Текст книги "Работы по металлу"
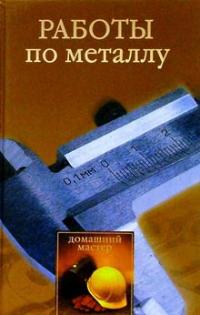
Автор книги: Наталья Коршевер
Жанр: Техническая литература, Наука и Образование
сообщить о неприемлемом содержимом
Текущая страница: 18 (всего у книги 20 страниц)
Теперь, после ознакомления с кузнечным ремеслом, рассмотрим процесс создания с его помощью произведений искусства. Конечно, можно попробовать ковать что-либо на глазок и посмотреть, что в результате этого получится. Однако в этом случае вряд ли изделие обрадует кого-либо. Поэтому для получения заранее намеченных форм и узоров начать нужно с эскиза и чертежа.
Подготовка чертежа
При составлении эскиза следует учитывать свойства материала: каким бы тонким ни хотелось сделать тот или иной декоративный элемент, металл должен сохранять запас прочности. Кроме того, развивать композицию лучше в соответствии с направлением волокон, в противном случае изделие получится хрупким.
Когда при сварке образуется чересчур много окалины, размеры изделия уменьшаются. Усадка происходит и во время остывания, вытяжки и других кузнечных операций. Поэтому рисунок делается с напуском, то есть чуть больше, чем требуемая деталь.
Необходимо знать массу отхода при выполнении той или иной операции, чтобы правильно рассчитать размер.
Далее на плотной бумаге (лучше всего подойдет бумага «крафт») необходимо сделать чертеж в натуральную величину. Для отдельных и повторяющихся плоских элементов лучше приготовить шаблоны с нанесением напусков и требуемых размеров. Сверять с ними деталь можно на протяжении всего процесса работы.
Сложные и гнутые детали, как никакие другие, нуждаются в точном чертеже. Сделать его легко с помощью проволоки, из которой изготовляется макет в натуральную величину. В местах изгибов и ответвлений ставятся метки, проволоку выгибают и переносят полученные размеры на чертеж.
Часто шаблоны или пробные образцы делают из жести, что позволяет изгибать их в нужных местах. Это дает возможность заранее обдумать последовательность операций и уточнить размеры деталей в процессе ковки.
Декоративные элементы
Для нанесения на поверхность кованых изделий рисунка изготовляют специальные штампы, или пуансоны. Мелкий узор легко пропечатывается на листьях и других плоских элементах поковки. Чтобы выбить орнамент на круглых или фигурных деталях, используют фигурные обжимки, оправки, гладилки, а также кузнечные формы. Композиции чаще всего включают в себя кованые растительные элементы. При всем разнообразии форм способы их изготовления почти одинаковы.
Ковка листа
Для этой детали больше подходит листовая заготовка, но можно сделать листок и из конца прутка, выполнив осадку с последующей раскаткой и придав нужную форму зубилом.
В первую очередь выковывают ножку листа. Она должна быть толще и длиннее необходимых размеров, так как часть металла уйдет при нагреве, а часть пойдет на сварку. После этого обжимкой с полукруглым углублением выполняют центральную жилку листа. Контур листа вырубают полукруглым зубилом по шаблону, им же наносят мелкие элементы отделки.
Гибку выполняют при нагреве за один раз. При этом часть рисунка иногда портится, и тогда окончательную обработку выполняют зубилом уже в самом конце.
Части листа можно загнуть относительно друг друга, в результате получится очень необычный и красивый лист (рис. 158).

Рис. 158. Последовательность операций при изготовлении листа.
Для придания изделию выпуклой формы рекомендуется использовать фигурный верхник с соответствующей ему подкладкой. Но лист можно изготовить и на плоской поверхности наковальни.
Изделию высадкой придают правильную форму, обратной стороной ручника или специальной полукруглой подбойкой делают рельеф. Поковка при этом раздается в стороны, и лист приобретает законченный вид. Центральную жилку выковывают секачом или зубилом.
Волюты
Так называются декоративные элементы, состоящие из всевозможных завитков. Их можно отковывать из одного куска, либо свивать в холодном состоянии и сваривать из отдельных деталей (рис. 159).

Рис. 159. Изготовление волюты: а – вырубка защепа; б – вырубка в тисках; в, г – формирование завитка; д – готовая волюта.
У цельных волют в первую очередь отковывается основной изгиб. Делается это на роге наковальни с помощью ручника или кувалды. В местах, где в дальнейшем будут вырубаться дополнительные ответвления, заранее производится осадка.
Короткий отгиб называется защепом (рис. 159, а). Он представляет собой самостоятельный элемент, но иногда к нему приваривают отдельные элементы композиции. Защеп делается горизонтально или вертикально с помощью тисков (рис. 159, б).
Завитки вырубают зубилом на наковальне, начиная с противоположного от вершины конца. Отделив от заготовки полосу нужной длины, ее самостоятельно загибают на шпераке (рис. 159, в, г). На заключительном этапе волюту правят, где нужно проводят высадку или вытяжку.
Если все завитки загибаются в одну сторону, то волюту можно сделать за одно нагревание. Завитки, загнутые в противоположную от основной линии сторону, выполняют при местных накаливаниях.
При желании можно украсить и дверь своего дома, особенно в сельской местности. Для основы двери достаточно взять достаточно толстые склепанные кованые полосы. Закрыть их листовым материалом. Для красоты хорошо бы использовать различные накладные элементы: цветы, розетки, завитки.
А чтобы дверь стала произведением искусства, можно выковать оригинальный замок, ручку-стукалу, жиковины.
Сборка кованых изделий
При изготовлении сложных композиций какие-то части приходится выполнять отдельно от основы. Для того чтобы осуществить сборку, необходимо иметь ясное представление о способах скрепления кованых деталей (рис. 160).

Рис. 160. Различные способы скрепления частей кованых изделий.
Соединения могут выполнять функциональную роль, а также быть самостоятельными художественными элементами. В зависимости от этого сборка выполняется несколькими способами.
В композициях с подчеркнутым растительным стилем детали просто свариваются или склепываются. Крепления не несут смысловой нагрузки и поэтому почти всегда маскируются декоративными элементами (цветами, розетками и пр.). Этот прием характерен для стиля барокко. Но когда части изделия скрепляются скобами или заклепками, соединения не скрываются, а, наоборот, выделяются, чтобы подчеркнуть замысел художника, то соединительным элементам придают декоративную форму.
Скобы, или хомуты, для этого отковывают отдельно и в горячем состоянии надевают на те части, которые требуется скрепить. Остывая, они дают усадку, и соединение получается очень прочным.
Скобы можно делать полукруглыми, загибая их уже на скрепляемых деталях, которые перед этим нужно плотно зафиксировать в тисках или струбциной. Но при соединении внахлест скобу делают в одной из пересекающихся полос. В ней просекается отверстие, в которое вставляется пруток такого же сечения, что и продеваемая часть.
Когда подгонку формы заканчивают, то пруток убирают и на его место ставят требуемую деталь, обжимая место соединения клещами, губки которых раскалены до красного каления. Происходит сварка, после которой части композиции прочно скрепляются между собой.
Обработка кованых изделий
Окончательная обработка кованых изделий применяется не только для того, чтобы защитить их от коррозии, но и для придания им законченного вида художественного произведения.
Видов такой отделки множество, здесь приводятся только основные, которые используются большинством мастеров.
Практически любое кованое изделие можно украсить орнаментом, для которого понадобятся ручники, гладилки, пробойники, зубила, а также некоторые инструменты слесарей и чеканщиков. Орнамент можно делать как на холодной, так и на горячей заготовке. Орнамент, выполненный на холодной заготовке, получается плоским и поверхностным, а на горячей – глубоким и объемным.
Используя ручник, можно нанести огранку (специальные грани) на подготовленную поверхность, а с помощью кузнечного зубила получится штриховой орнамент. Для нанесения прямых линий используют зубило с прямолинейным лезвием. Для нанесения линий с более мягкими, нерезкими очертаниями надо взять зубило с затупленной режущей кромкой. Работая с зубилами, у которых разная кривизна лезвия, можно получить сложные орнаменты, состоящие из цветов, кружков и розеток.
Насечка
К заключительным видам ковки относится насечка рисунка, проводимая в горячем или холодном состоянии с помощью зубила. Этим способом можно наносить штрихи, насечки, решетки фона, узоры, надписи и т. п. Насекание производят на плоских поверхностях, которые на готовом изделии будут хорошо видны (не будут закрыты другими деталями, не попадут в тень и т. д.). Плоские изделия насекают на наковальне, полые и кольцеобразные – на оправках.
На отдельные элементы изделия можно наносить насечку уже во время ковки. Например, выковав лист, сделать на его поверхности различные прожилки с помощью зубила, а только потом изогнуть лист по своему желанию. Чтобы нанести насечки на объемное изделие, лучше использовать оправки.
Набивка
Набивка рельефа и фактуры также относится к отделочным операциям. Помимо цветов и розеток, можно украсить изделие точками и всеми видами углублений. Для этого понадобится пробойник со специально заточенной рабочей частью и некоторые другие инструменты. При нанесении на поверхность изделия углублений, нельзя забывать использовать подкладной инструмент. Им могут быть протяжки, притупленные зубила, гладилки и пробойники. С помощью гладилок, поставленных под определенным углом, можно получить углубления треугольной формы, с помощью протяжек – волнистую поверхность, с помощью пробойников с разным сечением рабочей части – углубления круглой, квадратной, конической формы, с помощью притупленного зубила – бороздки. Кроме вышеперечисленных инструментов можно использовать пуансоны, чеканы, молотки с бучарами.
Воронение
Воронение, пожалуй, самый распространенный способ обработки стали, прекрасно защищающий ее от коррозии и придающий изделиям красивый черный цвет.
Проще и доступнее всего осуществлять воронение следующим образом. Изделие быстро нагревается до температуры 600–650 °C (темный цвет заготовки) и погружается в машинное масло до неполного остывания. После просушивания вынутой поковки на поверхности образуется темная пленка магнитного оксида железа, хорошо предохраняющая металл от коррозии.
Вместо машинного можно использовать льняное масло, но тогда деталь следует смазать им перед нагреванием. Так как масло легко воспламеняется, перед загрузкой в горн поковку необходимо тщательно просушить.
Если проводить нагрев нежелательно, изделие обрабатывают в растворе из 650 г едкого натра, 200 г натриевой селитры и 200 г перекиси марганца на 1 л воды. Его погружают в кипящий раствор на 1 час, затем просушивают и шкуркой удаляют лишний налет.
Травление
Травлением называют процесс обработки отдельных частей поверхности металлических изделий кислотами. В зависимости от того, какая часть изделия подвергается травлению – рисунок или фон, различают позитивное или негативное травление. При позитивном на обезжиренную поверхность наносят антикислотное покрытие. Оно готовится следующим образом: в скипидаре до состояния смолы растворяют 40 г парафина, 20 г битума и 20 г смолы.
Покрытие наносят на изделие ровным слоем, затем иглой проводят по контуру рисунка. В зависимости от выбранного способа травления либо удаляют части фона, либо тщательно ретушируют линии. Чтобы кислота не слишком сильно разъела изделие, перед погружением на него наносят тонкий слой воска.
Травление проводится разбавленной кислотой, для сталей различных марок используется серная, для цветных металлов – азотная. Ее разводят до 10–15 %-ного раствора, добавляя постепенно воду. Признаком нормального соотношения является прекращение пузырения по всему объему жидкости. Чаще всего изделие опускают в кислоту целиком, но можно покрывать его раствором с помощью ворсистой кисти.
Окраска
Железо не так хорошо, как цветные металлы, окрашивается химическим способом. Поэтому для придания стали с высоким содержанием углерода того или иного цвета рекомендуется сначала нанести на поверхность слой меди или латуни. Делается это обычно с помощью гальванической установки.
Тем не менее в синий цвет можно окрасить сталь, опустив в краситель, приготовленный следующим образом: 140 г гипосульфита натрия на 1 л воды смешивают с раствором 35 г уксусного свинца с таким же количеством воды. Поковку опускают в кипящий раствор и держат там до тех пор, пока она не окрасится в синий цвет.
Придать заготовке коричневый цвет с темным оттенком поможет сурьмяное масло. Его наносят на тряпочку и протирают поверхность, после чего она покрывается тонким налетом ржавчины. На следующий день операцию повторяют и продолжают ее, пока изделие не приобретет нужный цвет. Если по каким-то причинам этот способ не подходит, поступают следующим образом. Деталь на несколько секунд опускают в кипящий 10 %-ный раствор двухромовокислого натрия, после чего равномерно прогревают над открытым огнем.
После окончания окрашивания изделие необходимо протереть льняным маслом и высушить. Для получения яркого цвета перед этим изделие немного нагревают.
Яркий черный цвет получается после воронения. Но если поковка предназначена для оформления интерьера, ее специально чернят.
Древнерусским мастерам был известен способ окраски поверхности в черный цвет с помощью льняного масла. Но гораздо проще погрузить изделие в раствор гидрата или нитрита натрия, нагретый до температуры 130–140 °C, и подержать его там 5–10 минут. Если поверхность была хорошо очищена, то цвет получится ярким и равномерным.
Можно поступить следующим образом. Растворить в 100 мл 30 %-ного раствора фосфорной кислоты 18 г цинкового порошка, затем разбавить смесь 5 л воды, нагреть до кипения и погрузить в нее изделие на 2–3 часа. После завершения обработки поковку промывают под проточной водой и высушивают.
Другие виды обработки
Поверхность любого изделия, особенно если оно выполнялось с тем расчетом, чтобы радовать глаз, можно дополнительно обработать. В зависимости от характера предмета на его поверхность можно нанести рисунок, орнамент или просто отшлифовать.
Нанесение орнамента
Орнамент наносится на поверхность с помощью зубил, пробойников, особым образом закаленных чеканов и т. д. На холодном изделии он получается неглубоким, а на горячем линии значительно четче.
Комбинированием секачей с прямыми и закругленными лезвиями можно получить рисунок любой сложности. Сначала наносятся самые тонкие линии, затем глубокие. Мягкие линии получают притупленными зубилами.
Часто на еще не остывшем изделии выбивают точки и углубления различной формы. Для этого используют пробойники всевозможного диаметра, с фасонной рабочей поверхностью. Применяют также и обычные кузнечные инструменты, например, с помощью гладилки, поставленной под углом к обрабатываемой поверхности, можно получить треугольные углубления. Если в кузнице есть бучарда – молоток с коническими или круглыми выступами на рабочей поверхности, то можно обработать изделие им.
Кроме вышеперечисленных инструментов, для набивки орнамента применяются пуансоны. На их поверхности уже выгравирован определенный элемент, и все, что остается сделать, – это установить инструмент в нужном месте и ручником проковать орнамент.
Крацевание
Так называется способ обработки поверхности изделия с помощью металлических щеток. В зависимости от твердости используемой стали ворс для щеток делают из стальной или латунной проволоки диаметром 0,1–0,2 мм.
Поверхность проглаживают круговыми движениями, силой надавливания на щетку регулируют глубину наносимых линий. Процесс можно облегчить, сделав щетку круглой формы, с металлическим стержнем в середине. Его вставляют в патрон электродрели и обрабатывают изделие. Для того чтобы сделать линии более заметными, ворс перед началом крацевания смачивают в пиве или 3 %-ном растворе серного поташа.
Шлифовка и полировка
Шлифовку кованых изделий осуществляют с применением абразивных порошков. Для сталей с низким содержанием углерода используются такие материалы, как корунд или наждак. Шкуркой обрабатывать металлические поверхности слишком долго, поэтому большинство кузнецов пользуются специальными шкурками или войлочными кругами. Последние можно сделать самому. Из войлока необходимо вырезать несколько кругов равного диаметра, склеить их между собой так, чтобы толщина валика была около 1 см. Через центр продеть опорный стержень.
Нижнюю поверхность кругов надо смазать столярным клеем и наклеить выбранный абразивный материал. После этого можно приступать к шлифовке.
Полировка поверхности – более тонкий процесс, выполняемый с помощью кусочков кожи, сукна или плотной ткани с нанесенным абразивом по уже отшлифованной поверхности.
В качестве полировочных материалов используют порошки корунда, карбида кремния, синтетический алмазный порошок и т. д. Их смешивают с вязким раствором, которым покрывают участок изделия, а затем растирают по всей поверхности.
Чтобы отполировать поверхность внутри углублений поковки, делаются фетровые валики шарообразной формы, которыми работают с помощью дрели.
Литье
Литейное дело – одно из самых древних ремесел, оно известно на Руси уже несколько тысячелетий. В те далекие времена, когда литейное производство только-только появилось, литейщики использовали глиняные формы, причем модель делали из воска.
Пик развития литейного ремесла в Древней Руси приходится на XII–XIII века. В это время появляются уже двусторонние формы с разветвленными литниковыми системами, с помощью которых изготавливали самые разнообразные изделия: посуду, металлические украшения, наконечники для стрел и копий. И уже к XIV веку на Руси овладели техникой литья бронзовых пушек – это явилось немаловажным событием в истории молодого государства.
В XV веке для литья труб и гирь стали использовать чугун, а в XVI веке, наряду с бронзой и чугуном, применять также и смесь из сырого кварцевого песка, глины и овечьей шерсти.
С течением времени постепенно развивалось и литейное производство. Позднее появилась сталь. В связи с тем что потребности населения в изделиях из металла возрастали, литейное производство значительно совершенствовалось, усложнялось. В это время появились даже научные труды по технологии отлива из металла.
В России родоначальниками науки о литье традиционно принято считать ученых-металлургов: Аносова П. П., Чернова Д. К. и Лаврова А. С.
Оборудование рабочего местаОборудовать литейную мастерскую в домашних условиях крайне сложно. Как и кузницу, правила безопасности запрещают делать ее в квартире многоэтажного дома. Получение отливок из бронзы или латуни требует довольно высоких температур и подготовительных работ, для которых нужна большая площадь.
Еще одна причина, по которой не стоит проводить плавку металлов дома, – необходимость хранения большого количества горючих материалов, так как обычная плавильная печь, работающая на угле, потребляет его столько, что в случае пожара потушить дом будет крайне сложно.
Многие литейщики-любители используют в качестве топлива пропан, хранящийся в баллонах. Он не выделяет побочных продуктов горения, прост в эксплуатации и обладает массой других достоинств. Но этот газ крайне взрывоопасен, поэтому хранить баллоны лучше в сарае, а рабочее место устроить так, чтобы они располагались в другом помещении, подальше от открытого огня.
Лучше всего устроить литейную мастерскую в отдельном строении на даче или в деревне. При этом подготовительные работы, то есть формовку небольших моделей, вполне можно производить дома, но при этом надо соблюдать технику безопасности.
Для формовки, собственно литья и хранения топлива необходимо предусмотреть отдельные помещения. Они должны хорошо сообщаться между собой, что облегчает переноску тяжелых форм от одного участка к другому.
Самое просторное помещение отводится для литейной. В центре, подальше от стен, ставится печь. Пол вокруг делается земляным или выкладывается кирпичом.
В стороне ставится невысокий верстак для литейной формы. Уровень расположения литейной чаши не должен быть выше уровня верхней части печи, чтобы при работе ковш не приходилось поднимать.
Одежду литейщика следует делать из прочного материала, хорошо защищающего от тепла. Высокие ботинки на толстой подошве предохраняют ноги во время работы около печи. На руках обязательно должны быть перчатки, а при заливке – рукавицы из двухслойного брезента.
Комната для формовки должна иметь не только хорошее дневное, но и искусственное освещение. Литниковые системы собираются на широком верстаке, за которым должно быть одинаково удобно и сидеть, и стоять. Большие формы заполняются и собираются прямо на полу.
Стол должен иметь жесткую крышку и прочно стоять на ножках, поскольку масса некоторых заполненных форм довольно велика. Вокруг него располагают ящики с инструментами, необходимыми при формовке, и съемными частями литниковых форм.
Многоразовые опоки средних размеров, очищенные от остатков формовочного материала, хранятся в специальном шкафу. Песок и глину держат в больших стационарных ящиках.
Обычно начинающему литейщику доступны два легкоплавких материала – свинец и олово. Пользоваться первым не рекомендуется, несмотря на всю простоту его обработки в домашних условиях. Во-первых, свинец ядовит и дышать его парами опасно. Во-вторых, от неосторожных опытов могут пострадать близкие и соседи.
Оборудование для микролитья
Другой металл – олово издавна использовался для отливки небольших предметов быта, а также игрушек. Помните сказку Г. Х. Андерсена «Стойкий оловянный солдатик»? Чтобы сделать фигурку из олова, понадобится большой опыт формовки, но сам металл крайне прост в обращении. Рабочее место оборудовать совсем несложно. Прежде всего необходим просторный стол, за которым можно было бы стоя собирать литейные формы и производить засыпку формовочной смеси. Место должно быть хорошо освещено, поскольку формы для микролитья (именно так называется отливка небольших изделий) по сложности не отличаются от обычных, хотя размеры их гораздо меньше.
Правообладателям!
Это произведение, предположительно, находится в статусе 'public domain'. Если это не так и размещение материала нарушает чьи-либо права, то сообщите нам об этом.