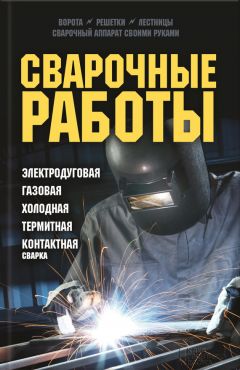
Автор книги: Юрий Подольский
Жанр: Техническая литература, Наука и Образование
Возрастные ограничения: +12
сообщить о неприемлемом содержимом
Текущая страница: 3 (всего у книги 25 страниц)
Основным инструментом газосварщика является сварочное пламя. Оно образуется при сгорании горючего газа в кислороде. От соотношения объемов кислорода и горючего газа в их смеси зависят внешний вид, температура и характер влияния сварочного пламени на расплавленный металл.
Рассмотрим строение пламени (рис. 10). Сварочное пламя имеет три четко различимые области: ядро, восстановительную зону и факел.
Ядро пламени представляет собой ярко светящуюся зону, в наружном слое которой сгорают раскаленные частицы углерода, образующиеся при разложении ацетилена.
Восстановительная зона, более темная, состоит из оксида углерода и водорода, которые раскисляют расплавленный металл, отбирая кислород от его оксидов.
Факел – периферийная часть пламени – представляет собой зону полного сгорания углеводородов в кислороде окружающей среды.
В зависимости от соотношения объемов кислорода и ацетилена получают три основных вида сварочного пламени: нормальное, окислительное и науглероживающее.

Рис. 10. Строение и виды ацетиленового сварочного пламени, распределение температуры по длине факела:
а – нормальное; б – окислительное; в – науглероживающее; 1 – ядро; 2 – восстановительная зона; 3 – факел
Нормальное сварочное пламя образуется тогда, когда в горелке на один объем кислорода приходится один объем ацетилена. В нормальном пламени ярко выражены все три зоны. Ядро имеет резко очерченную форму, близкую к цилиндру, с ярко светящейся оболочкой. Температура ядра достигает 1000 °C.
В восстановительной зоне, содержащей продукты неполного сгорания ацетилена, проводят сварку. Температура этой зоны в точке, отстоящей на 36 мм от ядра, составляет 3150 °C. Факел имеет температуру 1200–2500 °C.
Нормальным сварочным пламенем осуществляют сварку сталей всех марок, меди, бронзы и алюминия.
Окислительное сварочное пламя получают при избытке кислорода, когда в горелку подают на один объем ацетилена более 1,3 объема кислорода. Ядро такого пламени имеет укороченную, конусообразную форму. Оно приобретает менее резкие очертания и более бледную окраску, чем у нормального пламени. Протяженность восстановительной зоны уменьшается по сравнению с нормальным пламенем. Факел имеет синевато-фиолетовую окраску. Горение сопровождается шумом, уровень которого зависит от давления кислорода. Температура окислительного пламени выше, чем у нормального, однако при сварке таким пламенем из-за избытка кислорода образуются пористые и хрупкие швы.
Окислительное пламя применяют при сварке латуни и пайке твердыми припоями.
Науглероживающее сварочное пламя получают при избытке ацетилена, когда в горелке на один объем ацетилена приходится не более 0,95 объема кислорода. Ядро такого пламени теряет резкость очертаний, на его конце появляется зеленый венчик, по наличию которого судят об избытке ацетилена. Восстановительная зона существенно светлее, чем у нормального пламени, и почти сливается с ядром. Факел приобретает желтую окраску. При значительном избытке ацетилена пламя коптит. Температура науглероживающего пламени ниже, чем у нормального и окислительного.
Слегка науглероживающим пламенем сваривают чугун и осуществляют наплавку твердых сплавов.
Регулируют и устанавливают вид сварочного пламени «на глаз».
При выполнении сварочных работ необходимо, чтобы сварочное пламя обладало тепловой мощностью, достаточной для расплавления свариваемого металла. Ее выбирают в соответствии с толщиной свариваемого металла и его теплофизическими свойствами. Эта мощность зависит от расхода ацетилена – объема газа, проходящего за один час через горелку, поэтому ее регулируют ацетиленовым вентилем и подбором наконечника горелки.
Расход ацетилена (его измеряют в дм3/ч), необходимый для расплавления слоя свариваемого металла толщиной 1 мм, устанавливают на практике. Так, слой низкоуглеродистой стали толщиной 1 мм расплавляется при расходе ацетилена 100–130 дм3/ч. Чтобы определить расход ацетилена при сварке конкретной детали, нужно умножить расход, соответствующий единичной толщине, на действительную толщину свариваемого металла (мм).
При сварке низкоуглеродистой стали толщиной 3 мм минимальный расход ацетилена составит 100 ∙ 3 = 300, а максимальный – 130 ∙ 3 = 390 дм3/ч.
Решающую роль в процессе горения играет кислород. Для полного сгорания одного объема ацетилена требуется два с половиной объема кислорода. Однако при газовой сварке недопустимо смешивать ацетилен с кислородом в такой пропорции, чтобы обеспечить полное сгорание ацетилена. Как правило, на один объем ацетилена подают 1,1–1,2 объема кислорода.
Для предотвращения окислительных процессов при газовой сварке в присадочные материалы и флюсы вводят вещества, которые раскисляют металл[11]11
Раскисление – процесс удаления кислорода из сварочной ванны, одна из основных операций рафинирования металлов (рафинирование – процесс очистки металлов от примесей).
[Закрыть], например кремний и марганец, которые имеют большее сродство к кислороду, чем металл шва. При сварке стали раскисляющее действие оказывают углерод, его оксид и водород, образующиеся при горении газовой смеси. Поэтому углеродистые стали можно сваривать и без флюса. Соответствующие присадочные материалы и флюсы применяют и для легирования металла шва.
При газовой сварке основной металл, примыкающий к сварному шву, подвергается нагреву до температуры 1500 °C. Область, нагретую до 450—1500 °C, принято называть зоной термического влияния. Общая протяженность околошовной зоны при газовой сварке, зависящая от толщины и марки стали, составляет 6—30 мм. Эта область склонна к образованию холодных и горячих трещин.
Для предупреждения образования холодных трещин рекомендуется применять сварочные материалы с минимальным содержанием фосфора и проводить сварку на оптимальных режимах.
Для предотвращения образования горячих трещин необходимо применять сварочные материалы с повышенным содержанием марганца и минимальным количеством серы и углерода, вводить в металл шва легирующие элементы (титан, алюминий, медь), выполнять сварку с предварительным подогревом и последующей термообработкой.
Кроме того, для улучшения структуры и свойств зоны термического влияния и металла шва, выполненного газовой сваркой, осуществляют горячую проковку[12]12
Проковка – механическое воздействие молотком или кувалдой на металл шва как в горячем, так и в холодном состояниях. Проковка улучшает механические свойства наплавленного металла и в значительной степени уменьшает усадку.
[Закрыть] шва, его термообработку (нагрев сварочной горелкой) и общую термообработку сварного изделия (нагрев в печах с последующим медленным охлаждением).
Технология сварочных работ

Под техникой сварки понимают приемы манипулирования электродом или горелкой, выбор режимов сварки, приспособлений и способы их применения для получения качественного шва. Однако качество швов зависит не только от техники сварки, но и от других факторов, таких как состав и качество применяемых сварочных материалов, состояние свариваемой поверхности, качество подготовки и сборки кромок под сварку.
Подготовительные слесарные операции
Благодаря доступности электроинструментов в наше время работы по раскрою и подготовке металла к сварке значительно упростились. Фактически с помощью одной только углошлифовальной машинки в большинстве случаев можно быстро раскроить материал, опилить фаски, а затем и зачистить сварные швы. Но болгарка выручает не всегда. Для работы в узких местах, при сложной конфигурации исходного материала, его малых размерах и т. п. она неудобна. Например, прорезать болгаркой небольшое окно в металлическом листе, не захватывая лишний материал, не получится. Тонкий металл из-за высокой скорости вращения отрезного или шлифовального диска очень легко пережечь. К тому же ограничиться раскроем и зачисткой удается не всегда. И тут на помощь приходят старые добрые ручные инструменты.
Рубка металлаОперация по разделению на части или по удалению излишних слоев металла называется рубкой. При помощи рубки удаляют наплывы, снимают кромки, заусенцы, твердую корку, делят заготовки на части, делают отверстия, пазы, канавки, углубления, разделывают трещины под сварку и т. п. Точность обработки при рубке составляет 0,5–0,7 мм.
Линии разметки под рубку лучше наносить керном в виде пунктира. При разметке кромок под сварку удобно наносить две риски в виде параллельных линий: внутренняя показывает верхнее ребро фаски, а внешняя – нижнее ребро фаски.
Режущим инструментом при ручной рубке являются зубило и крейцмейсель[13]13
Крейцмейселем называют зубило, имеющее зауженную режущую кромку. Этот инструмент предназначен для прорубки шпоночных пазов, узких канавок и углублений.
[Закрыть], ударным – слесарный молоток. Угол заострения лезвия зубила или крейцмейселя в зависимости от твердости обрабатываемого материала должен составлять: для чугуна, бронзы и твердой стали – 70°, стали средней твердости – 60°, меди, латуни, алюминиевых и драгоценных сплавов – 45° и менее.
Слесарные молотки бывают с круглым и квадратным бойком. Сила удара молотка по зубилу зависит от веса молотка, величины размаха и скорости движения руки. Тяжелый молоток увеличивает силу удара, но в то же время делает работу более утомительной. Рекомендуемая масса молотка – от 600 до 800 г.
При рубке заготовки кладут на толстую стальную плиту или наковальню или зажимают в тиски. Для рубки лучше применять стуловые тиски, они более устойчивы. При использовании параллельных тисков необходимо, чтобы они были тяжелыми и прочными, с шириной губок 125–150 мм. Рубить следует по направлению к неподвижной губке, предварительно подложив под деталь деревянную или металлическую подкладку, чтобы не испортить тиски.
Зубило следует держать легко в кулаке левой руки за среднюю часть стержня, удерживая главным образом безымянным пальцем и мизинцем и слегка придерживая средним и указательным пальцами. Стоять надо прямо, не нагибаясь, вполоборота по отношению к тискам так, чтобы левая нога была выдвинута вперед, а правая отнесена назад[14]14
Описания методик работы здесь и далее ориентированы на правшей. Для левшей позиции правых и левых конечностей соответственно меняются местами.
[Закрыть]. Во время рубки надо смотреть на лезвие зубила, а не на головку, иначе при ударе легко промахнуться.
Рубку пруткового, полосового и толстого листового металла производят на плите или наковальне. Зубило ставят вертикально, материал надрубают с обеих сторон и затем отламывают, перегибая то в ту, то в другую сторону. Круглые прутки предварительно надрубают по окружности, а затем, поворачивая пруток, наносят сильные удары до полного разделения.
При вырубании заготовки из листового металла или получении в нем отверстия лист кладут на плиту, зубило держат вертикально и ведут его вдоль разметочной линии, оставляя припуск на последующую обработку (рис. 11, а). Сначала легкими ударами делают надрубы вдоль всей линии разметки, а затем сильными ударами прорубают материал насквозь. Лист толщиной до 2 мм прорубают с одного удара, предварительно подложив прокладку из мягкой стали, чтобы не повредить зубило. Толстые листы рубят до тех пор, пока с противоположной стороны не появится след от зубила, и, перевернув лист, окончательно вырубают заготовку.

Рис. 11. Рубка:
а — на наковальне; б — в тисках
При рубке в тисках листовой материал устанавливают так, чтобы разметочная линия совпала с уровнем губок. Толстые заготовки при рубке по разметке устанавливают так, чтобы риски были выше губок на 3–4 мм.
В ряде случаев, например при изготовлении художественно-декоративных элементов (для заборов, лестничных ограждений и т. п.), металл не разрубают полностью, а надрубают, формируя таким образом заусенцы, завитки, вилки и т. п. Если необходимо от стержня квадратного сечения или полосы отсечь ветвь значительно меньшей толщины, чем остающаяся часть стержня, это делают, как правило, вертикально в тисках (рис. 11, б). Заготовку зажимают в тисках и зубилом под соответствующим углом отсекают нужную ветвь. В этом случае заготовку как бы обтесывают. Эта операция требует значительного опыта для того, чтобы рассекание было ровным, а отсекаемые ветви были одной и той же толщины. Чтобы облегчить рубку, заготовку следует нагреть.
При черновой рубке срубают стружку от 1,5 до 2 мм. При чистовой рубке снимают слой металла толщиной 0,5–1 мм. Угол наклона зубила должен быть 35–40°. При меньших углах зубило легко соскальзывает, при бóльших – врезается.
В процессе рубки холодного металла в нем возникает структурное напряжение, в результате чего в заготовке могут появиться трещины. Чтобы избежать этого, заготовку можно предварительно отжечь.
Для получения при рубке равных фасок требуется внимательность в работе и равномерный нажим на инструмент. При рубке фаски на кромках листов следует убедиться в надежности закрепления края листа для предупреждения сдвига их при ударах.
При чистовой рубке стали и меди полезно обтирать лезвие зубила тряпкой, смоченной в машинном масле или мыльной воде, при рубке алюминия – скипидаром. Чугун следует рубить сухим зубилом.
Пользоваться надо только острозаточенным зубилом. При заточке зубил и крейцмейселей на наждачных станках не следует сильно прижимать их к абразивному кругу, что может привести к перегреву и отпуску режущей кромки. Грани лезвия должны иметь одинаковую ширину и угол наклона к осевой линии.
РазрезаниеРазделение заготовки на части, удаление излишков металла, вырезание отверстий называется разрезанием. Тонкий листовой металл разрезают ножницами, профильный материал, трубы и толстые листы – ножовкой. Допустимая толщина листового металла, разрезаемого ручными ножницами, различается: для стали это 0,7 мм, для меди – 1,0 мм, для алюминия – 2,5 мм.
Более толстый листовой, а также полосовой и прутковый металл разрезают рычажными или машинными ножницами. Различают прямые правые и прямые левые ножницы. У правых ножниц верхнее лезвие (по отношению к нижнему) находится справа, у левых – слева. В большинстве случаев применяют правые ножницы, так как линии разметки при работе ими хорошо видны; левыми ножницами пользуются при вырезании криволинейных деталей, при этом резать нужно по часовой стрелке, располагая ножницы так, чтобы они не закрывали лезвием линии разметки. Если ту же операцию проводят правыми ножницами, то процедуру выполняют против часовой стрелки (рис. 12). Применяют также ножницы с кривыми лезвиями специально для разрезания по кривым линиям.
Круглое отверстие можно вырезать следующим образом. После разметки лист кладут на деревянную подкладку и зубилом прорубают его крестообразно в центре. Потом лист переворачивают, края проруба отгибают и обрезают. Вставив лезвие ножниц в получившееся отверстие, режут, отгибая лишний металл вниз, по спирали до линии разметки, а затем короткими шагами вырезают круг. Если нужно получить диск, после разметки сначала обрезают углы листа. Когда отгибаемая (лишняя) часть станет слишком длинной и начнет мешать, ее отрезают.

Рис. 12. Работа ножницами по металлу:
а – прямолинейное разрезание; б, в – криволинейный рез
Разрезание листового металла производят по заранее нанесенной разметке, а ножницы располагают так, чтобы верхнее лезвие всегда находилось над разметочной линией. При разрезании листа отрезаемую часть отгибают левой рукой вверх, что облегчает процесс и предохраняет правую руку от пореза.
При разрезании листа на узкие полосы его нужно положить на стол и следить за тем, чтобы нижнее лезвие опиралось на стол, а отрезаемые полосы отгибались вперед.
Ножницы раскрывают несильно – примерно на 2/3 длины лезвия, тогда они хорошо захватывают и режут металл; сильно раскрытые ножницы выталкивают металл. Лезвия ножниц должны быть перпендикулярны плоскости листа, при перекосе они мнут металл, образуются заусенцы, а ножницы заедает. Ножницы нужно все время плотно прижимать к краю прореза, иначе неизбежно появятся заусенцы.
Стуловые (или кровельные) ножницы применяют для разрезания более толстых листов (до 2–3 мм). Они отличаются тем, что верхняя рукоятка удлинена до 400–800 мм, а нижняя изогнута и крепится к верстаку. На этих ножницах работают всей рукой, а не кистью, как в ручных, что значительно увеличивает силу разрезания.
У рычажных ножниц нижнее лезвие неподвижное, закреплено на столе, а верхнее сочленено с ним посредством шарнира. Ножницы снабжены прижимным устройством, которое гасит опрокидывающий момент, возникающий в процессе резания. Они позволяют разрезать стальные листы толщиной до 2 мм.
Существует также целый ряд машинных или механических ножниц: дисковые, вибрационные и др.
Профильный металл и трубы разрезают ручными или механическими ножовками. Полотно в ручной ножовке устанавливают зубьями вперед. Степень натяжения полотна не должна быть слабой, иначе разрез получится косым, а полотно легко сломается. При чрезмерном натяжении полотно также легко ломается при малейшем перекосе. Натяжение полотна проверяют поворотом его на 1/8 часть окружности, взяв двумя пальцами посередине его длины.
При работе ножовку держат за ручку правой рукой, а левой поддерживают передний ее конец в горизонтальном положении. Левой рукой, которая находится впереди, производят нажим, а правая рука только поступательно перемещает ножовку. Во время движения назад (к себе) нажим не производится, так как при холостом ходу он ведет к быстрому затуплению зубьев. Завершая разрезание, усилие уменьшают.
При разрезании толстых заготовок полотно смазывают машинным маслом. Если распил получается косой (идет не по риске), не следует пытаться исправить направление поворотом ножовки – полотно сломается. Нужно начать новый разрез с противоположной стороны, повернув заготовку. Если полотно сломалось, нужно иметь в виду, что старое, изношенное полотно дает более узкий пропил. Поэтому новым полотном надо пройти сделанный разрез без нажима и по возможности начать резать с другой стороны.
При разрезании массивных заготовок длина пропила большая и резать трудно, поэтому, чтобы облегчить работу, ножовку наклоняют последовательно то к себе, то от себя. В этом случае резание идет не по всей ширине и процесс резания облегчается.
Граненые изделия начинают резать с грани, а не с угла. Полосовой металл разрезают по узкой грани – это производительней. Очень тонкий материал режут по широкой грани, так как при врезании зубья цепляются и полотно может легко сломаться. Обычно для облегчения врезания делают небольшой пропил трехгранным напильником или направляют полотно сбоку большим пальцем левой руки. Полезно сделать по линии разметки небольшую борозду зубилом или краем напильника. Это углубление поможет выдержать правильнее направление распила.
Очень тонкий материал зажимают между деревянными брусками толщиной 15–30 мм и режут вместе с брусками.
Для отрезания полосы от листа полотно поворачивают относительно станка на 90° и режут осторожно, так как от собственного веса ножовки полотно легко ломается.
Новое ножовочное полотно сначала хорошо использовать для разрезания мягких металлов (меди, латуни, алюминия и др.), а когда оно немного притупится – для стали и чугуна.
При вырезании отверстий в листовом металле сначала сверлят отверстие, в которое можно ввести полотно, затем собирают ножовку и приступают к резанию.
При разрезании труб ножовку сначала держат горизонтально; когда стенка трубы окажется пропиленной, ее наклоняют на себя. Затем трубу поворачивают на 45–90° от себя и продолжают резать.
Разрезаемое изделие следует надежно зажимать в тисках, иначе в процессе разрезания оно может сместиться и хрупкое полотно сломается.
ОпиливаниеОперацию по обработке металла напильником называют опиливанием. При этом с детали снимают слой металла, чтобы придать ей необходимую форму, размеры и обеспечить чистоту поверхности.
Обязательное условие успешной работы напильником – прочное закрепление опиливаемого предмета. Лучше всего заготовки зажимать в тиски. Обрабатываемая поверхность не должна слишком выступать над поверхностью губок. Изделия с тонкими стенками или выступами зажимают в тисках, пользуясь медными, свинцовыми или деревянными прокладками.
Работать напильником удобнее стоя. Опиливаемый предмет должен находиться на уровне локтя опущенной руки. Напильник держат правой рукой так, чтобы его ручка упиралась в мякоть ладони, большой палец располагался сверху вдоль ручки, а остальные пальцы прихватывали ручку снизу. При выполнении большинства опиловочных работ, особенно грубых, инструмент прижимают к обрабатываемой детали левой рукой, положенной на конец напильника. При чистовой обработке поверхностей напильником малого размера на него не нужно сильно нажимать, поэтому его передний конец удерживают щепотью – большим пальцем сверху, а средним и указательным – снизу. Мелкими напильниками и надфилями работают, как правило, одной рукой.
Нажимать на напильник нужно только при его движении вперед, так как зубья насечки режут именно в этом направлении. При обратном движении нажимать на напильник не надо, но и отрывать его от поверхности ни в коем случае не следует, так как при этом теряется правильное направление инструмента.
В насечке напильника не будут застревать частицы обрабатываемого металла, если напильник предварительно натереть мелом или древесным углем.
Неумелый работник обычно давит на напильник левой рукой сильнее, чем надо, отчего инструмент совершает качающие движения. Это приводит к скруглению обрабатываемой поверхности.
Научиться правильно владеть напильником и уверенно опиливать плоские поверхности можно только в результате систематической тренировки. Есть, однако, некоторые правила, выполнение которых поможет любителю сократить срок учебы.
В начале движения вперед нажим производят левой рукой, а правая рука просто направляет напильник. По мере продвижения напильника вперед нажим левой рукой постепенно уменьшают, одновременно увеличивая нажим правой рукой, так что в конце движения основное давление сообщает правая рука.
Детали из твердых металлов лучше обрабатывать напильниками с перекрестной насечкой, из мягких металлов – с простой (одинарной) насечкой.
При работе всегда используйте полную длину напильника.
При опиливании углов деталь в тисках нужно зажимать так, чтобы обрабатываемая грань располагалась горизонтально.
При продольном опиливании криволинейных поверхностей напильнику придают качательное движение в вертикальной плоскости.
Короткие заготовки зажимают в тиски вертикально и обрабатывают колебательными движениями напильника в горизонтальной плоскости.
Вогнутые криволинейные поверхности, а также круглые и криволинейные отверстия в деталях опиливают полукруглыми или круглыми напильниками или надфилями. Напильник движется горизонтально и одновременно поворачивается вокруг своей оси, причем радиус кривизны напильника или надфиля должен быть всегда меньше радиуса кривизны поверхности.
Правообладателям!
Это произведение, предположительно, находится в статусе 'public domain'. Если это не так и размещение материала нарушает чьи-либо права, то сообщите нам об этом.