Текст книги "Теxнология дуговой сварки в защитных газах"
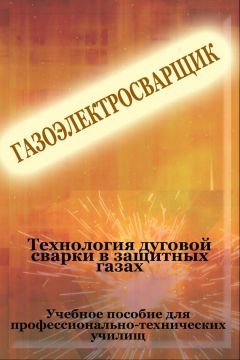
Автор книги: Илья Мельников
Жанр: Хобби и Ремесла, Дом и Семья
Возрастные ограничения: +12
сообщить о неприемлемом содержимом
Текущая страница: 1 (всего у книги 3 страниц)
Илья Мельников
Технология дуговой сварки в защитных газах
СУЩНОСТЬ ДУГОВОЙ СВАРКИ В ЗАЩИТНЫХ ГАЗАХ
При этом способе в зону дуги подается защитный газ, струя которого, обтекая электрическую дугу и сварочную ванну, предохраняет расплавленный металл от воздействия атмосферного воздуха, окисления и азотирования.
Сварку в защитных газах отличают следующие преимущества:
– высокая производительность (в 2-3 раза выше обычной дуговой сварки);
– возможность сварки в любых пространственных положениях, хорошая защита зоны сварки от кислорода и азота атмосферы, отсутствие необходимости очистки шва от шлаков и зачистки шва при многослойной сварке;
– малая зона термического влияния;
– относительно малые деформации изделий;
– возможность наблюдения за процессом формирования шва;
– доступность механизации и автоматизации.
Недостатками этого способа сварки являются необходимость принятия мер, предотвращающих сдувание струи защитного газа в процессе сварки, применение газовой аппаратуры, а в некоторых случаях и применение относительно дорогих защитных газов.
Разработаны следующие разновидности сварки в защитном газе: в инертных одноатомных газах (аргон, гелий), в нейтральных двухатомных газах (азот, водород), в углекислом газе. Наиболее широкое применение получили аргонодуговая сварка и сварка в углекислом газе. Инертный газ гелий применяется очень редко ввиду его большой стоимости. Сварка в двухатомных газах (водород и азот) имеет ограниченное применение, так как водород и азот в зоне дуги диссоциируются на атомы и активно взаимодействуют с большинством металлов.
Сварка в углекислом газе, благодаря его дешевизне, получила широкое применение при изготовлении и монтаже различных строительных конструкций из углеродистых и низколегированных сталей.
Углекислый газ, подаваемый в зону дуги, не является нейтральным, так как под действием высокой температуры он диссоциируется на оксид углерода и свободный кислород. При этом происходит частичное окисление расплавленного металла сварочной ванны и, как следствие, металл шва получается пористым с низкими механическими свойствами. Для уменьшения окислительного действия свободного кислорода применяют электродную проволоку с повышенным содержанием раскисляющих примесей (марганца, кремния). Шов получается беспористый, с хорошими механическими свойствами.
По способу защиты различают местную и общую защиту свариваемого узла (сварку в контролируемой атмосфере). Основным способом местной защиты является струйная, при которой защитная среда создается газовым потоком при центральной, боковой или комбинированной подаче газа. При центральной подаче газа дуга, горящая между электродом и основным металлом, со всех сторон окружена газом, подаваемым под небольшим избыточным давлением из сопла горелки, расположенного концентрично оси электрода. Это самый распространенный способ защиты. Иногда с целью экономии инертных газов, а также получения оптимальных технологических и метуллургических свойств защитной среды применяют горелки, конструкция которых обеспечивает комбинированную защиту двумя концентрическими потоками газов. Например, внутренний поток образется аргоном, а внешний – углекислым газом. При сварке высокоактивных металлов надо защищать не только расплавленный металл, но и зону металла, нагреваемую при всаврке до температуры более 300 °С с лицевой и обратной стороны шва. Для расширения струйной защиты с лицевой стороны шва применяют дополнительные колпаки-приставки, надеваемые на сопло горелки. Защита обратной стороны шва обеспечивается поддувом защитного газа. Боковую подачу газа применяют ограниченно.
Наиболее эффективная защита металла шва и зоны термического влияния обеспечивается при сварке в камерах с контролируемой атмосферой. Камеры предварительно продувают или вакуумируют, а потом заполняют защитным (инертным) газом под небольшим давлением.
Сварку в защитных газах можно осуществлять вручную, полуавтоматически и автоматически. Ручная сварка применяется при соединении кромок изделий толщиной до 25-30 мм и при выполнении коротких и криволинейных швов. Полуавтоматическая и автоматическая сварки применяются при массовом и крупносерийном производствах.
Сварка в защитных газах производится как неплавящимся, так и плавящимся электродом. Неплавящиеся электроды служат только для возбуждения и поддержания горения дуги. Для заполнения разделки кромок в зону дуги вводят присадочный металл в виде прутков или проволоки. Применяются такие неплавящиеся электроды: вольфрамовые, угольные и графитовые. Вольфрамовые электроды изготовляют из проволоки марки ВТ-15 диаметром 0,8-6 мм, содержащей 1,5-2,0 % диоксида тория. Торий способствует более легкому возбуждению и устойчивому горению дуги. Однако торий является радиоактивным веществом и его применение сопряжено с соблюдением специальных санитарных правил. Для сварки алюминия и его сплавов успешно применяют электроды из проволоки марки ВЛ-10 (вольфрам с присадкой лантана). Лантан снижает расход вольфрама и повышает устойчивость горения дуги. Расход вольфрама при сварке незначителен и составляет при сварочном токе 300-400 А около 0,05-0,06 г на метр сварного шва. Угольные и графитовые электроды применяют редко, так как они не обеспечивают достаточно устойчивое горение дуги и сварной шов получается пористым с темным налетом. Плавящиеся электроды применяют в виде соответствующей сварочной или порошковой проволок.
ЗАЩИТНЫЕ ГАЗЫ
Аргон – одноатомный инертный газ без цвета и запаха, тяжелее воздуха. Получают аргон из воздуха. Аргон поставляется двух сортов: высшего и первого. Высший сорт содержит 99,992 % аргона, не более 0,006 % азота и не более 0,0007 % кислорода. Первый сорт содержит аргона 99,987%, азота – до 0,01% и кислорода – не более 0,002 %. Аргон поставляется в газообразном виде в баллонах типа А под давлением 15 MПa. Баллоны окрашены в серый цвет с зеленой полосой и зеленой надписью «Аргон чистый».
Аргон применяют при сварке ответственных сварных швов и при сварке высоколегированных сталей, титана, алюминия, магния и их сплавов.
Гелий – одноатомный инертный газ без цвета и запаха. Газообразный гелий производится также двух сортов: гелий высокой чистоты (99,985 % гелия) и гелий технический (99,8 %). Транспортируется и поставляется в баллонах типа А при максимальном давлении 15 МПа. Баллоны окрашены в коричневый цвет белой надписью "Гелий". Гелий используют так же, как аргон, но значительно реже ввиду высокой стоимости.
Углекислый газ СО2 не имеет цвета и запаха. Получают его из газообразных продуктов сгорания антрацита или кокса, при обжиге известняка и т. д. Поставляется в сжиженном состоянии в баллонах типа А вместимостью 40 л, в который при максимальном давлении 7,5 МПа вмещается 25 кг углекислоты (при испарении образуется около 12750л газа). Для сварки используют сварочную углекислоту. Чистота углекислоты первого сорта должна быть не менее 99,5 %, а высшего сорта 99,8 %. Баллоны с углекислотой окрашивают в черный цвет с желтой надписью "СО2 сварочный". Применяется при сварке низкоуглеродистых и некоторых конструкционных и специальных сталей.
Для снижения влажности углекислого газа рекомендуется установить баллон вентилем вниз и после отстаивания в течение 15 мин осторожно открыть вентиль и выпустить из баллона влагу. Перед сваркой необходимо из нормально установленного баллона выпустить небольшое количество газа, чтобы удалить попавший в баллон воздух. Часть влаги задерживается в углекислоте в виде водяных паров, ухудшая при сварке качество шва. Кроме того, при выходе из баллона, от резкого расширения происходит снижение температуры углекислоты и влага, отлагаясь в редукторе, забивает каналы и даже полностью закрывает выход газа. Для предупреждения замерзания влаги между баллоном и редуктором устанавливают электрический подогреватель.
Окончательное удаление влаги после редуктора производится специальным осушителем, наполненным прокаленным медным купоросом, хромистым кальцием или другим осушительным веществом.
СВАРОЧНЫЕ ПОЛУАВТОМАТЫ И АВТОМАТЫ
Аргонодуговая сварка неплавящимся или плавящимся электродом производится на постоянном и переменном токе. Установка для ручной сварки постоянным током состоит из сварочного генератора постоянного тока или сварочного выпрямителя, балластного реостата, газоэлектрической горелки, баллона с газом, редуктора и контрольных приборов (амперметра, вольтметра и расходомера газа).
Источником питания дуги служат сварочные генераторы постоянного тока с жесткой или пологопадающей внешней характеристикой. Для регулирования и получения малых значений сварочного тока и повышения устойчивости горения дуги в сварочную цепь включают балластные реостаты.
Газоэлектрические горелки бывают различной конструкции. Наибольшее применение получила горелка типа ЭЗР. Выпускаются горелки типов ЭЗР-66 для сварки током до 150 А, ЭЗР-4-68 – до 500 А и ЭЗР-5-71 – до 80 А.
Электрододержатель типа ЭЗР-3-66 состоит из корпуса, сменного наконечника, рукоятки с устройством включения подачи газа и газотокоподводящего кабеля. Диаметр сопла сменных наконечников 8 и 10 мм. Они позволяют использовать электроды диаметром 1,5, 2 и 3 мм, рассчитанные на сварочные токи до 150 А. Расход аргона составляет 120-360 л/ч. Масса горелки с газотокопроводящим кабелем около 3 кг.
Для сварки при больших сварочных токах (до 450 А) применяют также горелки типов АР-10-3 (большая), АР-75, АР-9, снабженные системой водяного охлаждения.
Установка для ручной сварки переменным током состоит из источникам питания дуги, осциллятора, балластного реостата, газоэлектрической горелки, баллона с газом, редуктора и контрольных приборов.
Источники питания должны иметь повышенное вторичное напряжение, чтобы обеспечить устойчивое горение дуги. Для этого в сварочную цепь включают два сварочных трансформатора с последовательно включенными вторичными обмотками или применяют трансформатор типа ТСДА с повышенным вторичным напряжением холостого хода. Осциллятор обеспечивает быстрое и легкое возбуждение и устойчивое горение дуги. Применяют газоэлектрические горелки типов ГРАД-200 и ГРАД-400, отличающиеся легкостью. Горелка ГРАД-200 массой 0,2 кг допускает сварочные токи до 200 А, а горелка ГРАД-400 массой 0,4 кг – до 400 А. Применяются установки УДАР-300 и УДАР-500 (номинальный сварочный ток 300 и 500 А). Взамен этих установок выпускаются установки типов УДГ-301 и УДГ-501. Установки типов УДГ-301 и УДГ-501 применяют для сварки сплавов легких металлов в аргоне. Такие установки имеют однофазный силовой трансформатор с неподвижным подмагничиваемым шунтом. Сердечник шунта с обмоткой, питаемой постоянным током, расположен перпендикулярно стержням трансформатора, на которых находятся секции первичной и вторичной обмоток. Два диапазона регулирования сварочного тока получают при параллельном соединении секций обмоток – большие токи и при их последовательном соединении – малые токи. В пределах каждого диапазона плавное регулирование тока осуществляют подмагничиванием шунта, изменяя ток, питающий его обмотку.
Полуавтоматическая сварка неплавящимся электродом производится шланговым полуавтоматом типа ПШВ-1, состоящим из сопла; вольфрамового электрода; корпуса; сварочной проволоки; рукоятки; механизма подачи сварочной проволоки. ПШВ-1 предназначен для сварки металлов толщиной 0,5-5 мм. Полуавтомат снабжен электродвигателем, который через редуктор и гибкий вал, проходящий по шлангу, приводит во вращение ролики, расположенные на газоэлектрической горелке. Ролики протягивают по шлангу присадочную проволоку и подают ее в зону дуги. Скорость подачи проволоки диаметром 1-2 мм устанавливается в пределах 5-50 м/ч. Сварку осуществляют постоянным или переменным током с включением в сварочную цепь осциллятора. Полуавтомат позволяет выполнять сварку во всех пространственных положениях шва.
Полуавтоматическая сварка плавящимся электродом производится с помощью полуавтоматов типов ПШПА-6, ПШПА-7 и ПШП-9. Первые два типа предназначены для сварки электродной проволокой диаметром 1,6-2,5 мм при сварочном токе до 300 А, а последний тип – для сварки малых толщин проволокой диаметром 0,5-1,2 мм при сварочных токах до 180 А. Комплект полуавтомата состоит из переносного пульта управления, механизма подачи электродной проволоки с кассетой и газоэлектрической горелки в виде пистолета. Электродная проволока вытягивается из кассеты по шлангу роликами, расположенными в пистолете. Ролики вращаются электродвигателем через редуктор с помощью гибкого привода. Пистолет полуавтомата типа ПШПА-7 предназначен для сварки многослойных швов деталей из алюминия, магния и их сплавов с толщиной кромки до 100-150 мм. Для предохранения от нагрева пистолет имеет водяное охлаждение. Пистолет состоит: из сопла, механизма подачи проволоки, шланга для подачи проволоки, шланга для подвода аргона, проводов управления, рукоятки.
Для сварки в монтажных условиях рекомендуется ранцевый полуавтомат типа ПДГ-304, имеющий ремни для крепления на спине сварщика. Источником питания служат выпрямитель типа ВДГ-301. Сварочный ток – 315 А, диаметр сварочной проволоки 0,8-2,0 мм, скорость подачи проволоки 0,05-0,2 м/с. Масса механизма полуавтомата ПДГ-304 7 кг.
Автоматическая сварка может производиться неплавящимся и плавящимся электродами.
Автомат типа УДПГ-300 служит для сварки в защитном газе. В его комплект входят: сварочная головка, механизм подачи проволоки, электродная проволока, кассета с электродной проволокой, кнопка управления, электродвигатель механизма подачи.
Применяются специализированные сварочные тракторы типа АДСП-2 для сварки черных и цветных металлов толщиной 0,8 мм и более. Автоматы типа АТВ предназначены для сварки труб различного диаметра неплавящимся вольфрамовым электродом и присадочной проволокой диаметром 1,6-2,0 мм.
Сварка в углекислом газе производится полуавтоматическими и автоматическими аппаратами. Полуавтоматическая установка состоит из сварочного преобразователя постоянного тока, газоэлектрической горелки, механизма подачи электродной проволоки, аппаратного шкафа, баллона с углекислым газом, осушителя, подогревателя, редуктора и расходомера. Применяют сварочные преобразователи типов ПСГ-350 или ПСГ-500-2.
Газоэлектрические горелки служат для подвода газа и подачи электродной проволоки в зону дуги и для подвода сварочного тока к электродной проволоке. Они выпускаются различных типов для малых сварочных токов (до 300 А) и для сварки на больших токах (до 1000 А). Последние снабжены водяным охлаждением. Механизм подачи электродной проволоки используется от полуавтоматов типов ПШПА-6, ПШПА-7. Подача электродной проволоки производится с постоянной скоростью независимо от напряжения дуги. Аппаратный шкаф содержит электрооборудование, необходимое для подвода сварочного тока и тока цепей управления к соответствующей аппаратуре установки. Осушитель газа типа РОК-1, начиненный обезвоженным медным купоросом, применяют для удаления влаги из углекислого газа. Подогреватель с электронагревательным элементом служит для подогрева углекислоты. Это необходимо для предупреждения замерзания редуктора, которое может произойти от понижения температуры газа при редуцировании.
Широкое применение получил полуавтомат типа А-547ум (ПДГ-309), предназначенный для сварки листового материала толщиной до 3 мм во всех пространственных положениях электродной проволокой диаметром 0,8-1,2 мм с постоянным током обратной полярности. Источниками питания дуги являются выпрямители типа ВС-ЗООБ или ВДГ-301. Сварочный ток устанавливается в пределах 60-300 А. Механизм подачи электродной проволоки вмонтирован в чемоданчик и состоит из электродвигателя постоянного тока, роликов и катушки с проволокой. Реостат, включенный в обмотку двигателя, позволяет плавно изменять скорость вращения электродвигателя и тем самым изменять скорость подачи электродной проволоки в пределах 100-340 м/ч. Электродная проволока применяется марок Св-12ГС, Св-08ГС и Св-08Г2С.
Для автоматической сварки применяют специальные сварочные аппараты типов АДПГ-500, АСУ-6 или сварочные тракторы типов АДС-1000-2, ТС-17М, переоборудованные для сварки в углекислом газе.
АРГОНОДУГОВАЯ СВАРКА
При аргонодуговой сварке постоянным током неплавящимся электродом используют прямую полярность. Дуга горит устойчиво, обеспечивая хорошее формирование шва. При обратной полярности устойчивость процесса снижаемся, вольфрамовый электрод перегревается, что приводит к необходимости значительно уменьшить сварочный ток. Вследствие этого производительность процесса снижается. При автоматической и полуавтоматической сварках плавящимся электродом применяется постоянный ток обратной полярности, при котором обеспечивается высокая производительность процесса. Кроме того, при сварке алюминия, магния и их сплавов происходит мощная бомбардировка поверхности сварочной ванны положительными ионами, что наряду с процессом катодного распыления приводит к разрушению пленки оксидов алюминия и магния, облегчая процесс качественной сварки без применения флюсов.
При сварке переменным током неплавящимся электродом необходимо, чтобы источник тока имел более высокое напряжение холостого хода, что обеспечивает устойчивое горение дуги и стабилизирует процесс сварки. Однако в связи с ограничением напряжения по условиям безопасности применяют ток допускаемого напряжения, на который накладывается ток высокой частоты, включая в сварочную цепь осциллятор.
При сварке переменным током происходит частичное выпрямление тока вследствие различной электронной эмиссии вольфрамового электрода и свариваемого изделия. В периоды, когда вольфрамовый электрод является катодом, электронная эмиссия имеет большую интенсивность, проводимость дугового промежутка повышается, а напряжение на дуге понижается. Вследствие этого сварочный ток увеличивается. В периоды, когда катодом является изделие, электронная эмиссия менее интенсивна, в результате чего сварочный ток уменьшается. Ввиду этого появляется некоторая составляющая постоянного тока, что приводит к уменьшению тепловой мощности дуги и значительно затрудняет разрушение оксидной пленки при сварке алюминиевых и магниевых сплавов и тем самым способствует образованию поверхностных и внутренних дефектов. Поэтому при сварке переменным током принимают меры по устранению или снижению составляющей постоянного тока. Для этой цели в сварочную цепь включают последовательно конденсаторную батарею 100 мкФ на 1 А сварочного тока или аккумуляторную батарею (положительный полюс батареи присоединяют к электроду). Применяется также последовательное включение в сварочную цепь активного сопротивления, но такая мера снижает устойчивость горения дуги и поэтому при такой схеме сварочной цепи приходится использовать источники питания дуги с повышенным напряжением холостого хода до 120 В.
При ручной сварке неплавящимся электродом возбуждение дуги производят на угольной или графитовой пластинке и некоторое время разогревают электрод, а затем быстро переносят дугу в начало разделки кромок. При сварке переменным током возбуждение дуги осуществляют с помощью осциллятора без короткого замыкания электрода на изделие.
При полуавтоматической и автоматической сварке возбуждение дуги производят путем касания электродной проволокой вводной планки, которую устанавливают для предупреждения дефекта в начале свариваемого шва.
Аргонодуговой сваркой можно выполнять швы стыковых, тавровых и угловых соединений. При толщине листов до 2,5 мм рекомендуется сварку производить с отбортовкой кромок. При малом зазоре порядка 0,1-0,5 мм можно сваривать тонколистовой материал толщиной 0,4-4 мм без отбортовки и разделки кромок. При этом чем меньше толщина свариваемых встык листов, тем меньше допустимый зазор. Листы толщиной 4-12 мм сваривают с V-образной разделкой кромок при угле разделки 50-70°. Допустимый зазор в стыке составляет не более 1,0 мм. Расход аргона должен обеспечить надежную защиту электрода и металла сварочной ванны от воздействия воздуха. Следует учитывать конфигурацию свариваемого изделия, чтобы при экономном расходовании газа создать хорошую защиту шва.
Рекомендуются следующие соотношения:

Перед началом сварки следует продуть шланг и горелку небольшой порцией аргона. Возбуждение дуги следует производить спустя 3-4 с после подачи аргона в горелку. Струя аргона должна защищать не только сварочную ванну, но и обратную сторону шва. Если доступ к обратной стороне шва затруднен, то применяют подкладки или флюсовую подушку.
Ручную сварку листов малой толщины производят левым способом, при котором горелка перемещается по шву справа налево. Листы большой толщины (более 12 мм) сваривают правым способом, т. е. горелку ведут слева направо. Ось мундштука горелки при сварке тонких листов (толщиной до 4 мм) должна составлять с поверхностью свариваемых листов 75-80°. Присадочный пруток вводится в зону дуги под углом 10-15° к поверхности свариваемых листов, т. е. почти перпендикулярно оси мундштука горелки. При сварке листов большей толщины ось мундштука горелки располагают почти перпендикулярно к поверхности свариваемых листов. Длина дуги при аргонодуговой сварке небольшая и составляет 1,5-2,5 мм при длине выступающего вольфрамового электрода в пределах 6-12 мм. Дугу следует гасить постепенно, увеличивая дуговой промежуток. Подачу аргона в зону дуги следует прекратить лишь спустя 10-15 с после гашения дуги, чтобы защитить металл шва от воздействия воздуха до его затвердевания.
Автоматическая и полуавтоматическая сварка плавящимся электродом производится при постоянной скорости подачи электродной проволоки независимо от напряжения дуги. Постоянство длины дуги поддерживается автоматическим саморегулированием. Применяется электродная проволока диаметром 0,5-2,0 мм. Листы толщиной до 5 мм соединяют стыковой сваркой без разделки кромок, а при толщине листов более 5 мм произнодят У-образную разделку шва с углом разделки 30-50°.
Сварочный ток влияет на характер переноса металла в шов. С увеличением тока капельный перенос металла электрода сменяется струйным и глубина проплавления увеличивается. Значение тока, при котором металл электрода начинает стекать в сварочную ванну в виде тонкой струи, называют критическим. Практика показала, что при сварке алюминиевых сплавов критический ток составляет 70 А на 1 мм2 сечения электродной проволоки, при сварке сталей – 60-120 А на 1 мм2 сечения проволоки.
Подготовка поверхностей под сварку включает обезжиривание растворителями, бензином авиационным или ацетоном техническим, а затем удаление оксидной пленки механической зачисткой или химическим способом. Механическую зачистку производят металлическими щетками из проволок диаметром до 5 мм. Химический способ включает травление в течение 0,5-1,0 мин раствором, состоящим из 45-55 г едкого натра технического и 40-50 г фтористого натрия технического на 1 л воды, промывку проточной водой, нейтрализацию в 25-30 %-ном водном растворе азотной кислоты в течение 1-2 мин, промывку в проточной воде, затем в горячей воде, сушку до полного испарения влаги. Обработку рекомендуется выполнять не более чем за 2-4 ч до сварки.
Правообладателям!
Это произведение, предположительно, находится в статусе 'public domain'. Если это не так и размещение материала нарушает чьи-либо права, то сообщите нам об этом.