Текст книги "Инновации от идеи до рынка"
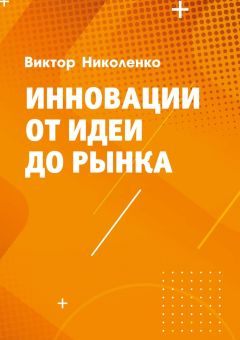
Автор книги: Виктор Николенко
Жанр: Прочая образовательная литература, Наука и Образование
Возрастные ограничения: +16
сообщить о неприемлемом содержимом
Текущая страница: 23 (всего у книги 32 страниц)
Глава 5.
Улучшение потребительских свойств
5.1 Управление качеством проектов ОКР
На разных этапах управления жизненным циклом продукта важнейшую роль играет система менеджмента качества (СМК). Принципы управления качеством в части обеспечения разработок и эксплуатации новой техники сегодня являются неотъемлемой частью создания инновационных изделий, деятельности предприятий и проектных команд. Они затрагивают:
1. Финансовые ресурсы организации.
2. Коммуникации.
3. Время, скорость и соответствующие аспекты проектов.
4. Лидерство руководства.
5. Согласованность с практикой управления бизнесом.
6. Подход, основанный на разумной оценке риска.
7. Управление жизненным циклом.
8. Цепочку поставок.
9. Фокус на соответствие продукции требованиям.
10. Результаты процесса и поставок по вехам.
11. Поддержание инфраструктуры.
12. Менеджмент процессов реализации проектов.
13. Управление знаниями.
14. Внедрение инструментов обеспечения качества.
15. Структуру СМК и стандартов менеджмента.
16. Технологии информационного менеджмента.
Качество определяется клиентами. Их потребности и восприятие продукта могут сильно различаться. Приведем некоторые общеупотребительные определения качества.
• Качеством называют совокупность свойств и характеристик продукта или услуги, которые связаны с их способностью удовлетворять заявленные или предполагаемые потребности сейчас и в будущем.
• Качеством называют уровень удовлетворенности и лояльности клиентов.
• Детальное определение качества продукции принято основывать на следующих параметрах:
а) производительность: способность продукта выполнять свои основные функции;
б) эффективность: функции продукта, которые соответствуют применимым правилам, повышают его полезность, комфорт и удобство;
в) надежность: способность продукта работать без сбоев с течением времени;
г) ремонтопригодность: возможность производить ремонт быстро и по разумным ценам;
д) восприятие бренда: впечатление о качестве, создаваемое продуктом в мнении покупателя;
е) другие измерения качества: совершенство, постоянство, устранение отходов, скорость доставки, соблюдение политик и процедур, предоставление хорошего пригодного для использования продукта, удовлетворение клиентов, качественное обслуживание в эксплуатации.
Качество является одним из ключевых показателей продукта, который представляет общий интерес как для производителя, так и для покупателя. Можно выделить две составляющих этого фактора:
1. Качество, ориентированное на клиента, например, функция, внешний вид, цвет, удобство пользования, то есть удовлетворение выраженных и скрытых требований клиента.
2. Инженерное качество. Обеспечить свободу продукта от негативных параметров, неугодных заказчику, например, от шума, вибраций, отказов, и т. д. В частности, робастное проектирование может сделать функциональность технологии и продукта максимально приближенной к идеальному состоянию, и избежать различных проблем с качеством, возникающих на последующих этапах.
Издержки, связанные с качеством продукта, можно разделить на внутренние и внешние.
Внутренние затраты на обеспечение качества включают бюджеты видов деятельности, не добавляющие стоимости продукту (испытания, брак, диагностика, доработка, повторная проверка доработок, закупочные действия для приобретения запасных материалов и деталей, анализ проблем с качеством, стоимость корректирующих действий, затраты на качество, вызванные изменениями), и требующие трудозатрат, чтобы исправить дизайн.
Внешние затраты на качество включают стоимость рассмотрения жалоб клиентов, возврата средств и товаров, ремонта товаров, гарантийных претензий, затраты на исправления, юридические обязательства, контроль повреждений, штрафы и корректирующие действия, плохую рекламу компании, испорченную репутацию, и потерю доли продаж. Убытки из-за плохого качества продукции определяются стоимостью поиска и устранения дефектов, а также связанных с этим затрат. Компании без надежных программ управления качеством могут понести лишние затраты по этой статье в пределах 15…40% дохода.
Сегодня некоторые корпорации стремятся как можно быстрее выпустить и реализовать продукты возобновляемой энергетики. Датская фирма Vestas занималась гарантийным ремонтом вышедшего из строя оборудования поставленных клиентам ветроэлектростанций на протяжении трех лет подряд. Компания Siemens Gamesa после неудачного слияния попыталась оказывать предпочтение темпам роста за счет качества продукции. В итоге, за 2022 г. гарантийное обслуживание на установленных компанией объектах стоило €920 млн. чистых убытков. В 2023 г. из-за многочисленных случаев производственного брака и возможных ошибок в дизайне оборудования Siemens оценил ликвидацию последствий в разработке и на производстве в сумму €1 млрд. Как можно видеть, сокращение сроков поставок за счет потери качества ведет к заметным финансовым и имиджевым потерям для изготовителя инновационных продуктов.
Отметим некоторые важные результаты обеспечения качества продукта. Оно напрямую связано с успешностью бизнеса компании, так как относится ко всем процессам, является не просто набором правил, а нормой жизни предприятия, все люди и процессы должны быть вовлечены в улучшение продукции. Планирование, контроль и повышение качества являются тремя взаимосвязанными процессами в управлении качеством. СМК должна служить для предотвращения дефектов, а дизайн продукта и процесса должен быть защищен от воздействия неконтролируемых факторов; то есть продукты должны быть разработаны с учетом робастности и живучести (см. главу 5.3).
Основная роль обеспечения качества заключается в подготовке планов и процедур для выполнения задач проектирования и разработки. Эти планы должны быть задокументированы, одобрены службой качества организации, поддерживаться и обновляться по мере необходимости. Проведение периодических проверок для доказательства соблюдения планов и процедур гарантирует, что работа по проектированию систем осуществляется в соответствии с утвержденным процессом.
Для обеспечения качества планируют следующее:
• определить цели и стандарты обеспечения качества;
• сосредоточиться на профилактических мерах, а не на излечении дефектов;
• собирать статистику и использовать данные для анализа результатов;
• устанавливать и контролировать показатели качества;
• проводить аудиты качества на рабочих местах.
Большинство показателей качества являются субъективными. Конечным оценщиком качества продукта является потребитель. Объективные показатели также могут использоваться, если они связаны с восприятием качества или удовлетворенностью потребителя. Например, в промышленности используются стоимостные показатели качества. Они основаны на подсчете затрат, связанных с качеством:
a) затраты на профилактику (например, затраты, связанные с рассмотрением проекта, обучением и анализом);
b) затраты на оценку качества (например, затраты на инспекции, испытания и аудит);
c) внутренние затраты на отказ (например, расходы, связанные с гарантийной доработкой и ремонтом на площадке изготовителя);
d) внешние затраты на отказ (например, возврат некачественных продуктов, рассмотрение жалоб клиентов и расходы, связанные с ремонтом, когда продукт используется клиентами).
Ниже приведены примеры часто используемых показателей качества легковых автомобилей:
1. Процент клиентов, довольных транспортным средством.
2. Количество обнаруженных клиентами дефектов на транспортное средство.
3. Количество всех поломок на 100 проданных автомобилей.
4. Количество гарантийных ремонтов на 100 проданных автомобилей.
5. Относительное количество изделий, возвращенных в ремонт.
6. Оценки удовлетворенности клиентов (например, по 5-балльной шкале).
Один из основополагающих принципов качества: покупатель всегда прав. Поэтому фокус на требования потребителей является ключевым элементом. Качество должно быть встроено в продукт на самом раннем этапе его проектирования. Поздно и дорого реагировать на устранение любых дефектов, возникающих после выхода продукта на рынок. Все группы разработчиков продукта должны стремиться к созданию качества, разрабатывая продукт, который хотел бы клиент, на основе принципов системного подхода. В системах управления менеджментом качества отметим два хорошо разработанных направления по внедрению качества в продукты и процессы. К первому относятся стандарты ISO 9000 для организаций. Вторым из многочисленных инструментов можно рекомендовать методологию разработки и улучшения качества продукта «Шесть сигм». Вышеуказанные подходы дополняют друг друга, и организация, стремящаяся улучшить качество, может реализовать любой из них.
ISO 9000 представляет собой серию стандартов качества, разработанных Международной организацией по стандартизации (ISO) для облегчения международной торговли на базе общего набора стандартов СМК. Они включают все важные политики, процедуры, планы, ресурсы, процессы, а также разграничение ответственности и полномочий организации. Все это направлено на достижение уровней качества продукции или услуг, соответствующих удовлетворенности потребителей и целям компании. Предприятия разрабатывают систему качества и следуют ей в работе для повышения качества своих продуктов и услуг. Версии стандартов качества с 2015 г. унифицированы с подходами и стандартами системной инженерии.
Основные принципы СМК, предусмотренные в системе стандартов ISO 9000:
A. Ориентация на потребителя. Организации зависят от своих клиентов и поэтому должны понимать текущие и будущие потребности клиентов, выполнять требования клиентов и стремиться превзойти их ожидания.
B. Лидерство. Лидеры должны создавать и поддерживать внутреннюю среду, в которой люди полностью вовлечены в достижение целей организации.
C. Вовлечение людей. Люди на всех уровнях составляют основу организации, и их полное вовлечение позволяет эффективно использовать их способности в организации.
D. Процессный подход. Желаемый результат достигается более эффективно, когда деятельность и связанные с ней ресурсы управляются как процессы.
E. Постоянное улучшение. Базовой целью организации должно быть улучшение общей деятельности.
F. Принятие решений на основе фактов. Эффективные решения основаны на анализе данных и информации.
G. Эффективное управление взаимовыгодными отношениями с поставщиками, которые повышают способность обоих сторон создавать ценность.
Методология «Шесть сигм (sixsigma)» является системой создания устойчивых улучшений в производственных и других повторяющихся процессах с использованием статистических методов. Используется для устранения потерь и улучшения качества, затрат и времени в любом бизнесе. В основу положено достижение удовлетворенности клиентов за счет производства продуктов и услуг с меньшим разбросом характеристик.
В исходном смысле так названа борьба за снижение типовой характеристики дефектности продукции, числа дефектов на миллион событий или единиц продукции. В производственном процессе продукция, не соответствующая требованиям потребителя, отбраковывается и отправляется на доработку, а продаваться может только та, которая не имеет дефектов. При нормальном статистическом распределении погрешностей значения случайной величины должны лежать в пределах шести сигм с очень высокой вероятностью. Стандартное нормальное распределение для «коридора» разброса параметров (шириной три сигмы) дает 66 тысяч дефектов на миллион деталей, т.е. выходов параметра за границы коридора, тогда как количество дефектов при шести сигм равно всего 3,4. Для любой операции или на любом шаге процесса можно определять количество дефектов. Например, отсутствие реакции на запрос заказчика в течение интервала четырех часов, ошибка в заказе на покупку, неправильно оформленный счет на услугу, и т. д. Можно также определять дефекты в цепи процессов, связанных с внутренними и внешними заказчиками. Цель шести сигм нигде пока не достигнута, фирмы General Electric, Motorola анонсировали текущее достижение рубежа 4.5 сигм.
Философия «Шесть сигм» направлена на снижение неэффективного использования ресурсов и неоптимальных процессов, используя применение инновационных цифровых технологий. Популярный вариант такого подхода в процессе развития назван Lean SixSigma, где интегрированная концепция объединяет две методологии управления качеством. Одна из них, бережливое производство, сфокусирована на устранении потерь и непроизводительных затрат (см. главу 4.4). Другая, «шесть сигм», ориентирована на снижение вариантов процессов и стабилизацию характеристик продукции.
Исторически реализованный первым базовый процесс «Шесть сигм» (DMAIC), направлен на улучшение качества серийного продукта. Позже появилась вторая процедура «Дизайн для шести сигм» (DFSS) для создания исходного продукта с высокими характеристиками качества. В соответствии с этапами жизненного цикла сегодня последовательность применения методологии такова. На этапе разработки используют DFSS, «Дизайн для шести сигм», комплексную систему синтеза нового продукта, удовлетворяющего критерию. На этапе производства применяют DMAIC, процесс по развитию выпускаемого серийно продукта, ориентированный на непрерывное совершенствование производства или услуг. Используется при решении локальных задач улучшения системы, когда они уже сформулированы, и выполнена обработка располагаемых статистических данных.
Для решения конкретных задач технологии «шести сигм» разработаны «поваренные рецептурные книги (cookbook)», содержащие детали описания шагов реализации процесса, для получения эффективного результата.
Базовая часть «Дизайна для шести сигм» включает применение шагов стратегии, концепции, процесса и инструментария. Стратегию используют для разработки новых и лучших продуктов или процессов. Сначала необходимо услышать и принять к исполнению «голос клиента». Концепция включает реализацию задачи проекта и проверки с упором на предотвращение вероятных проблем. Процесс содержит перевод «голоса клиента» в технические требования, оптимизацию влияющих факторов для достижения высокого уровня качества продукта или услуги.
После того, как продукт создан, для повышения качества производства используется набор инструментов DMAIC и вторая «поваренная книга». Целью данного этапа является сокращение отклонений в ходе производственного процесса и его совершенствование путем реализации проекта «Шесть сигм». Выделена последовательность шагов «определить – измерить – анализ – улучшение – контроль». Постановка проблемы сфокусирована на выходные данные и целевые значения характеристик. Частые дефекты есть следствие плохого процесса, который нужно изменить. Результат достигается на шаге улучшения, где проводится установление рабочих допусков, поверка измерений и доработка процессов. В заключение проводится контроль результатов процесса для критических входных данных.
Обеспечивается выполнение процедур с применением аналитических инструментов на основе фактических данных и методик, для предотвращения возникновения дефектов, ненужных процессов и услуг. Для количественных оценок применяется в основном пакет программ статистического анализа «Minitab». Подробное описание методологии можно найти в ГОСТ Р ИСО 13053-1-2015 и ГОСТ Р ИСО 13053-2-2015 «Статистические методы».
Важным дополнением стандарта ГОСТ Р ИСО 9001—2015 «Системы менеджмента качества, Требования» является ГОСТ Р 58876—2020 «Системы менеджмента качества организаций авиационной, космической и оборонной отраслей промышленности» (на основе набора международных стандартов AS/EN 9100), который определяет требования качества для аэрокосмической промышленности и оборонных предприятий. Он является рекомендованной моделью качества при проектировании, разработке, производстве, монтаже и обслуживании, и может использоваться при создании инновационных продуктов в других высокотехнологичных отраслях.
Цели стандарта включают:
1) обеспечение высокого качества и безопасности продукции в аэрокосмической отрасли с всемирно признанным уровнем качества;
2) выполнение специфических требований потребителей, включая требования к оценке поставщика финальной продукции;
3) выполнение требований государственных органов по принадлежности;
4) оптимальное использование взаимодействия по всей цепочке поставщиков по предотвращению и снижению дефектов;
5) повышение стабильности партнерских процессов между интеграторами системы, поставщиками и субподрядчиками;
6) систематизированный анализ поставщиков.
Существенные специфические требования стандарта унифицированы с требованиями системного подхода к разработке новых продуктов:
• управление рисками;
• управление документацией;
• конфигурационный менеджмент;
• проектная документация;
• планирование;
• валидация;
• верификация;
• управление закупками;
• планирование и осуществление производства;
• испытание первого образца;
• аварийный план в случае поставки несоответствующей продукции;
• установление полномочий участников работ;
• документальное подтверждение уничтожения бракованных частей.
Отметим, что крупные компании выпускают свои дополнения к данному стандарту качества для поставщиков. В них они отражают специфические требования к поставкам используемой номенклатуры ПКИ, с учетом статистических результатов опыта предыдущей работы с подрядчиками.
Управление качеством при разработке новых продуктов обеспечивает решение следующих основных проблем:
• Повышение производительности, чтобы справиться с конкуренцией. Продуктивность ОКР определяется как ключевое свойство продукта легче удовлетворять потребности рынка в разнообразии продукции и более высоком уровне качества, предотвращать потенциальные проблемы с качеством за счет раннего прогнозирования, эффективно накапливать знания и снижать затраты на разработку продукта.
• Поставка качественных деталей с первого предъявления, с целью экономии времени и средств.
• Управление циклом разработки в среде цепочки поставок.
• Создание привлекательного качества продукта за счет удовлетворения скрытых требований клиентов.
Для реализации современных инновационных ОКР с требуемым уровнем качества рекомендуется:
1. Использовать в разработке зрелую технологию. Применение непроверенной и неподтвержденной технологии или новых материалов создает огромный риск для успеха создаваемой системы.
2. Полезно для успешного продукта применять модульную разработку с использованием покупных готовых блоков, а также использовать открытые архитектуры и модульные концепции, четкое определение системных интерфейсов и применение отраслевых стандартов.
3. На старте работ нужно фиксировать определенный набор достижимых требований, ориентированных на потребности заказчика. Следует отдавать приоритет реалистичному решению проблемы в сжатые и достижимые сроки. Бесконечное, дорогостоящее стремление к идеальному решению, с более длительным и часто плохо прогнозируемым сроком достижения цели, как правило, заканчивается неудачно.
4. Рекомендуется использовать в управлении проектом процессы технических обзоров и контрольные аудиты. Основное внимание уделяется документированию важной технической и программной информации и аргументов принятия базовых решений.
5. При конструировании следует принять некоторый разумный уровень рисков. Попытка управлять всем возможным набором рисков является трудоемким и дорогостоящим, нереалистичным процессом.
6. Менеджер должен создать и поддерживать доверие в команде проекта. Это критическая основа командной работы, без которой невозможно эффективно сотрудничать. Следует регулярно делегировать полномочия по принятию решений на самом низком уровне, на котором существует достаточная информация и знания для принятия решения. Это сокращает процесс, уменьшает время ожидания и способствует установлению уверенности в коллегах.
7. Постоянно пополнять багаж участников команды конкретными навыками и опытом. Сотрудники должны понять, что такое правила проекта, где расположена управленческая документация по работе, и какие правила или процессы применяются к ситуации. Необходимо в процессе работы обучать и готовить экспертов высокого уровня со специфическими навыками и опытом. Также следует поощрять обучение текущим вопросам для всех участников команды. Проект является коллективным видом спорта, для достижения успеха линию финиша должны пересечь все сотрудники.
Для наших инженеров отраслевые справочные издания публикуются сегодня только фрагментарно, а большинство справочников времен СССР в XXI веке не актуализировались, и не переиздавались. Нет информационных сборников в цифровом формате, медленно развиваются базы знаний предприятий, выкладываемые в интернет. Разрушено в угоду вступления в ВТО обязательное применение системы ГОСТов, десятилетиями обобщавших текущий отраслевой и мировой опыт с учетом аналогичных зарубежных материалов. Многие стандарты серии MIL с большим объемом полезной технической информации до недавнего времени были доступны в Интернете. Сегодня на ряд зарубежных сайтов с подобной информацией вход из российского сегмента Интернета закрыт. По сути, международное разделение труда для РФ свелось к заимствованию худшей части «западной» системы со странным опасением «Вдруг приедут и спросят?» Тогда как, например, проверенный зарубежный опыт массовой разработки и производства гражданской авиационной техники никто у нас не спешит ассимилировать. Российские высокие технологии конкурентоспособны на рынке, что доказано неоднократно в разных отраслях. В моей практике руководителя совместных инженерных центров c промышленными лидерами General Electric и Airbus нашим инженерам всегда поручали сложные творческие задачи. Неоднократно удавалось удивлять признанных профессионалов мирового уровня, подробности см. в книге [7]. Наставники должны предлагать сотрудникам на проекте интересные работы в рамках «личных творческих планов» (терминология времен СССР не устаревает).
8. Поддерживать высокие уровни мотивации и ожиданий в команде. Работа в проекте на протяжении всего жизненного цикла, от определения концепции до разработки и запуска в эксплуатацию способствует профессиональному росту. Полезно регулярно обсуждать, что пошло не так, и изучать «извлеченные уроки», чтобы предотвратить появление тех же ошибок в последующих итерациях текущего проекта и в будущем.
Требования качества являются важным разделом контроля исполнения проектов на технических обзорах. Для прохождения каждых контрольных рубежей проекта (ворот принятия решений) должна быть собрана и представлена в требуемом для обзора формате необходимая информация по качеству работ на проекте:
a) ведение учетных записей проекта;
b) подготовка материалов плана качества;
c) разработка и внедрение недостающих процессов проекта;
d) подготовка листов проверки чертежей, 3-Д моделей и сборок;
e) развитие шаблонов документов;
f) ведение статистики несоответствий;
g) разработка ТПЭ проекта и статистика показателей;
h) подготовка ежемесячных отчетов с анализом мероприятий;
i) подготовка и проведение регулярных аудитов;
j) актуализация основных документов СМК (при необходимости).
Традиционные инструменты качества можно использовать на проектах в различных комбинациях. Литературу по ним можно найти в сети Интернет.
Правообладателям!
Это произведение, предположительно, находится в статусе 'public domain'. Если это не так и размещение материала нарушает чьи-либо права, то сообщите нам об этом.