Текст книги "Технология декоративно-прикладного искусства. Основы дизайна. Художественное литье. Учебное пособие"
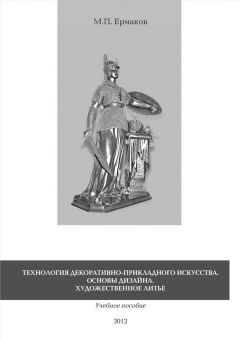
Автор книги: Михаил Ермаков
Жанр: Прочая образовательная литература, Наука и Образование
сообщить о неприемлемом содержимом
Текущая страница: 17 (всего у книги 66 страниц) [доступный отрывок для чтения: 21 страниц]
На начальном этапе для художественного литья предлагаем использовать один из самых доступных и легкоплавких металлов – цинк.
Чистый цинк имеет серовато-белый цвет с синеватым оттенком. На свежем изломе он имеет характерный блеск, быстро исчезающий на воздухе: цинк покрывается слоем окиси тускло-серого цвета. Оксидная пленка очень прочная и надежно защищает металл от дальнейшей коррозии. Цинк куется плохо, легко паяется и обрабатывается инструментами, а также гравируется, и при соответствующей обработке ему можно придать различный вид.
Цинк обладает высокими литейными свойствами, низкой температурой плавления (419 °C), что позволяет заниматься литьем без особых нагревательных приспособлений. Но самое главное – не надо прилагать особых усилий к его поиску. Проще всего сделать запас цинковых стаканчиков от гальванических элементов (батареек), отслужившие свой срок они в больших количествах выбрасываются в контейнеры для мусора. От остатков смолы полые цинковые стаканчики очищают кипячением в 10-процентном растворе питьевой соды. А затем собранный цинковый материал сплавляют в слиток. Таким образом, на первое время материалом вы себя обеспечите.
Сплавы цинка были также известны человеку с глубокой древности. Они изготовлялись египтянами, китайцами и индусами еще до нашей эры и ввозились в Европу. Уже в древности цинк добавляли как руду в медь при получении латуни. В доисторических дакийских развалинах в Трансильвании был найден идол, отлитый из сплава, содержащего около 87 % цинка.
Античные мастера также получали и использовали цинковые сплавы с медью (латунь), где содержание первого не превышало 28 %.
Получение металлического цинка из галмея (Zn4·H2O) впервые описывает Страбон (60–20 гг. до н. э.). Цинк в этот период называли тутией или фальшивым серебром. Благодаря довольно сложной выработке цинка из руд в X–XI вв. н. э. искусство получения цинка в Европе было утрачено, и он ввозился сюда под названием индийского олова из Китая и Индии.
В конце XIII в. н. э. итальянский путешественник Марко Поло описал способ получения металлического цинка в Персии. В 1637 году метод выплавки цинка и его свойства описываются в китайской книге «Циан коняг канн у». Казалось бы, что раз метод получения описан в литературе, то его легко могли перенять другие народы и применить у себя на родине. Но этого не случилось. Экономическая и культурная разобщенность народов, слабые транспортные связи, а главное, стремление многих ученых описывать свои открытия на непонятном языке – всё это препятствовало быстрому распространению технических достижений.
Вторично получение цинка в Европе стало известно в начале XVI века. О способе его выплавки упоминают в своих сочинениях Георг Агрикола (1494–1555 гг.) и Теофраст Парацельс. Однако и после этого цинк в Европе был большой редкостью, что продолжалось почти до конца XVIII века.
Название же «цинк» происходит от латинского слова, обозначающего бельмо или белый налет, и впервые встречается у Парацельса в 1530 году.
Однако получение цинка в чистом виде можно отнести лишь к XVI веку. Для производства художественных изделий сплавы, где цинк – основная составляющая, начали применяться только в XVIII веке. Роберт Бойль назвал цинк «спелтером». У нас цинк И. Шлаттер (1736 г.) называл «туцией», Ломоносов (1742 г.) ввел название «цинк», но оно не пользовалось успехом и цинк чаще всего называли «шпиаутер».
В 8-м издании «Основ химии» (1906 г.) Д. И. Менделеев употребляет современное название цинка, но наряду с этим ставит в скобках и другое его название – «шпиаутер». Из этого можно заключить, что во времена Менделеева старое название цинка было достаточно широко распространено.
«Ложная бронза», как ее называли в XIX веке, впервые явилась во всем своем великолепии на Лондонской всемирной выставке, где пальма первенства беспрекословно принадлежала французским фабрикантам. Их товаром были наводнены практически все павильоны выставки.
Хорошие литейные свойства и низкая температура плавления давно привлекли внимание мастеров миниатюрной пластики. Из цинка отливают миниатюрную настольную скульптуру, медальоны, броши, накладные бляшки, значки и многое другое. Для этих же целей применяют цинко-свинцовый сплав с содержанием свинца 25, 30 или 50 %.
В середине XIX века француз Жилло изготовил из цинка первое типографское клише. Цинковые сплавы оказались лучшим материалом для печати книг, рисунков и т. д.
В конце XIX века из цинка методом художественного литья изготовляли подсвечники, настольные бра, канделябры, декоративные скульптуры, которые нередко тонировали под бронзу или золотили. Изготовление скульптуры из цинка относится главным образом к 50-80-м годам. Примером такой скульптуры могут служить памятники Павлу I работы скульптора И. П. Витали, установленные в Гатчине. Из цинка в прошлом отливали и крупные вещи. Так, по проекту скульптора И. П. Витали для Георгиевского зала Большого Кремлевского дворца в Москве из цинка были отлиты колонны, украшенные декоративной скульптурой, а также скульптура на фасаде нового здания Государственного Эрмитажа [105].
Из цинка выполнены горельефы на часовне у Ильинских ворот в Москве, установленной в память гренадеров, павших под Плевной, работы архитектора и скульптора В. О. Шервуда (1887 г.). Памятник русским гренадерам в Москве, павшим в боях под Плевной, изготовленный из чугуна, насыщен барельефами, отлитыми из цинкового сплава. На первом барельефе изображен русский крестьянин, благословляющий сына-солдата на ратный подвиг, на втором – янычар, занесший кинжал над ребенком, которого он вырывает из рук матери, на третьем – гренадер, берущий в плен турецкого солдата. Эти барельефы являются в истории художественного литья одними из последних отливок, для которых использовался цинковый сплав в монументальной скульптуре.
В настоящее время скульптура и художественные изделия из чистого цинка очень редко изготовляются. Вместо цинка в современной художественной промышленности применяется алюминиевоцинковый сплав, изделия из которого (мелкая настольная скульптура и другие) получают способом кокильного литья «на выплеск».
В ювелирном деле цинк применяют для приготовления припоев, а также как один из компонентов в различных сплавах.
Во второй половине XIX века почти все российские бронзолитейные предприятия, так или иначе, изготовляли ряд товаров из цинковых сплавов, что являлось большим подспорьем в производстве и торговле. Дешевые вещи, заполнив прилавки обеих столиц, хлынули в губернские города, находя и там своих покупателей.
Настоящим «Клондайком» для нарастающего цинкового производства Европы явились месторождения галмеевых руд в Верхней Силезии, интенсивная разработка которых началась с первой половины XVIII века. С этого момента Силезия становится новым центром цинкового производства.
В 1805 году в Германии был разработан метод вальцовки (проката) цинка при температуре 115–165 °C. В Европе начинают использовать цинковый прокат для кровельно-жестяных работ. Вместе с тем делаются первые попытки использовать цинк и его сплавы для изготовления небольших предметов повседневного обихода. Как правило, это были медали, декоративные накладки, таблички и другие мелкие предметы. Уже в 1818 году из цинка изготавливаются подносы для кофейников, подсвечники, подставки для ламп и другие предметы, которые раньше делались из других сплавов.
При этом мастера конструктивно опирались на чугунное литье. Сплошной отливкой производились лишь тонкие профили. Как ранние примеры фигурного цинкового литья можно назвать два произведения искусства Жана-Филиппа Давида: цинковый бюст Е. К. Висконти (1820 г.) и Распятие, отлитое в 1819 году для собора Dom von Angers, а также статую Виктории для берлинской Новой Вахты.
Идея применить цинк при отливке больших архитектурных деталей и скульптур принадлежит Гайсу. С его подачи заводчик Рутберг, занимающийся в Силезии муфельными процессами, открыл новую широкую область применения этого материала. Предпосылкой для этого послужила специальная технология производства, обусловленная самим материалом. В отличие от бронзового и чугунного литья, выполнялись отдельные детали, которые затем присоединялись к полому корпусу резьбовыми соединениями или пайкой.
Благодаря расчленению отливок на плоские фрагменты, имеющие соразмерную толщину стенок, была решена проблема уменьшения объема при затвердевании сплава и предотвращению образование трещин. Производство же литейных форм значительно облегчалось, а небольшие фрагменты смонтировать с корпусом было не так уже сложно.
Вскоре после фирмы Гайса появился ряд фирм, которые стали его последователями: «Деваранн и Кале» (Берлин); «Фёрст-Гайс и Гланц» (Вена); «Кунст-Цинк-литейня», или «Королевская бронзовая литейня» (Мюнхен, вторая половина XIX века). Эти фирмы работали по многочисленным оригинальным рисункам и моделям, которые делались специально для реализации в цинковом литье и не имели иного воплощения.
В середине XIX века в Европе и России цинковое литье как производство художественных изделий начинает доминировать над бронзовым. Это обусловлено рядом факторов, говорящих в пользу первого. Цинк более дешевый материал по отношению к меди и бронзе, он более текуч, что позволяет исключать последующую обработку отливки, а разница в температуре плавления этих материалов позволяла производителям экономить как сырье и энергию, так и рабочие руки, участвующие в производственном процессе.
Среди российских фабрикантов-производителей изделий из цинковых сплавов необходимо отметить Штанге, Шопена и Крумбюгеля, Гризара и Кумберта. Первый из них получил в 1853 году на Московской мануфактурной выставке большую серебряную медаль за лампы, представленные его фабрикой.
Благодаря высокой жидкотекучести цинка, из него выполняли очень тонкие ажурные работы. Цинковое литье особенно широко применялось для производства недорогой осветительной арматуры: подсвечников, подставок для ламп, настенных бра, канделябров и т. п. Эти изделия тонировались под бронзу или золотились. Кроме того, литьем исполнялись и круглые декоративные скульптуры, которые отливались по частям и затем спаивались оловянно-свинцовым припоем.
Цинковые изделия относительно устойчивы к коррозии, однако при нарушении технологии в литье и производстве сплавов и покрытий, а также при наличии агрессивной среды (морской климат, городской смог) они утрачивают первоначальный вид, подвергаясь разрушениям.
Уже в 1817–1833 гг. в Королевской высшей горной службе в Берлине и на медном предприятии Хеегертюлера проводились опыты по проверке коррозионной устойчивости цинковых, медных и свинцовых пластинок. Еще на ранних этапах производителями было отмечено, что нанесение на цинковую окисленную поверхность масляных лаков и красок не дает большого эффекта. Через некоторое время покрытие начинает осыпаться. Были проведены опыты по улучшению адгезии (сцепляемости) поверхности отливок с защитными и декоративными покрытиями.
Среди покрытий, применяемых для отливок из цинковых сплавов, известны и полихромные (краски, лаки, иногда сернокислая медь CuSO4 для создания зелени, характерной для бронзы) и металлические (листовое серебро, золото, медь). Среди русских способов получения эффекта цинка зеленой античной бронзы применялся следующий состав: поверхность покрытой медью цинковой вещи смачивали раствором нашатыря (30 г) и щавелевокислого калия (8 г) в уксусе (1 л). Раствор наносили кистью до получения необходимого результата.
В настоящее время существует значительное количество способов химического окрашивания литой скульптуры из алюминиево-цинкового сплава и оцинкованного железа. Эти металлы обычно тонируют в черный или темно-серый цвет, различные рецепты можно найти в источнике [96].
Со второй половины XIX века начала применяться гальваника с использованием цианидов. С появлением электролитического способа покрытия себестоимость производства предметов из цинковых сплавов значительно снизилась.
К основным повреждениям памятников из цинка относят: а) изломы и деформации, возникающие в результате механических повреждений. Основной причиной хрупкости предметов из цинка является его крупнозернистое строение; б) трещины, образовавшиеся как результат нарушения производственных технологий, а также как результат межкристаллитной коррозии; в) коррозия паяных швов и арматуры, возникающая в результате образовавшейся гальванопары; г) коррозия поверхности изделия, как результат вредного воздействия окружающей среды; д) коррозия, как результат возникновения гальванопары между цинком и его покрытием; е) выветривание поверхности у памятников, находящихся под открытым небом; ж) нарушение декоративного покрытия.
Опыт реставрации предметов цинкового литья невелик. Поэтому мы приведем пример работы с парными канделябрами на подставках из черного мрамора. Выполненные, вероятно, в России в 1870-1880-х годов, они являются яркими представителями стиля «историзм» (рис. 3.34).

Рис. 3.34. Парные канделябры. 1870-1880-е годы. [105]
В качестве декоративного покрытия для отделки канделябров использовано гальваническое меднение с последующим нанесением в углублениях патины черного и зеленого цвета.
При реставрации канделябров были проведены лабораторные исследования с применением микрохимического метода (ГИМ, Р. А. Турищева). Растворение продуктов коррозии покрытия в 10 % растворе азотной кислоты показало присутствие аниона СО2-2, а появление коллоидной серы в растворе – присутствие сульфида меди. Реакция раствора с хлористым барием и раствором азотнокислого серебра свидетельствовала об отсутствии анионов SО4-2 и Cl-1.
По результатам проведенных исследований было сделано заключение, что продукты коррозии состоят в основном из карбонатов меди, а присутствие сульфида меди свидетельствует о сульфидной природе патины. Зеленые отложения на поверхности декоративной отделки являются искусственно нанесенными и опасности для экспоната не представляют.
Следующим этапом в реставрационном процессе стало исправление деформаций элементов. Опираясь на ранее проводимые работы в этой области и на опыт других исследователей, было решено использовать метод с применением нагрева с помощью термопистолета. Для контроля температуры использовалась термопара, которую подключали поочередно к исправляемым деталям.
Ввиду многообразия цинковых сплавов, используемых в художественной промышленности, температура, при которой допустимо проводить исправления деформаций, может быть различной. В данном случае она составляла приблизительно 120 °C.
Определенные трудности вызвала работа по восстановлению покрытия как в местах склеивания и дублировки, так и на деталях, где это покрытие отсутствовало. Видимо, в результате предыдущей чинки на двух деталях (свечник и розетка) отсутствовал слой патины. Для его восстановления детали были погружены в разогретый раствор серной печени. После чего их поверхность подверглась втиранию медного и графитового порошка. Зеленые отложения имитировались акриловыми красителями. Для тонировки клеевых швов использовались также акриловые краски. Экспонат был законсервирован отбеленным пчелиным воском, растворенным в четыреххлористом углероде.
В настоящее время сотрудниками химической лаборатории, реставрационных мастерских и отдела хранения металла Государственного Исторического музея проводятся дальнейшие исследования в области изучения и реставрации изделий из цинковых сплавов [105].
Особый интерес представляют легкоплавкие цинковые сплавы для центробежного литья, под давлением и в кокиле. Эти сплавы применяются для литья самых различных деталей, в том числе и художественных изделий. Например, декоративные элементы (эмблемы, марки) на автомашинах и холодильниках.
В процессе естественного старения цинковых сплавов происходит уменьшение размеров отлитых изделий (на 0,07-0,09 %). Две третьих усадки происходит в течение 4–5 недель, остальная – в течение многих лет. Для стабилизации размеров применяют термообработку – отжиг (3–6 ч при 100 °C, или 6-10 ч при 85 °C, или 10–20 ч при 70 °C).
Сплавы могут подвергаться пайке и сварке. Однако эти процессы применяют главным образом для заделки дефектов, так как паяные швы имеют низкую прочность. Оловянно-свинцовыми припоями можно паять только предварительно никелированные сплавы. Флюс – подкисленный хлористый цинк. Лучшие результаты дает припой, содержащий 82,5 % Cd, 17,5 % Zn. В этом случае флюс не требуется.
Сварку ведут в восстановительном пламени. Электроды и изделие изготовляют из одного сплава.
Наиболее широко литейные цинковые сплавы используют в автомобильной промышленности для отливки корпусов карбюраторов, насосов и т. д. Помимо этого сплавы применяют для отливки деталей бытовых приборов: стиральных машин, пылесосов и т. п. Эти сплавы нельзя использовать в условиях повышенных и низких температур, так как уже при температуре 100 °C прочность снижается на 30 %, твердость – на 40 %, а при температуре ниже 0 °C они становятся хрупкими.
Для повышения коррозионной стойкости и для декоративных целей на цинковые изделия наносят различные защитные покрытия. Как правило, в качестве покрытий используют медь, никель и хром.
Цинковые сплавы нашли широкое применение для отливки небольших полых художественных изделий, главным образом бюстов, методами заливки в металлическую форму, «литья с выплеском» и при изготовлении ажурных изделий методом литья под давлением. На рис. 3.35 показаны литые модели автомобилей для брелоков, изготовленных последним способом. Толщина стенок отливок не превышает нескольких десятых долей миллиметра [18].

Рис. 3.35. Брелоки для ключей из цинка [18]
Творческая мастерская художественного литья из цинковых сплавов из Москвы специализируется в основном на изготовлении различных решеток и накладных элементов из цинковых сплавов центробежным литьем (рис. 3.36).

Рис. 3.36. Ажурная решетка. Цинковый сплав. Москва, Творческая мастерская художественного литья
В Екатеринбурге на одном из литейных заводах был отлит бюст В. С. Высоцкого из цинкового сплава (рис. 3.37).

Рис. 3.37. Бюст В. С. Высоцкого. Высота 13,5 см. Цинковый сплав. Екатеринбургское литье
Легкоплавкие цинковые сплавы повышенной прочности состоят из 93 % Zn, 4 % Al и 3 % Cu; сплавы средней прочности состоят из 95 % Zn, 4 % Al и 1 % Cu. В эти сплавы добавляют 0,03 % Mg, который предохраняет изделия из этих сплавов от растрескивания. Недостатком некоторых из этих сплавов является низкая коррозионная стойкость, что ограничивает их применение только для условий интерьера, способность с течением времени увеличиваться в размерах и деформироваться. Эти изменения вызываются внутренними превращениями, связанными с распадом твердого раствора меди и алюминия.
В ювелирном деле цинк применяют для приготовления припоев, а также как один из компонентов в различных сплавах.
Для изготовления золотых сплавов с пробой менее 750-й и для получения серебряных сплавов, не содержащих хлорида, применяют только электролитический цинк.
Используя различные технологические приемы (полирование, шлифование, обработку пескоструйным аппаратом), можно получать изделия из цинка разного цвета с различным отражением света. Палитра цветов и отражений в этом металле отличается сдержанностью, что привлекает многих дизайнеров.
Сплавы цинка, меди, магния и алюминия, содержащие свыше 50 % Zn, называемые «замак», имеют высокие литейные свойства. Их часто используют европейские производители сувенирной продукции [105].
3.7. Отливки из алюминиевых сплавовАлюминий – легкий и малоокисляющийся материал, хорошо поддается различным видам художественной обработки. Однако, работая с алюминием, необходимо соблюдать особую осторожность при отжиге, так как он плавится при относительно низкой температуре (660 °C).
Широко используются в литейном деле сплавы алюминия. Чистый алюминий не обладает достаточными литейными свойствами. К тому же он недостаточно прочен.
Алюминий широко используется при изготовлении различных значков, сувениров, недорогих ювелирных украшений, а также как компонент припоев и сплавов цветных металлов.
В чистом виде (99,9 %) может подвергаться анодированию и окрашиванию в золотистый и серебристый цвета. Алюминий также применяют при выполнении монументальных произведений, используя при этом листы толщиной до 3 мм.
Из алюминиевых сплавов изготовляют литые архитектурные детали и скульптуры, а также ювелирные украшения. Для изготовления модных украшений (бижутерии) и шаблонов используется чистый алюминий (99,99 %), естественная окисная пленка которого утолщается посредством анодирования и затем хорошо окрашивается в золотистый и серебристый цвета.
Самая древняя археологическая находка алюминия – пояс с алюминиевым обрамлением на пряжке. Относится она к III тыс. д. э. Однако до сих пор остается тайной за семью печатями производство алюминия в то время.
Однако древнегреческий мыслитель Платон, описывая 2300 лет назад Атлантиду, рассказывал, что жители этой легендарной страны знали, кроме золота и серебра, еще какой-то драгоценный металл. Он был легкий, белый и мягкий. Похоже на алюминий? Да. Но если это был действительно алюминий, то как смогли получить его в столь далекие времена при тогдашней технике? А может быть, это только легенда?
Бокситы – главная руда алюминия. Своим названием этот вид минерального сырья обязан местности Ле-Бо на юге Франции, где в XIX веке впервые были обнаружены его крупные залежи. Однако знакомство человека с этой рудой произошло гораздо раньше – в самом начале нашей эры. Сохранилось письменное свидетельство Плиния Старшего о том, как безымянный мастер изготовил для императора Тиберия (42 год до н. э. – 37 г. н. э.), правившему Римом в 14–27 годах н. э. (рис. 2.10), металлический сосуд. Он поведал императору о том, что металл изготовлен из глинистой породы. Сосуд блестел так, словно был серебряным. К тому же он был необычайно легок. Император, отличавшийся недоверчивостью, подозрительностью и вероломством, приказал казнить мастера, так как побоялся, что доступное «глиняное серебро» обесценит его серебряные сокровища. Загадочная глина осталась безвестной еще на восемнадцать столетий [50].
В литературе неоднократно ссылаются на этот рассказ, а современные авторы почти всегда делают оговорку, что вся эта история – не более чем красивая сказка. Не беремся судить о правдоподобии рассказа. Карл Бакс пишет: «Алхимики того времени твердо верили в то, что все вещества происходят от одного начала и одно вещество может превращаться в другое. Поэтому сам факт получения «серебра из глинозема» римскому императору Тиберию мог показаться заслуживающим доверия» [86]. И это не удивительно: алюминий в горных породах чрезвычайно прочно связан с кислородом, и для его выделения необходимо затратить очень много энергии. Однако каким образом? Принимая во внимание тогдашний уровень развития техники, для нас остается загадкой. Из него не могли выплавить таинственный металл. Или это было «случайным открытием», которое все же позволило при наличии примитивных подсобных средств той эпохи достичь желаемого результата.
Однако в последнее время появились новые данные о принципиальной возможности получения металлического алюминия в древности. Как показал спектральный анализ, украшения на гробнице китайского полководца Чжоу-Чжу, умершего в начале III в. н. э., сделаны из сплава, на 85 % состоящего из алюминия. Могли ли древние получить свободный алюминий? Все известные способы (электролиз, восстановление металлическим натрием или калием) отпадают автоматически.
Могли ли в древности найти самородный алюминий, как, например, самородки золота, серебра, меди? Это тоже исключено: самородный алюминий – редчайший минерал, который встречается в ничтожных количествах, так что древние мастера никак не могли найти и собрать в нужном количестве такие самородки.
О том, что существует самородный алюминий, узнали совсем недавно, впервые он был обнаружен в трапповых горах Сибирской платформы в 1978 году прошлого века. У некоторых ученых эти находки вызывали недоверие, возможно, связанное с тем, что не удавалось удовлетворительно объяснить происхождение алюминиевых химически чистых самородков [12].
Однако возможно и другое объяснение рассказа Плиния. Алюминий можно восстановить из руд не только с помощью электричества и щелочных металлов. Существует доступный и широко используемый с древних времен восстановитель – это уголь, с помощью которого оксиды многих металлов при нагревании восстанавливаются до свободных металлов. В конце 1970-х годов немецкие химики решили проверить, могли ли в древности получить алюминий восстановлением углем. Они нагрели в глиняном тигле до красного каления смесь глины с угольным порошком и поваренной солью или поташом (карбонатом калия). Соль была получена из морской воды, а поташ – из золы растений, чтобы использовать только те вещества и методы, которые были доступны в древности. Через некоторое время на поверхности тигля всплыл шлак с шариками алюминия! Выход металла был мал, но не исключено, что именно этим путем древние металлурги могли получить «металл XIX века».
Но, как это нередко случается, путь нового материала от лаборатории до промышленного производства занимает десятилетия. Так было и с алюминием.
В свободном виде чистый алюминий впервые был получен в 1825 году датским физиком Хансом Кристианом Эрстедом в виде тонкого порошка.
Этот металл начали применять в ювелирном деле как очень дорогой и редкий металл; кольцо, например, сделанное из алюминия ценилось дороже золотого.
Выдающемуся русскому ученому Д. И. Менделееву на юбилей преподнесли брошку в виде маленькой ящерицы. Этот подарок считался сенсацией, так как ящерица была отлита из совершенно нового, чрезвычайно редкого и дорогого материала – алюминия.
Лишь через 20 лет удалось получить новый металл в виде зерен. Затем почти 60 лет он считался драгоценным металлом, не имеющим промышленного применения.
Новый металл получали в небольших количествах химическим методом, и стоил он ненамного дешевле золота. Наряду с золотом и серебром алюминий шел на изготовление ювелирных изделий. Так, в 50-х годах XIX века из алюминия и золота сделали погремушку для сына французского императора Наполеона III. Центральный шар погремушки и корона на нем сделаны из золота, а ангелочки и ручка в виде ангела – отлиты из алюминия. Погремушка украшена драгоценными камнями (рис. 3.38) [128].

Рис. 3.38. Погремушка из алюминия, золота и драгоценных камней. [128]
По приказу Наполеона III были изготовлены алюминиевые столовые приборы, которые подавались на торжественных обедах императору и самым почетным гостям. Другие гости при этом пользовались приборами из традиционных драгоценных металлов – золота и серебра.
Кроме того, Наполеон очень часто даровал своим самым почетным гостям ножи и вилки, сделанные из чистого алюминия. Датский король Кристиан X носил корону из алюминия.
Так, в 1854–1855 гг. было получено всего 25 кг алюминия по цене около 45 руб. золотом за килограмм.
В 1860-е годы каждая парижская модница непременно должна была иметь в своем наряде хотя бы одно украшение из алюминия.
Случались и курьезы и в XX веке – в 1967 году американский дизайнер Оскар де ла Рента произвел сенсацию в мире моды, представив публике купальник из тончайшей алюминиевой нити.
В 1884 году из алюминия отлили верхушку памятника Вашингтону в столице США. Пирамидка весом около 25 килограммов перед установкой на вершине обелиска была выставлена в витрине крупного ювелирного магазина в Нью-Йорке на удивление прохожим, никогда в жизни не видевшим таких количеств драгоценного металла [128].
Затем, в 1886 году одновременно и независимо друг от друга французский металлург Эру и американский физик Холл запатентовали и предложили способ получения алюминия электролизом криолитно-глиноземных расплавов, заложивший фундамент бокситодобывающей и алюминиевой промышленности. Это и положило начало промышленному производству.
Д. И. Менделееву в 1889 году в Лондоне за заслуги в науке был преподнесен ценный подарок: весы, выполненные из золота и алюминия. Распространенность алюминия в горных породах и легкость получения в больших количествах почти совершенно лишили его этой роли. Зато в технике и строительстве алюминий – поистине драгоценный металл.
Дореволюционная Россия не имела своего алюминия. Впервые отечественный алюминий был получен в 1921 году. Тем не менее, в середине XIX века в Петербурге существовал завод статуарного литья, принадлежащий Морану и Плеске, и первые экспериментальные работы по художественному литью из алюминия производились именно на этом заводе. Первой отливкой была скульптура Дианы Габийской [13]. С 1899 года из алюминия литейные мастерские производили мебель и иконостасы.
Н.Г. Чернышевский называл алюминий коротко: «Металл социализма». Первый советский спутник был выполнен из алюминиевого сплава, как и корпуса американских ракет «Авангард» и «Титан», применявшихся для запуска первых американских спутников, детали космической аппаратуры.
За 115 лет выпуск алюминия в мире увеличился почти в 100000 раз. История не знает таких темпов применения какого-либо другого промышленного металла.
Художественные изделия из алюминиевых сплавов, как литейных, так и деформируемых, хорошо полируются до зеркального блеска, напоминающего никелированные поверхности. Они достаточно устойчивы и декоративны в полированном состоянии. Чистый алюминий устойчив против коррозии, а все виды сплавов менее устойчивы.
Перечень изделий, изготавливаемых из алюминиевых сплавов, велик. Это и крупные литые скульптурные и архитектурные детали, и предметы интерьера. Даже посуду, классически изготовлявшуюся из чугуна, теперь с успехом заменил алюминий.
В наше время алюминий широко используется для изготовления скульптур. К лучшим образцам относятся работы «В космос» скульптура В. Шевченко (Рязань, Краснодар, Артемовец), «Защитники Брестской крепости» скульптура А. Потривова (Брест), «Колхозница со снопом» скульптура С. Буянина (высота статуи 2 м), «Эстафета мира» скульптура И. Тенитина, «Памятник Олегу Кошевому» скульптура Писаревского (Москва, школа № 622), «Купальщица» скульптура А. Чусовой (Сахалин, Анапа, Челябинск, Краснодар, высота статуи 2 метра) и другие.
Кроме того, алюминий все больше применяется в ювелирном производстве в качестве замены серебра и золота.
Правообладателям!
Данное произведение размещено по согласованию с ООО "ЛитРес" (20% исходного текста). Если размещение книги нарушает чьи-либо права, то сообщите об этом.Читателям!
Оплатили, но не знаете что делать дальше?