Текст книги "Практичная мебель для летней дачи"
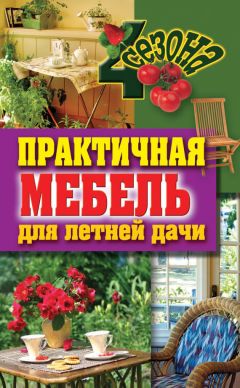
Автор книги: Галина Серикова
Жанр: Хобби и Ремесла, Дом и Семья
Возрастные ограничения: +12
сообщить о неприемлемом содержимом
Текущая страница: 4 (всего у книги 12 страниц)
Данный способ обработки используется для древесины пористых пород (орех, бук, дуб) и представляет собой процесс нанесения и растирания специальных мастик. Предварительная подготовка в виде грунтования в данном случае не требуется, поскольку восковые мастики сами по себе являются хорошими заполнителями и очень прочно держатся на поверхностях.
Перед вощением древесину необходимо зачистить, отшлифовать и удалить ворс. Наиболее распространены следующие рецепты восковых мастик:
– 30 частей воска, 10 частей стеарина, 10 частей мыла, 40 частей скипидара, 10 частей канифоли;
– 25 частей воска, 12 частей мыла, 5 частей охры, 18 частей раствора поташа, 40 частей канифоли;
– 35 частей воска, 60 частей скипидара (бензина), 5 частей канифоли.
Канифоль, стеарин и воск следует расплавить при температуре 80–90 °C. В полученную смесь добавьте водный раствор поташа и раствор с мыльной стружкой. Наносите приготовленную мастику с помощью жесткой кисти и следите за тем, чтобы покрытие было однородным, без пропусков.
Мастику следует использовать охлажденной до 20–25 °C и сушить при комнатной температуре не менее 24 часов. После того как поверхность полностью высохнет, ее следует отполировать суконкой. Сначала у вас могут возникнуть с этим сложности из-за налипания на нее воска, но по мере работы темная и грязная поверхность древесины будет становиться гладкой и блестящей, станет видна текстура.
После полировки древесину следует высушить (не менее 24 часов), а затем протереть мягкой чистой тканью. Для усиления глянцевого эффекта можно покрыть поверхность смесью щелочного лака и щелочной политуры, взятых в соотношении 1: 1.
Обшивка пластиком и пленкойДля получения лучшего качества обработки специалисты рекомендуют обшивать детали до сборки изделия. Облицовочный материал вырезается в соответствии с габаритами детали с припуском 2 мм. Пластик наклеивается на брусья, фанеру, ДСП, ДВП и доски с помощью карбамидного клея или поливинилацетатной эмульсии. Хороший результат можно получить, применяя синтетический клеящий состав БФ-2, который представлен в продаже во флаконах или тюбиках и готов к использованию.
Клей следует наносить на поверхность с помощью кисти ровным слоем. БФ-2 наносится на обе склеиваемые поверхности два раза. Первый слой в данном случае выполняет функции грунтовки. После его нанесения поверхность необходимо оставить для пропитки на 5 минут, а затем покрыть ее вторым слоем. Теперь пластик нужно наложить на деталь, накрыть картоном и запрессовать в струбцинах (другой вариант – положить сверху лист фанеры и накрыть прессом) на 4 часа. После этого снимите струбцины и оставьте деталь для окончательного высыхания еще на 4 часа.
Облицовка гладкой поверхности может быть выполнена специальной бумагой с печатным рисунком под цвет и фактуру кожи, древесины, камня, ткани и др. Наиболее часто используется бумага, имитирующая срез древесины различных пород. Листовой материал выпускается в виде многослойных и однослойных листов.
В зависимости от режимов пропитки, сушки и используемых пропиточных составов выпускается пленка нескольких типов – А, В, С и D. Первые три разновидности используются для облицовки всего изделия и подлежат отделке. Последний тип применяется для облицовки внутренних поверхностей и не требует отделки.
Материалы для облицовки, изготовленные на основе бумаги, пропитанной смолами, представлены в продаже в виде рулонов. Они бывают как однослойными, так и многослойными.
Рулонные пленки на основе бумаги могут обладать различными характеристиками: иметь повышенную эластичность, лакированную поверхность с рисунком пор древесины и без него, не иметь лакового покрытия и т. д. Такие пленки часто применяются при изготовлении мебели и могут быть использованы в условиях домашней мастерской.
В продаже представлены пленки таких типов, как РП, РПЛ, РПТ, РПЭ и РПЛЭ.
Пленки РП выпускаются без лакокрасочного покрытия, РПЛ – с лакокрасочным покрытием, РПТ имеют специальное теснение в виде пор древесины. Пленки остальных типов отличаются повышенной эластичностью. Ширина пленки составляет 875, 1000, 1760 или 1850 мм. Для облицовки кромок необходимо приобрести специальную пленку, которая выпускается на бумажной основе в виде рулонов и полос, двухслойных и однослойных. Ее ширина варьируется от 14 до 50 мм с градацией 1 мм. Выпускаются кромочные материалы следующих марок:
– МКР-1;
– МКР-1 к;
– МКР-2 и др.
МКР-1 представляет собой однослойный рулонный материал для облицовки кромок, его поверхность отделывается лаком. Он отличается высокой степенью устойчивости к воздействию внешней среды и предназначен для отделки кухонной мебели. МКР-2 – двухслойный рулонный материал для облицовки кромок.
Для производства торговой, медицинской, кухонной и другой мебели применяются декоративные бумажно-слоистые пластики (ДБСП). При их изготовлении используются пленки на основе пропитанной бумаги. Лицевой (декоративный) слой выполняется из бумаги с печатным рисунком или фоновой, а под ним располагаются 4–5 слоев менее ценной бумаги.
Чтобы повысить устойчивость лицевого слоя к истиранию, на поверхность определенных видов пластика можно напрессовать тонкую прозрачную пленку, которая изготавливается на основе бумаги «оверлей».
ДБСП может быть однотонным, разноцветным, украшенным печатным рисунком под кожу, древесину, камень и т. д. Поверхность пластика может быть глянцевой или иметь различную степень матовости.
В зависимости от назначения ДБСП делятся на:
– конструкционные;
– облицовочные;
– формуемые.
Конструкционные – это пластики толщиной более 1 мм, которые используются как конструкционный материал. Облицовочные пластики имеют толщину менее 1 мм и служат для покрытия плоских поверхностей. Формуемые пластики под воздействием давления и тепла меняют форму и поэтому могут использоваться для облицовки фасонных деталей.
ДБСП отличаются высокими физико-механическими свойствами. Они создают хороший декоративный эффект, легки в обработке, устойчивы к воздействию высокой температуры, воды, пара, щелочей, кислот, бытовых жидкостей и др. Этот материал довольно стоек к истиранию и ударам. Кроме того, с него легко удаляются загрязнения.
Стандартные размеры листов ДБСП: толщина – 1, 1,3, 1,6, 2, 2,5 или 3 мм, длина составляет от 400 до 3000 мм, а ширина – 4001600 мм (с шагом в 25 мм).
В соответствии с характеристиками лицевой поверхности выделяют пластик трех марок:
– А (используется для изделий, требующих высокой степени износостойкости, например, для столешниц);
– Б (применяется для изделий, которые эксплуатируются в менее жестких условиях);
– В (используется в качестве поделочного материала).
Для лицевой поверхности пластика используются следующие обозначения:
– Г (глянцевая);
– М (матовая);
– О (однотонная);
– Р (с печатным рисунком);
– З (с защитным слоем).
В основном для облицовки мебели применяется ДБСП толщиной до 1,3 мм, поскольку более толстый пластик не так хорошо приклеивается.
Популярны также облицовочные материалы, изготовленные на основе полимеров. При производстве мебели часто используются материалы на основе поливинилхлоридной смолы (ПВХ), смеси АБС-пластика и поливинилхлорида (ПВХ-АБС), а также поливинилфторида (ПВФ) и некоторые другие.
Облицовка шпономДля лицевой облицовки деревянных деталей применяется строганый шпон. Он изготавливается из сортиментов хвойных и лиственных пород, а также из древесных наростов (капа) древесины всех пород. Рисунок лицевой поверхности зависит от породы древесины, из которой сделан шпон, и направления среза относительно годичных колец.
Различают следующие виды шпона (табл. 1):
– радиальный;
– полурадиальный;
– тангентальный;
– тангентально-торцовый.
Таблица 1. ВИДЫ ШПОНА

Толщина строганого шпона в зависимости от используемой древесины указана в табл. 2
Таблица 2. ТОЛЩИНА СТРОГАНОГО ШПОНА

В продаже представлен строганый обрезной (обрезается по длине с двух сторон), строганый прирезной (обрезается по длине с одной стороны) и необрезной шпон. Маркировку строганого шпона следует расшифровывать следующим образом: дуб Р1-1,4 – шпон, изготовленный из древесины дуба, вид – радиальный, сорт – 1, толщина листа составляет 1,3 мм.
Лущеный шпон может применяться как в качестве подслоя, так и для лицевой облицовки. Его получают посредством среза по спирали тонкого слоя древесины. Для этого берут ольху, березу, дуб, ясень, липу, кедр и лиственницу. В результате получается шпон, текстура которого близка к тангентальной. Следует отметить, что по декоративным качествам он уступает строганому шпону.
В зависимости от обработки и качества древесины лущеный шпон лиственных пород бывает пяти сортов – А, АВ, В, ВВ и С. А шпон хвойных пород представлен четырьмя сортами – АХ, АХВ, ВХ и СХ.
Для лицевой облицовки применяются все виды лущеного шпона листовых пород. Они представлены в продаже в виде листов шириной 150-2500 мм и длиной 800-2500 мм. Толщина шпона лиственных пород составляет 0,35-1,25 мм, хвойных – 1,2–4 мм.
В большинстве случаев это шпон красного дерева (краснокоричневого цвета), ореха (обладающий интересной текстурой), дуба (желто-коричневого цвета), бука (оранжевого цвета) или ясеня (розово-желтого цвета и с волнистой текстурой).
Набор шпона
В зависимости от желаемого декоративного эффекта можно сделать любой набор шпона. Он может быть простым или фигурным. В первом случае все полосы шпона должны быть одинаковыми (либо близкими по цвету и текстуре) и иметь продольное направление волокон, а текстуру следует располагать симметрично оси набора.
Фигурный набор (рис. 12) предполагает выполнение различных рисунков из отрезков шпона: в рост, с контрастными полосами, в крест, в шапку, в елку и др.

Рис. 12. Набор шпона: а, б – в рост; в, е – в крест; г, д – с контрастными полосами; ж – в шапку; з – с фризом; и – в конверт
Набор в рост может выполняться вдоль или поперек пласти. При этом направление волокон шпона не должно совпадать с таковым на облицовываемой поверхности. Последнее очень важно, иначе при усыхании древесины наклеенный шпон может покрыться трещинами.
В зависимости от вашего желания можно использовать поперечный или косой набор. При подборе шпона важна длина имеющихся листов: если она меньше длины облицовываемой поверхности, то их следует располагать в поперечном направлении, чтобы не было стыка по длине. Если шпон очень маленького размера, подберите рисунок в двух направлениях: по ширине и длине с использованием фриза или контрастных полос, сделанных из шпона других пород. Другой вариант – набор кусков шпона методом «в елку» под углом в 45° к краям детали.
Помните о том, что стороны шпона имеют определенные отличия. Правая (лицевая) сторона – наружная, она состругивается с чурбана, а левая (обратная) сторона более рыхлая и нередко имеет микротрещины.
Для лицевой облицовки следует использовать правую сторону шпона. При выполнении разметки обязательно оставьте припуск в 4–5 мм: это потребуется вам для подгонки стыков.
Резать шпон нужно хорошо заточенным ножом с использованием линейки. Сначала нажим должен быть незначительным, а затем его можно усилить. Чтобы отрезать шпон, вам потребуется сделать ножом 3–4 прохода. Если вы двигаетесь вдоль волокон, то не следует вести лезвие навстречу годичным слоям, так как в результате произойдет косой разрыв материала между слоями.
Разрезать необходимо только в направлении годичных слоев. Если вы режете шпон поперек волокон либо под углом к ним, то сначала с помощью ножниц выполните встречный надрез длиной 10–15 мм. Это поможет избежать разрыва шпона, когда вы будете надавливать на него лезвием ножа.
Если шпон необходимо вырезать по кривой линии, для этого следует взять ножницы. Для фуговки кромок соберите листы шпона в пачку толщиной 18–20 мм, аккуратно зажмите в струбцинах и обработайте фуганком.
Чтобы проверить качество фугования, приложите листы друг к другу обработанными кромками. Если между ними не будет зазора, это значит, что фугование выполнено качественно. Нарежьте заготовки шпона, разложите их поочередно на каждой оклеиваемой детали и посмотрите, правильно ли выполнен набор. Особое внимание обратите на точность стыковки.
Для удобства пронумеруйте заготовки и поставьте эти же номера на соответствующие листы облицовываемой поверхности. В местах стыковки проведите стыковочные линии.
Наклеивание шпона
Прежде чем приступать к наклеиванию шпона, внимательно осмотрите облицовываемую поверхность. При необходимости устраните неровности, сколы, выбоины и другие повреждения. После этого поверхность следует обработать шкуркой.
Если основа сделана из хвойных пиломатериалов, нужно проверить, не выступает ли где-нибудь смола. Ее необходимо аккуратно соскоблить ножом и промыть очищенную поверхность 5–6 %-ным раствором кальцинированной соды.
Шпон очень плохо приклеивается к сучкам, поэтому их рекомендуется высверлить, а отверстия заделать пробками с помощью клея. Оптимальная влажность шпона составляет 8-10 %, а влажность облицовываемых деталей – 7–9 %.
Чтобы выровнять поверхность основы, используйте шпатлевку следующих составов:
– 60 частей канифоли, 30 частей цинковых белил, 10 частей древесной муки (канифоль предварительно расплавьте);
– 67 частей карбамидного клея и 33 части древесной муки.
Наиболее подходящим для наклеивания шпона является белковый клей (костный и мездровый). В случае использования такого средства обязательно проверьте его: в приготовленную массу погрузите деревянную палочку, хорошо перемешайте и достаньте ее. Качественный клей стекает с нее прозрачной непрерывной струей. Если же масса стекает каплями, значит, клей недостаточно густой и не подходит для фиксирования шпона. Слишком густой клей стекает очень медленно или не стекает вовсе. Такое средство также нельзя применять для облицовки шпоном.
Чтобы не выбрасывать испорченный состав, в первом случае добавьте твердые частицы клея, а во втором – воду. После этого клей следует разогреть до нужной консистенции и снова проверить с помощью деревянной палочки.
При изготовлении мебели на фабриках шпон наклеивается в гидравлических прессах с системой подогрева. В домашних условиях вам не остается ничего другого, как применять ручной способ. Он заключается в том, что на подготовленную поверхность древесины наносится тонкий слой клея (вдоль волокон). При этом нужно следить, чтобы не было комочков и сухих (необработанных) участков. После нанесения слоя клея деталь выдерживайте в течение 3 минут, после чего положите на нее листы шпона. Поместив шпон на основу, аккуратно разгладьте его с помощью чистой увлажненной ткани, а затем притрите. Обратите внимание на то, что утюг или притирочный молоток должны быть подогреты до температуры 160–170 °C. Это необходимо для того, чтобы состав под шпоном нагрелся и усилились его клеящие свойства. Шпон притирается вдоль волокон по направлению от центра к краям.
Постарайтесь в процессе притирки выдавить излишки клея и пузырьки воздуха. Выполнять эту процедуру следует до полного приклеивания шпона. Излишки клея нужно сразу же удалить с помощью влажной тряпки.
В некоторых случаях шпон наклеивается так: на основу наносится тонкий слой клея и оставляется до полного высыхания. Через 40–50 минут поверхность клея нужно обработать мокрой тряпкой (или губкой), на нее положить листы шпона и притирать их с помощью разогретого утюга. При правильном выполнении данной процедуры шпон наклеивается быстро и прочно.
Для удобства листы шпона перед наклеиванием можно собрать в стопку нужных размеров. Разложите их (в соответствии с подбором) лицевой стороной вверх, состыкуйте отфугованные кромки и скрепите их клеевой лентой. Набор следует перевернуть и поместить на облицованную поверхность.
В домашних условиях проще всего наклеивать шпон отдельными листами последовательно (один за другим). Работать в этом случае нужно, двигаясь от центра к краям. Наносите клей не на всю поверхность сразу, а лишь на тот участок, куда наклеивается очередной лист шпона (помните о том, что набор пронумерован и очерчен).
Основная сложность при таком способе облицовки обычно заключается в том, что влажный шпон закручивается и расширяется поперек волокон. Таким образом, как только вы притираете первый лист и наклеиваете следующий (рядом с ним) вдоль стыка, который параллелен волокнам, сразу же появляется складка, связанная с расширением шпона. Если вы снова притрете этот участок за счет сдвига листа, то, после того как он высохнет и лист шпона сожмется, шов разойдется. Чтобы этого не произошло, следующий лист нужно притирать не впритык к предыдущему, а с небольшим нахлестом на него. После расширения шпона нахлест нужно разрезать так, чтобы подровнять оба листа шпона.
Обрезанные полоски удалите, а место стыка листов снова притрите теплым утюгом. Чтобы предотвратить расхождение шва, поверх него следует наклеить клеевую ленту, которую через некоторое время можно будет удалить.
Рабочее местоДля столярных работ вам обязательно потребуется верстак. Это рабочее место, на котором выполняются все необходимые операции: разметка, пиление, строгание и сборка готового изделия. В конструкцию верстака (рис. 13, а) входят подверстачье и крышка. Последняя состоит из верстачной доски толщиной 60–70 мм, передних тисков (или зажимного винта) с подкладной доской, задних тисков с зажимной коробкой и лотка, на котором раскладываются необходимые для работы инструменты.

Рис. 13. Столярный верстак (а) и верстачная доска со съемными тисками (б) (размеры указаны в миллиметрах): 1 – верстачная доска; 2 – передние тиски; 3 – задние тиски с коробкой; 4 – лоток; 5 – клиновой упор; 6 – подверстачье
В зажимной коробке и верстачной доске предусмотрены сквозные отверстия, в которые помещаются клиновые упоры, передвигаемые по высоте. Последние предназначены для фиксации обрабатываемой заготовки в горизонтальном положении. Между передвигаемым и неподвижным упорами можно установить деталь любой длины.
Передние тиски используются для закрепления детали в горизонтальном или вертикальном положении, а задние применяются лишь для вертикальной фиксации. В подверстачье можно сделать удобный шкаф для хранения необходимых инструментов.
Конечно, работать на столярном верстаке намного удобнее, чем на обычном столе, однако в доме не всегда есть место для него. Если вы столкнулись с подобной проблемой, вместо верстака можно использовать обычный стол, разместив на нем верстачную доску (рис. 13, б). Она прикрепляется к нему струбцинами, благодаря чему конструкцию можно легко разобрать после завершения работы.
Неплохой альтернативой могут стать и устойчивые деревянные опоры. Положите на них основную доску, а позади нее поместите еще одну доску. Последняя будет использоваться как место для инструментов. К верстачной доске необходимо прикрепить слесарные тиски с губками шириной 60–80 мм для закрепления обрабатываемых заготовок.
Рядом со столярным верстаком оборудуйте полки для хранения необходимых приспособлений и инструментов, чтобы при необходимости вы всегда могли ими воспользоваться. Позаботьтесь об освещении, которое должно быть достаточным для того, чтобы можно было работать без сильного напряжения зрения. Если ваше рабочее место находится в помещении, оно обязательно должно проветриваться, так как при изготовлении мебели придется иметь дело не только с древесиной, но и с лакокрасочными составами.
Металл
Для работы в домашних условиях металл применяется значительно реже, поскольку все операции по его обработке значительно сложнее, и не каждый мастер владеет техникой сварки. Поэтому ниже будет лишь кратко рассказано о ковке, так как эта информация может пригодиться вам для оформления беседок, пергол, декоративных сооружений и уличной мебели.
Специалисты рекомендуют использовать для работы металл с низким содержанием углерода или прокатную сталь различного сечения: тавр, швеллер, уголки, квадратные и круглые прутья. Все стальные элементы уличной мебели необходимо защитить от влияния атмосферы специальными покрытиями, например оцинковкой, эмалью, краской и др.
Вместо стальных деталей можно использовать профили из алюминия и его сплавов, так как они в меньшей степени подвержены воздействию внешней среды и не нуждаются в постоянном обновлении защитного покрытия.
Методика свободной ковки известна с древних времен. Металл нужно разогреть до определенной температуры, а затем придать ему желаемую форму. Но прежде чем приступить к этому, следует правильно устроить рабочее место (рис. 14).

Рис. 14. Рабочее место для свободной ковки металлов: 1 – рабочий стол; 2 – тиски; 3 – колода; 4 – бочка с водой; 5 – резервуар для угля; 6 – наковальня; 7 – скоба для инструментов; 8 – горн; 9 – полка; 10 – огнетушитель; 11 – вытяжной вентилятор
Помещение, в котором вы будете работать, должно быть достаточно большим и хорошо освещенным. Желательно, чтобы оно состояло из двух комнат. В одной из них вы сможете выполнять эскизы будущих изделий и другие подготовительные работы, а в другой – ковать.
Начните с прорисовки чертежей, соблюдая все необходимые формы и размеры. Соблюдайте идентичность отдельно выполненных деталей и следуйте общему стилю фигурных элементов.
Если у вас нет возможности оборудовать специальное помещение для ковки, не расстраивайтесь. Все необходимые операции можно выполнить и на садовом участке. Вам потребуются лишь источник огня, над которым можно разогреть металл, и приспособление типа наковальни, чтобы придать заготовке желаемую форму. Возможно, вас это удивит, но горн и наковальню можно сделать самостоятельно.
Горн, изготовленный своими руками (рис. 15, а), представляет собой бадью из черного металла, которая устанавливается на землю или металлический стол. К нижней части бадьи следует прикрепить кусок трубы, диаметр которой должен быть таким, чтобы на нее можно было надеть патрубок пылесоса. Для работы извлеките из пылесоса все фильтры: это поможет сильнее нагнетать воздух.

Рис. 15. Инструменты для ковки металлов: а – горн; б – наковальня; в, г – кузнечные зубила; д – изготовление раскатки; е – гвоздильня; ж – подкладки для сгибания заготовок
Внутреннюю поверхность бадьи покройте слоем обычной глины толщиной 3 см. Ее необходимо хорошо высушить, а затем нанести еще несколько слоев, тщательно высушивая каждый из них. Верхний слой, толщина которого составляет 5–7 мм, должен состоять из сухого каолина или любой огнеупорной глины (9 частей), прокаленной буры (1 часть) и воды (2 части).
Буру, глину и каолин необходимо соединить в эмалированной емкости и вымешивать до тех пор, пока не образуется однородная масса. После этого добавьте воду и перемешивайте до тестообразной консистенции. Полученную смесь ровным слоем нанесите поверх глины и дождитесь полного высыхания, после чего тщательно затрите образовавшиеся трещинки оставшейся массой. При необходимости снова повторите все после просушивания.
Заполните сухой горн древесным углем, включите пылесос и разожгите уголь. Жечь его следует до тех пор, пока обмазка не раскалится до красного цвета. Периодически подкладывайте новые порции топлива. После того как горн остынет, его можно использовать для работы. Данное приспособление выдерживает нагрев до 1600 °C.
Простую наковальню (рис. 15, б) моно сделать из стальной заготовки большого размера или отрезка крупного тавра. Кроме нее и горна, вам понадобятся некоторые инструменты. Для начала приобретите три молотка весом 0,5, 1 и 2 кг и полукувалду, которая насаживается на ручку длиной 70 см.
Кузнечное зубило (рис. 15, в) можно купить или изготовить из обычного крупного зубила, присоединив к нему ручку из проволоки диаметром 4 мм (рис. 15, г). Точно так же можно сделать кузнечные пробойники и просечки.
После протяжки металла его следует разгладить специальным инструментом, который называется «гладилка». Альтернативой ему может служить полукувалда с длинной ручкой. Вместо раскатки можно использовать переделанный молоток с бойком (рис. 15, д).
Для изготовления специальных гвоздей и шляпок заклепок понадобится гвоздильня (рис. 15, е). Она изготавливается из стального бруска на сверлильном станке. Сгибание металлических деталей производится с помощью подкладок (рис. 15, ж), которые также можно выполнить самостоятельно.
К основным приемам технологии свободной ковки относятся следующие:
– вытяжка;
– осадка;
– рубка;
– разрубка;
– пробивка отверстий;
– гибка;
– закручивание;
– выглаживание;
– насекание рисунка;
– набивка фактуры и рельефа;
– кузнечная сварка.
С их помощью вы сможете превращать обычные металлические прутья в стильные и красивые изделия. Для этого поместите заготовку в горн, разогрейте до температуры 1200 °C (она должна стать светло-желтой), захватите специальными щипцами и выложите на наковальню, где, используя ударный инструмент, придайте пруту желаемую форму.
Если вы работаете медленно и металл успевает остыть, то его необходимо периодически подогревать, иначе на поверхности готового изделия могут появиться изломы и трещины. Часть приемов художественной ковки показана на рис. 16 и 17.

Рис. 16. Приемы гибки полосовой стали: а – на роге наковальни; б – на оправке; в – в тисках на вилке; г – на уклоне; д – на радиусной оправе; е – на спирали

Рис. 17. Гибка и соединение полусфер из полосовой стали
Ажурные металлические детали можно также изготовить, применяя метод холодной гибки. Для этого вам потребуется простое приспособление, которое устанавливается на верстаке (рис. 18, а). Чтобы изготовить его, сделайте рычаг из полосовой стали толщиной 5–6 мм и шириной 40–50 мм и аккуратно приварите к нему втулку. При работе он будет вращаться вокруг штыря-оси, закрепленного на крышке верстака. На коротком конце рычага выполните несколько отверстий, в которые будут вкручиваться штыри-упоры.

Рис. 18. Приспособления для холодной гибки полосовой стали
Для закрепления штырей-упоров сделайте в рабочем столе нужное число отверстий в зависимости от формы изготавливаемых деталей. Штыри-упоры и штырь-ось фиксируются на верстаке двумя гайками, под которые подкладываются шайбы толщиной 3 мм и диаметром 50 мм. Фиксация штыря-упора на рычаге осуществляется с помощью двух гаек, закручивающихся с двух сторон рычага.
Чтобы изготовить штырь-ось и штыри-упоры, используйте шпильки и болты толщиной 10 мм и более (соответственно предполагаемым нагрузкам).
Гибка металлической полосы выполняется следующим образом. Полоса закрепляется, как отмечено на рисунке пунктиром. Затем переставляются штырь-упор на рычаге и неподвижный штырь-упор на верстаке (при необходимости можно также задействовать дополнительные штыри), в результате чего получаются самые различные изогнутые детали желаемой формы.
Иногда для получения крутых изгибов и сгибания мелких деталей применяется еще одно приспособление (рис. 18, б). Необходимо установить на том же штыре-оси вращающийся фигурный рычаг, уложить и зафиксировать полосу между двумя-тремя штырями-упорами (они показаны на рис. 18 пунктиром) и повернуть рычаг по часовой стрелке. Так вы добьетесь того, что полоса изогнется вокруг первого штыря-упора.
Если требуется придать изгиб нескольким одинаковым деталям, следует сделать их эскизы в натуральную величину и написать план гибки. Специалисты рекомендуют гнуть сначала одни участки каждой детали, а затем другие. Используя зубило, сделайте нужно количество деталей заданного размера, на каждой заготовке выполните завитки сначала с одной стороны, потом с другой. Во избежание ошибок обязательно сравнивайте каждый изгиб с эскизом или образцом.
Итак, все детали готовы, и вам остается лишь создать из них единую конструкцию. Это можно сделать с помощью сварки или заклепок. Следует учитывать, что использование второго способа возможно лишь в том случае если рисунок элемента не слишком сложный, что позволяет подвести упор в нужное место, без усилий достать до головки заклепки ударным инструментом и т. д.
Изделия, имеющие сложные завитки, рекомендуется сваривать выпрямителем или бытовым сварочным трансформатором (ТСК-500). Если у вас нет ни того, ни другого, воспользуйтесь ручной дуговой, или термитной сваркой. Сварка производится с помощью термитного карандаша (рис. 19, а), который можно изготовить самостоятельно. Для этого вам потребуется кусок проволоки из углеродистой стали. Ее толщина выбирается в зависимости от размера соединяемых деталей и составляет 2–5 мм. Чем толще элементы, тем большего диаметра она должна быть. Сверху проволока покрывается так называемым термитом. Чтобы приготовить его, необходимо соединить опилки алюминия (не использовать силумин) и железную окалину в пропорции 23: 77. Желательно, чтобы размеры опилок и окалины не превышали 0,5 мм. Перед тем как наносить полученную смесь на проволоку, добавьте в нее нитроцеллюлозный клей. Его количество должно быть таким, чтобы в результате получилась густая однородная масса.

Рис. 19. Изготовление термитных карандашей: а – термитный карандаш; б – устройство для изготовления термитных карандашей
Чтобы термитный карандаш поджигался, на его конец нужно нанести затравку на основе того же клея. Она состоит из бертолиевой соли (KCIO3) и мелких алюминиевых опилок, взятых в соотношении 2:1.
Используя один карандаш, можно соединить 6–8 элементов конструкции. Учитывая это, их нужно заготавливать с запасом. Упростить данный процесс поможет специальное устройство, с которым вы сможете делать 10 карандашей одновременно (рис. 19, б). Оно имеет деревянное основание с гофрированной алюминиевой полосой. С каждого торца к ней прижаты две стенки из алюминия, снабженные отверстиями для фиксации проволоки-основы.
Приготовьте разделительный состав (65 % керосина и 35 % парафина) и смажьте им внутренние поверхности гофрированной полосы. Как только он высохнет, в отверстия стенок вставьте проволочные стержни, заполните секции термитом и дайте ему высохнуть. После этого извлеките карандаши и нанесите затравку на их концы. Головки карандашей оберните бумагой и уберите на хранение в сухую коробку.
В процессе сварки глаза обязательно должны быть защищены очками с увиолевыми стеклами.
Правообладателям!
Это произведение, предположительно, находится в статусе 'public domain'. Если это не так и размещение материала нарушает чьи-либо права, то сообщите нам об этом.