изменения входных условий (см. главу 5.2);
3) эффективность, чтобы получить желаемый результат при меньшем расходе ресурсов, чем конкурирующие альтернативы
4) живучесть, когда продукт выполняет намеченные цели при влиянии непреднамеренных действий, побочных эффектов и последствий;
5) простота архитектуры, а именно структурного расположения физических частей с существенной сложностью, модульность;
6) минимальная стоимость владения жизненного цикла, включая проектные, производственные, капитальные затраты, эксплуатационные расходы;
7) привлекательные свойства жизненного цикла продукта: надежность, безопасность, гибкость при изменении, ремонтопригодность, устойчивость к внешним воздействиям.
Проектирование любого компонента включает изучение требований к системе в целом. Требования к деталям, узлам, модулям, подсистемам должны каскадироваться и распределяться с верхнего уровня системы, потому что каждый элемент нужен для обеспечения одной или нескольких функций системы. Функционирование компонента в системе включает определение его конфигурации (например, формы, размеры, особенности), материалов и специальной обработки, такой как термообработка и покрытие поверхности для повышения ее долговечности. Функция компонента также будет зависеть от того, как функции его родительской системы распределяются между различными узлами внутри системы, и как компоненты взаимодействуют друг с другом. Под производством здесь понимается изготовление отдельной детали (или компонента) из заготовки. Включает использование таких операций, как штамповка, раскрой, ковка, литье и механическая обработка на станках.
Сборка относится к соединению деталей для формирования сборочных узлов или модулей. Процесс обычно включает сборщиков (рабочих), специальное оборудование или роботов, которые выполняют операции сборки: перемещение, позиционирование, вставку и выравнивание компонентов, их крепление с использованием сварки, клепки, фиксации с помощью винтов, гаек, болтов или нанесения клея.
Хотя пункты перечня кажутся очевидными, полезно помнить, что для снижения затрат на производство следует:
a) минимизировать количество деталей в продукте;
b) минимизировать количество этапов процесса;
c) использовать модульную конструкцию продукта;
d) упрощать сборку и удобства обслуживания (быстрое крепление, время сборки и разборки);
e) ужесточить планирование операций, не добавляющих ценности, таких как доработка и верификация (частота отказов при испытаниях, время ремонта, лишняя обработка, ненадежные детали);
f) проектировать с возможностью низких накладных расходов (упрощенные конфигурации, предпочтительные поставщики, минимальное количество подрядчиков, и т.д.);
g) проектировать с минимизацией затрат на тестирование жизненного цикла (устранить избыточность испытаний, комплексировать тесты, использовать эквивалентно-циклические испытания);
h) минимизировать жесткие допуски деталей, без ущерба качеству.
На начальном этапе нужно уделить внимание сравнительному анализу конкурирующих продуктов с целью сравнения их спецификаций, рассматривая как структуру, так и их стоимость. Можно сравнивать разбивку стоимости основного продукта со структурой каждого из его конкурентов, или с идеальным продуктом, включающим в себя самые дешевые подсистемы, выбранные у каждого из конкурентов. Также полезен статистический анализ стоимости аналогичных компонентов и подсистем, используемых в семействе продуктов, с оценкой путем построения диаграмм с координатами «цена-эффективность».
Оптимизация архитектуры продукта является самым эффективным этапом деятельности в разработке, где заложен наибольший потенциал для обеспечения успеха. Важность этого этапа часто игнорируют, просто предполагая, что архитектура продукта будет такой же, как у предыдущих или конкурирующих систем. Процесс оптимизации архитектуры начинается с предварительного согласования всех проектных соображений полной многофункциональной командой. Одна из главных причин неоптимальной архитектуры продукта выявляется на этапе создания макета, когда проверяют, как он работает. Ранее макеты для подтверждения функциональной осуществимости изготавливали из имеющихся подручных материалов наиболее быстрым способом. При этом не рассматривали оптимизацию архитектуры продукта и технологичность, полагая, что эти задачи будут выполнены позже. При переходе к электронному моделированию базовых версий продукта часто сохраняют цели устаревшего подхода.
Стратегии производства и цепочки поставок должны разрабатываться одновременно с оптимизацией архитектуры, для чего следует:
1. Заранее сформулировать стратегии обработки деталей и узлов, включая выбор процесса и потоки деталей и компонентов, план производства (что и где производится).
2. Определить стратегию пополнения запасов деталей и сырья, оформлять заказы на закупку на основе ресурсного планирования.
3. Оптимизировать решения по аутсорсингу и определить базу поставщиков деталей и материалов.
Известен из личной практики автора пример оптимизации парашютного замка для фиксации ранца на груди парашютиста, когда удалось на основании функционального системного анализа пересмотреть базовую архитектуру продукта и сократить количество деталей в сертифицированной конструкции с 46 до 7. Оптимизировать архитектуру полезно следующими ключевыми действиями:
• Сначала тщательно проанализировать «голос клиента» с оптимальными спецификациями проектирования и распределением ресурсов перед началом процесса разработки. Обязательно нужно понять и удовлетворить все требования клиентов к продукту, чтобы свести к минимуму вероятность будущих изменений.
• Далее проанализировать извлеченные уроки, чтобы понять, что в предыдущих проектах сработало хорошо, а что вызвало проблемы. Уроки разработки продукта, такие как причины заказов на изменения, задержки, перерасход бюджета, повторная квалификация и количественная оценка всех категорий затрат, влияют на общую стоимость владения продукта. Нужно учесть уроки преодоления трудностей при изготовлении, сборке, тестировании, обеспечении качества.
• Проблемы следует поднимать и решать сразу при их выявлении, сводя к минимуму вероятность запоздалого решения, когда каждое изменение будет реализовать труднее и дороже.
• Базовая архитектура должна быть упрощена за счет умных концепций, меньшего количества деталей, комбинаций деталей, более высокого уровня интеграции микросхем, модульных возможностей, и т. д. Она должна быть оптимизирована с точки зрения минимальной общей стоимости, качества и надежности, технологичности и удобства обслуживания, а также гибкости и возможности настройки.
• При выборе архитектуры желательно оптимизировать интеграцию деталей и их сборку, интерфейсы, проводку, кабели, взаимодействие деталей и подсистем.
• Определить уровень стандартизации, создавать стандартные списки типовых конструкторских решений и применяемых деталей. Использовать интерфейсы отраслевых стандартов или создать универсальные интерфейсы.
• Следует на раннем этапе сформулировать стратегии обеспечения качества, надежности, защиты от ошибок, тестирования, ремонта, обслуживания и испытаний.
• Полезно оптимизировать конфигурацию ПО, установив легкодоступные порты, добавить достаточно памяти для наиболее требовательной версии.
• Удобно использовать изменяемые модули, которые можно подключать к универсальным разъемам, предусмотрев достаточное количество этих разъемов.
• Наделить базовую конструкцию дополнительным пространством, монтажными отверстиями, дополнительными портами, разъемами и дополнительными служебными возможностями.
• Реальное время вывода продукта на рынок можно сократить почти вдвое за счет тщательной предварительной работы, потратив нужное время на оптимизацию архитектуры, вместо того, чтобы торопиться с этим этапом.
В ходе реализации ПЗС продукта следует:
1) оптимизировать все производственные функции изготовления, сборки, испытаний, закупок, доставки, обслуживания и ремонта;
2) обеспечить оптимальную стоимость, качество, надежность, соответствие нормативным требованиям, безопасность, время выхода на рынок и удовлетворенность клиентов;
3) гарантировать, что выбранные технологии удовлетворяют требованиям по функциональности, доставке продуктов, программе улучшения и не ограничивают рост выпуска;
4) выбрать оптимально материалы в конструкции;
5) использовать стандартизацию компонентов;
6) сокращать количество компонентов изделия;
7) применить проектирование компонентов для эффективной сборки;
8) минимизировать количество производственных и сборочных операций.
Приемы реализации ПЗС можно разбить на три части по фазам жизненного цикла разработки продукта. Первая часть относится к концептуальному проекту, вторая к рабочему проекту, а третья касается окончательных корректировок перед началом производства.
На стадии концепции выполняется проектирование, ориентированное на затраты. Здесь проектные решения и производственные затраты могут сыграть свою наибольшую роль. Методология учета затрат (см. главу 4.1) помогает команде разработчиков понять, в чем заключаются их слабые стороны в конкурентной борьбе, определяет, какие улучшения следует внести, чтобы получить успешный продукт, и определяет конкретные целевые показатели затрат. Этапы простого процесса показаны далее.
1. Определить продукт конкурента и провести анализ. Оценить продукцию конкурентов так, как если бы производили ее сами. Сравнить производительность предполагаемого нового продукта с новым продуктом конкурентов, который должен выйти в тот же срок. Целью будет получить либо лучшую производительность при аналогичной структуре затрат, либо аналогичную производительность при лучшей структуре затрат для нового продукта.
2. Разработать ориентировочный список запчастей для нового изделия, чтобы определить проблемные области стоимости в конструкции. Анализировать следует только ключевые элементы узлов сборки.
3. Проанализировать данные о затратах, определив разницу с конкурентами, и сравнить наихудший и наилучший случаи. Указать для исключения из работы области затрат, которые являются наименее конкурентоспособными.
4. Более подробно рассмотреть каждый из выбранных узлов с помощью матрицы анализа модификаций. Список деталей нового продукта сравнить со списком деталей конкурирующего продукта.
5. Далее определить типы изменений, которые необходимо осуществить в части дизайна, или процесса. Затем проанализировать каждую деталь, чтобы определить ключевые характеристики, которые делают затраты неконкурентоспособными, для исключения из работы.
6. Тестировать решения по затратам, чтобы определить, будет ли выбранный метод работать для достижения целевых затрат до начала проектирования. Для изменений конструкции это оценки, могут ли изменения конструкции привести к экономии затрат. Для изменений процесса это оценки количества запланированных процессов производства и объема технологических затрат. Следует принять решения по процессам, поставкам и проектированию, чтобы определить экономию затрат, и показать разработчикам, откуда, вероятно, произойдет снижение затрат.
7. После завершения выбора новые сметы затрат учитываются в стоимости инновационного продукта, чтобы установить бюджет себестоимости продукта для каждого узла сборки.
8. В итоге удобно на диаграмме показать текущие и прогнозируемые затраты, характеристики, которые необходимо изменить, подход коррекций дизайна и процесса, необходимые ресурсы и партнерские предложения.
Декомпозиция системы на модули является неотъемлемым качеством обеспечения ПЗС современных высокотехнологичных изделий. Она создает удобства при проектировании, производстве, обслуживании в эксплуатации. Вкратце требование модульности сводится к разработке подсистем (модулей) с разделенными целевыми функциями и исключением необходимости к пересечениям с другими подсистемами. Интерфейсы лучше делать простыми, и подобные функции собирать вместе. Модули должны быть взаимозаменяемыми в обслуживании, без воздействия на другие модули. Можно отметить некоторые характерные особенности модульного проекта:
• Желаемое построение системы включает модульные подсистемы или компоненты, которые характерны слабыми зависимыми связями, высокой плотностью и минимальными подключениями.
• Связями называют меру относительных зависимостей или информации, распределенных между подсистемами. Слабые зависимые связи между подсистемами позитивно влияют на устойчивость системы в целом, когда в подсистеме встречаются ошибки или изменения.
• Плотность модуля характеризует меру подобия задач, решаемых внутри подсистемы. Высокая унификация позволяет использовать идентичные или подобные модули, или применить один компонент, исполняющий мульти-функции.
• Подключения относятся к связям внутренних элементов двух разных модулей. Высокая связность нежелательна, так как порождает сложные интерфейсы.
• Удобно проектировать системы с большим количеством маленьких независимых, но взаимодействующих модулей.
• Изменение одного модуля не должно вынуждать изменения в других модулях.
• Модули должны иметь низкую внешнюю сложность (слабая связь) и высокую внутреннюю сложность (значимая плотность).
Подход ПЗС отдельного компонента включает удовлетворение всех требований, связанных с функциями и интерфейсами системы, к которой он принадлежит. Его форма, размер и габариты, материал, прочность и другие функциональные характеристики определяются проведением различных анализов, таких как:
а) анализ потребностей клиентов,
б) механический анализ, включая прочность, динамику и вибрации,
в) тепловой анализ, анализ воздушных и газовых потоков,
г) электрический анализ, включая сопротивление, ток, напряжение и емкости,
д) химические анализы, включающие коррозионную стойкость и токсичность,
е) долговечность для обеспечения необходимого количества рабочих циклов при указанных нагрузках и условиях окружающей среды.
Кроме того, требования к производству и сборке компонентов должны учитываться одновременно, включая переменные, связанные с производственными процессами, оборудованием, компоновкой рабочих мест, технологических линий, конфигурацией сборочного конвейера, и т. д.
При разработке продукта под заданную стоимость полезна реализация набора принципов, с упором на:
1. Определение продукта, которое должно отражать мнение потребителя, но при этом быть сформулировано в общих чертах, чтобы не ограничивать эффективные возможности дизайна.
2. Проработку выученных уроков, чтобы применить опыт аналогичных проектов, и определить вероятные источники чрезмерных потерь, таких как дефекты, доработка, брак, настройки, затраты на гарантию, и другие недостатки.
3. Оптимизацию архитектуры. Многофункциональная команда должна запланировать достаточно времени для творческого поиска идей и организации мозговых штурмов для поиска недорогих подходов к проектированию, стратегий производства и снабжения.
4. Снижение затрат на электронику за счет определения более высокого уровня интеграции, модульности, исключения ручной проводки и пайки, объединения печатных плат, замены всех разъемов печатной платы слоями между платами, и др.
5. Для изготовления узлов сложной формы эффективно применение аддитивных технологий, чтобы исключить стыковки отдельных деталей.
6. Назначение оптимальных допусков деталей для производства, как одного из ключевых элементов стратегии экономии стоимости.
7. Сокращение накладных расходов.
8. Сокращение бюджета на разработку продукта. Применение параллельного инжиниринга позволяет заметно сократить потребное количество человеко-часов. Также необходимо учесть, что корректирующие действия для решения проблем качества, ресурса и надежности продолжают оплачиваться из бюджета ОКР до тех пор, пока они не будут решены. Эффективный подход к пошаговой верификации решений позволит сэкономить значительную долю общих затрат бюджета.
9. Использование программы качества типа «Шесть сигм» для эффективного снижения затрат на обеспечение качества. Системный подход к разработке продукта может обеспечить качество с минимумом затрат.
10. Формирование команды квалифицированных и опытных технических кадров с привлечением специалистов по проектированию, производству, сборке, маркетингу и финансам для обеспечения учета требований и свойств продукта при разработке всех его компонентов.
11. Следует минимизировать количество компонентов. Если компоненты можно комбинировать, количество этапов и время установки при сборке можно сократить.
12. Полезно уменьшить количество и номенклатуру креплений. Крепежи могут составлять всего лишь около 5% прямых затрат на материалы изделия, но все связанные с ними трудозатраты могут достигать 75% общих затрат на сборку. Установка крепежа занимает много времени и добавляет затраты на сборку и обслуживание.
13. Нужно обсудить применяемые типы крепежа. Если замена или ремонтопригодность компонентов не планируются, то гайки и болты можно заменить заклепками или сварными швами. В роботизированной ячейке сварка компонента может ускорить сборку.
14. Симметричный компонент сократит время сборки по сравнению с асимметричным. Следует использовать выраженные асимметричные элементы, чтобы гарантировать единственный вариант ориентации компонентов при сборке.
15. Рекомендуется избегать очень маленьких или больших компонентов. Их трудно захватывать, подавать и обрабатывать, а сборка занимает больше времени.
16. Глухие отверстия с плотной посадкой деталей должны иметь проход для сброса воздуха, чтобы уменьшить усилие вставки.
17. Компонент должен быть сконструирован так, чтобы его не нужно было прижимать во время сборки до закрепления. Это устранит трудности с удержанием компонента при ручной и роботизированной сборке.
18. Для выравнивания деталей можно использовать направляющие штифты и специальные выступы.
19. Следует обеспечить в проекте достаточные зазоры для инструментов или пальцев для вставки, чтобы сократить время монтажа и обслуживания. Важен доступ к инструментам и оператору инструмента, будь то рабочий или рука робота, для которого обычно требуется больше места для доступа, чем для руки рабочего.
20. Удобно использовать вставку компонентов сверху, подавая их под действием силы тяжести.
При проектировании разработчики должны формировать технологичный продукт, адаптируя его под производственные возможности предприятия. Технологичностью называют набор свойств конструкции, характеризующих возможность ее производства, с уклоном в минимизацию затрат при производстве и эксплуатации при заданных показателях характеристик, качества, объемов выпуска и условий производства.
Технологичность производственная включает обеспечение технологичности деталей и сборочных единиц. Для получения технологичности (качества и скорости монтажа) сборочной единицы важны модульность конструкции, простота и надежность соединения. Дополнительные условия включают снижение сложности и количества конструктивных особенностей, таких как прорези, ступени или канавки для обработки, количество переходов, этапов и рабочих мест в производстве и сборке компонентов, число инструментов, приспособлений, роботов, а также время, необходимое для настройки и переналадки инструментов и станков.
Эксплуатационная технологичность включает эффективное решение задач ремонтопригодности, адаптации к удобному и безопасному обслуживанию, подготовки обслуживающего персонала, оптимизации норм расходования эксплуатационных материалов, минимизации воздействия на окружающую среду, простоты хранения, транспортировки, и др.
В стоимость изготовления и сборки входят статьи:
а) стоимость сырья и заготовок, необходимых для производства компонента;
б) стоимость производственного процесса, включая капитальные и эксплуатационные затраты на технологическое оборудование при требуемой производительности в таких процессах, как литье, ковка, штамповка, механическая обработка и покраска;
в) стоимость сборки для установки компонента, включая затраты на доставку, ориентацию и размещение компонента на базовой подсборке, и его крепление;
г) прямые затраты на оплату труда;
д) косвенные затраты на оплату труда, например, для технического обслуживания;
е) стоимость запчастей, закупленных у поставщиков;
ж) накладные расходы на страхование, управленческий персонал, и др.
Проектирование под заданную стоимость и связанная с этим качественная проработка технологий изготовления позволяет снизить категории проблемных затрат, связанных с развертыванием производства, специальным оборудованием, сложными техпроцессами изготовления деталей, неэффективной сборкой, чрезмерным увеличением количества деталей, трудоемкими закупками, многочисленными изменениями и повышенными накладными расходами. Эти проблемы не только повышают стоимость, но и задерживают поставки. Плохая технологическая проработка также снижает качество, что увеличивает затраты и задерживает реальный срок выхода на рынок. Чрезмерное увеличение количества деталей может затруднить внедрение прогрессивных технологий бережливого производства «точно в срок», сборки на заказ и массовой настройки выпуска продукта.
Команда должна избегать неэффективных действий. К ним относятся аутсорсинг производства вдали от контроля инженеров, попытки снижения затрат после проектирования, и усреднение накладных расходов. Общая стоимость должна быть основой, тем важнее правильно ее измерить. Раннее рассмотрение производственных проблем сокращает время и минимизирует затраты на разработку, обеспечивает плавный переход к производству для максимально быстрого выхода на рынок в режиме реального времени.
При выборе производственных процессов ПЗС важно принять во внимание следующие соображения:
1. Производство многих компонентов требует последовательности различных технологических процессов и операций для достижения требуемых свойств конечной детали. Выбор техпроцесса для любого компонента будет зависеть от его функции, рабочей среды и циклов использования, а также материалов, выбранных инженерами.
2. Форма, прочность, масса, электропроводность, способность выдерживать уровень температуры, оптические свойства, текстура, должны быть учтены при выборе возможностей производственных процессов для производства продукции с постоянным уровнем качества.
3. При планировании производства следует учесть количество компонентов, использование стандартизованных единиц, необходимое количество комплектов и заданные темпы производства.
4. Необходимо работать над снижением общих производственных затрат.
Нужно уделять внимание заметно влияющему на стоимость вопросу назначения допусков деталей при изготовлении. Сумма допусков представляет собой совокупный эффект всех допусков, комбинация которых влияет на один и тот же общий размер. Допуск наихудшего случая означает объединение «наихудших» из всех допусков для анализа того, каким будет конечный эффект. Продукт должен быть способен функционировать надежно и безопасно во всех наихудших ситуациях сложения допусков. Анализ комбинаций допусков следует проводить в процессе проектирования на соответствующих комплектах деталей, модулях и узлах сборки, а также на сборочной модели самого изделия. Важно в процессе разработки максимально снижать влияние допусков деталей на характеристики продукта:
a) применить проектирование для упрощения процедур собираемости;
b) иметь таблицы данных деталей для анализа;
Правообладателям!
Это произведение, предположительно, находится в статусе 'public domain'. Если это не так и размещение материала нарушает чьи-либо права, то сообщите нам об этом.