Текст книги "Работы по металлу"
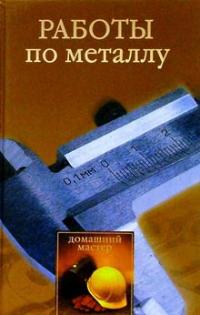
Автор книги: Наталья Коршевер
Жанр: Техническая литература, Наука и Образование
сообщить о неприемлемом содержимом
Текущая страница: 20 (всего у книги 20 страниц)
Ручная формовка – процесс достаточно трудоемкий, однако терпение и желание создать необычное изделие из металла могут помочь овладеть им. В технологии ручной формовки особенное внимание следует уделять двум основным процессам: наполнению формы и уплотнению формовочной смеси. Недостаточное наполнение и уплотнение смеси часто приводят к различным дефектам на отливках.
Брак на изделиях может появиться в результате чрезмерного наполнения формы смесью, так как при этом нарушается выход газов и воздуха из полости. Наполнять формы и уплотнять смесь нужно равномерно по всему объему так, чтобы при этом не образовывались впадины и излишне плотные места в формовке.
Подготовка исходных формовочных материалов
Формовочные материалы порой бывают в состоянии, непригодном для приготовления смесей. Поэтому их подвергают предварительной обработке – сушке, размолу, просеиванию.
Сушку производят различными способами. Когда расход смесей небольшой, сушат в простых печах, на противнях. При большом потреблении материалов – в специальных барабанных печах.
Некоторые пески поступают из карьеров в виде спрессованных пластин, а глины – в виде комков. Поэтому их после сушки подвергают размолу в бегунах.
Просеивание производят после размола на вращающихся или качающихся ситах.
Подготовка отработанной смеси включает в себя дробление, магнитную сепарацию и регенерацию.
Приготовление и испытание формовочных смесей
Нижеперечисленные операции входят в процесс приготовления формовочных смесей: составление смеси, перемешивание сухого состава, увлажнение, перемешивание влажного песка, вылеживание, разрыхление. Перед формовкой необходимо проверить качество формовочной смеси. Проверяют не все свойства, а только самые важные: газопроницаемость, прочность, количество глины, влажность и зерновой состав песка.
Изготовление моделей
Изготовить модели для отлива в домашних условиях не так сложно, как может показаться на первый взгляд.
Небольшие по размеру неразъемные модели, состоящие из нескольких склеенных между собой досок, необходимо предварительно обработать на токарном или фрезерном станке.
Модели более крупных размеров собирают из подготовленных продольных или поперечных рам и затем соединяют в определенном порядке для получения необходимой формы. После этого деревянный каркас обшивают досками или листами фанеры толщиной в 30 мм, поверхность которых затем зачищают. И лишь потом присоединяют мелкие детали модели (ребра, бобышки, приливы), а также вставляют и закрепляют подъемы.
Разъемные модели соединяют с помощью деревянных или металлических шипов-дюбелей, которые закрепляют без использования клея, так как они подвержены быстрому износу. Металлические дюбели при этом крепят к модели шурупами, а деревянные удерживаются вообще без какого бы то ни было крепления за счет силы трения.
Отъемные детали прикрепляют к модели с помощью металлических шпилек или шипов типа «ласточкин хвост». При этом шпильки используют для моделей, предназначенных для выпуска небольшой партии изделий, а деревянные или металлические шипы «ласточкин хвост» применяют для скрепления частей моделей, по которым изготавливают большое количество форм для отлива.
Галтели в деревянных моделях можно установить различными способами: с помощью клея (рис. 170, а), врезать в модель (рис. 170, б) или изготовить непосредственно в ней (рис. 170, в). Такую деталь для формовочной модели можно изготовить и из замазки (рис. 170, г).

Рис. 170. Установка галтелей: а – вклеивание; б – врезание; в – цельная галтель; г – замазка.
Формовка
Первоначально необходимо на модельной плите расположить модель отливки и питателя. После этого установить нижнюю опоку так, чтобы ее приливы оказались внизу, после чего предварительно слегка присыпанную серебристым графитом модель посыпать просеянной облицовочной смесью. Затем опоку надо заполнить смесью из органических и неорганических материалов (о них говорилось выше).
После наполнения формы ее нужно хорошо утрамбовать сначала острой трамбовкой для уплотнения стенок, а потом с тупым бойком, чтобы утрамбовать поверхностные слои наполнительной смеси, излишки которой потом можно удалить с помощью деревянной линейки. Для того чтобы при отливе газы выходили наружу, в смеси длинной металлической иглой проделывают вентиляционные каналы, которые не должны касаться модели.
После завершения данных операций заполненную нижнюю полуформу необходимо перевернуть на 180° так, чтобы вентиляционные каналы оказались на дне будущей формы, а приливы, наоборот, вверху. Затем ее располагают на столе верстака и снимают контрольную мерку плотности смеси нижней полуформы с помощью твердомера.
После проверки того, что смесь достаточно уплотнена, ее поверхность необходимо выровнять гладилкой, а затем закрепить знак модели. Поверхность нижней полуформы надо присыпать сухим кварцевым разделительным песком, а затем удалить все излишки материала, верхнюю же полуформу установить на нижнюю и модель вновь присыпать графитом.
Затем на модели питателя (расположенном в нижней опоке) закрепляют модели шлакоуловителя и стояка, после чего их засыпают слоем облицовочной смеси, которую вручную уплотняют вокруг стояка. В опоку засыпают наполнительную смесь, которую хорошо уминают плоской трамбовкой, после чего ее поверхность выравнивают линейкой, удаляя излишки.
Для предотвращения скопления воздуха и газов при нагреве в смеси верхней полуформы (так же, как и нижней) необходимо сделать вентиляционные каналы.
После завершения этого процесса нужно изготовить литниковую воронку и удалить стояк. Перед тем как извлечь шлакоуловитель и знак, необходимо разделить полуформы и смести щеткой разделительный песок. После формовки верхней опоки нужно измерить плотность наполнительной смеси в плоскости разъема и разровнять ее поверхность гладилкой.
Затем в модели закрепляют подъем. Для этого ее расталкивают, ударяя молотком по подъему, и только после этого осторожно (в строго вертикальном направлении) вынимают модель и питатели. Для того чтобы облегчить ее извлечение, смесь нужно предварительно увлажнить с помощью пеньковой кисти.
После извлечения модели форму осматривают, исправляют дефекты. Для этого поврежденные места нужно смочить глиной или жидким стеклом и исправить формовочным инструментом. При этом лучше всего пользоваться специальными шаблонами и деревянными линейками, учитывая то, что стенки форм и их поверхность должны быть ровными и гладкими, а платики и бобышки – иметь четкие линии. Форму, брак которой настолько велик, что она имеет множество слабо или, наоборот, чрезмерно уплотненных мест и различных повреждений, использовать для отливки нельзя. Такие формы разрушают, выбивая и удаляя из них формовочную смесь.
В смесях качественных форм закрепляют стержень, после чего опоки спаривают, соединяя штырями, и устанавливают на формовочной смеси, придавив сверху грузом.
Подготовка форм к заливке металла
После того как формы высохнут, их необходимо отделать и собрать разъемные детали.
Перед отливом рабочую поверхность формы следует закрепить шпильками длиной до 10 см. Прежде всего нужно закрепить наиболее слабые и подверженные различным повреждениям места формы: бобышки, болваны, платики, ребра, углы и боковые кромки, а также исправленные участки.
Для этого шпильки (или литейные гвозди) вдавливают в смесь, располагая их при этом на определенном расстоянии друг от друга: у питателей с интервалом в 25–35 мм, у поверхности 50–70 мм, нижнюю часть и вертикальные поверхности закрепляют шпильками, располагая их на расстоянии в 25–100 мм одна от другой, нижние и боковые выступы – на расстоянии 50–75 мм, верхние 25–40 мм. Перечисленные выше участки сырых форм рекомендуют закреплять несколько чаще, увеличивая частоту расположения шпилек в два раза.
Готовая к заливке жидким металлом форма должна иметь хорошо подготовленную литниковую систему с прочными, ровными и гладкими стенками.
Формы можно красить как перед просушкой, так и после нее. При окрашивании сырой формы ее необходимо обработать: хорошо выровнять полость и замазать подтеки и заливы краски с помощью влажной пеньковой кисти.
Сборка деталей формы
Для литья используют только качественные (неповрежденные, хорошо просушенные, с ровной и гладкой поверхностью) формы.
Стержни маленьких размеров закрепляют в нижней полуформе вручную, предварительно тщательно выверив их размер: они должны плотно входить в углубления в форме, причем их вентиляционные каналы должны совпадать с теми же каналами в форме. Для лучшей фиксации необходимо использовать жеребейки, которые закрепляют стержни в нужном месте и не дают им всплыть при заливке сплавом.
Для того чтобы жидкий металл при заливке не попадал в вентиляционные каналы и зазоры между стержнем и формой, на знаковой части рекомендуют сделать выступы (обжимные пояски), а ее зазоры заполнить глиной, паклей, асбестом или песком.
При сборке частей форм необходимо постоянно контролировать их размеры. Производить это можно с помощью линейки, угольника, кронциркуля или нутромера. Изогнутые поверхности можно контролировать, установив конусы или небольшие валики из глины. Однако этот процесс занимает достаточно много времени, и потому измерения подобных поверхностей удобнее производить с помощью шаблонов и кондукторов.
После установления и закрепления стержня его подъем необходимо заделать формовочной смесью. Участок должен быть тщательно отделан: прошпилен, хорошо просушен и выкрашен.
Для того чтобы предотвратить утечку сплава по линии разъема сырых полуформ, необходимо по периметру литниковой системы и полости формы, на расстоянии 40–100 мм от нее, произвести подрезку слоя смеси с помощью гладилки. В просушенных формах для этого прокладывают графитоасбестовый шнур, отступая от полости на 40–60 мм.
После сборки, перед применением, формы нужно очистить щеткой от пыли, остатков смеси и песка. И только затем надо устанавливать литниковые чаши (или воронки), сделанные из стержневой смеси или глины.
В полностью подготовленную форму можно заливать сплавы.
Техника литьяПриготовление расплавов
Чтобы приготовить металл для заливки в форму, существуют плавильные печи, в которых он расплавляется. Есть несколько разновидностей печей – дуговые и индукционные электрические, пламенные и тигельные, вагранки, электрические печи сопротивления. Они должны обеспечивать низкий расход топлива и хорошую производительность, небольшой угар расплава и минимальное насыщение его ненужными примесями, выход расплава заданной температуры, жидкотекучести и химического состава. Совсем немного поясним вопрос по поводу этих печей.
Если для литья необходимо иметь значительное количество металла с постоянным химическим составом, то более всего подойдет для этого вагранка. Это печь непрерывного действия, у нее высокая производительность. Она представляет собой шахтную плавильную печь, которая внутри выложена огнеупорным кирпичом.
Снаружи вагранка облицована металлическим кожухом, сварным или клепаным.
При всех достоинствах этой печи у нее имеется очень существенный недостаток – в процессе расплава происходит увеличение содержания серы (она переходит в чугун).
Пламенная печь используется при изготовлении цветных сплавов и плавке чугуна. Она представляет собой камеру, кожух которой собран из литых чугунных плит. Изнутри ее облицовывают огнеупорным кирпичом.
Такие печи могут быть стационарными и поворотными. Они имеют большое преимущество, заключающееся в возможности получения чугуна с меньшим содержанием вредных примесей. Но по сравнению с вагранками пламенные печи менее удобны в работе и неэкономичны.
По типу энергии, применяемой для плавки, тигельные печи (рис. 171) подразделяются на электрические и коксовые.

Рис. 171. Стационарная тигельная печь.
Они могут быть поворотными и стационарными и использоваться для плавки бронзы и латуни. Преимущество плавки в таких печах – получение расплава с малым содержанием серы. Недостаток – большой расход кокса и малая производительность.
Электрические плавильные печи делятся на дуговые, индукционные и печи сопротивления. Чаще всего их применяют для плавки бронзы и латуни, и редко – чугуна. Дуговая электрическая печь – это стальной сварной барабан с графитовыми электродами, между которыми возникает дуга, являющаяся источником теплоты.
Индукционные печи относятся к агрегатам непрерывного действия, они очень экономичны и производительны. Достоинствами этих печей являются небольшой угар элементов, постоянный химический состав металла и отсутствие вредных выделений.
Заливка форм
Для заливки расплавленного металла в формы имеется множество ковшей самых разных конфигураций и размеров.
Они бывают монорельсовые, крановые и ручные. Рассмотрим каждый тип ковша в отдельности.
При изготовлении малых форм пользуются ручными ковшами-ложками. Их переносят специальными носилками-рогачами, они имеют вместимость 16–40 кг и изготавливаются из листовой стали. Изнутри все ковши-ложки необходимо обмазывать огнеупорной глиной и просушивать.
Заливку крупных форм производят барабанными ковшами, которые подвозят на специальных вагонетках и наклоняют с помощью поворотного механизма. Такие ковши имеют емкость 400–800 кг.
В технологическом процессе получения отливки самая короткая операция – заливка литейных форм. Вместе с тем она значительно влияет на качество отливки. Шлаковые и усадочные раковины, недоливы, спаи, пригар – это причины брака при заливке, встречающиеся достаточно часто. Поэтому имеет смысл остановиться на способах заливки форм.
В зависимости от места расположения форм, от требований, предъявляемых к отливке, существует ряд способов заливки форм: на плацу, на рольганге, на конвейере. В сложных случаях применяют специальные способы – заливку в поворотные и наклонные формы, в среде инертных газов и под вакуумом, в автоклаве.
Выбивка
После охлаждения отливки, литейную форму разрушают – производится выбивка. В зависимости от объема производства и сложности отливки выбивают из форм вручную или механизировано. С помощью молотков и клещей выбивают вручную. При механизированном способе применяют вибрационные скобы, коромысла, механические и инерционные решетки, а также пневматические рубильные молотки и гидравлические установки. Познакомимся немного с этими инструментами.
Вибрационная скоба – это приводимый в действие сжатым воздухом переносной вибрационный механизм, предназначенный для выбивки из опок формовочной смеси и отливок.
Удобное подвесное устройство, которое создает вибрацию опоки, называется вибрационным коромыслом, оно обеспечивает равномерное вытряхивание смеси и ускоряет процесс выбивки.
Принцип работы механических выбивных решеток в том, что они после приведения в колебательное движение подбрасывают опоку, и она, ударяясь о решетку, разбивается. Стержни из отливок удаляют пневматическими рубильными молотками, вибрационными машинами и гидравлическими установками, из которых самыми совершенными являются последние, так как они работают бесшумно и не создают запыленности, а к недостаткам относятся высокая стоимость и необходимость сушки отливки.
Отливка после выбивки из формы имеет на поверхности выпоры, литники и прибыли, могут образоваться и заливы. Если они имеют небольшую толщину, с помощью молотка и зубила их удаляют вручную. У скульптурных и архитектурных форм – пневматическими зубилами. У отливок из цветных сплавов дефекты удаляют ножовками или на специальных станках с ленточными пилами. Этот процесс удаления литников, выпоров и т. д. называется обрубкой.
Очистка
После обрубки отливки очищают от пригоревшей к их поверхности формовочной смеси. Делают это вручную, в барабанах, дробеструйных аппаратах, в установках химической и электрохимической очистки, с помощью механических щеток. Изделия, имеющие сложную поверхность и тонкие стенки, очищают вручную на специальных столах с металлическими решетками и пылеотсасывающими трубами. Ажурные тарелки, кронштейны и др. очищают круглыми механическими проволочными щетками.
Очистка в барабанах
В них очищают толстостенные отливки, не имеющие на поверхности тонких украшений. Их закладывают в барабан (рис. 172) вместе с чугунными звездочками, которые при вращении барабана сдирают формовочную смесь, пригоревшую к поверхности отливки.

Рис. 172. Очистной барабан.
В барабанах можно очищать и тонкостенные отливки, только при этом необходимо проложить их деревянными прокладками, чтобы они не перекатывались.
Дробеструйная очистка отливок производится сжатым воздухом с добавлением чугунной дроби. Через слой дроби проходит воздух, увлекает ее за собой, выбрасывает на поверхность отливки и очищает ее.
Отливки, полученные литьем, очищаются выщелачиванием, или химической очисткой, в сетчатом барабане, помещенном в ванну с горячим раствором каустика.
Электрохимическая очистка отливок производится в специальных установках. Принцип работы их основан на химических реакциях, которые проходят в расплаве гидроокиси калия или натрия, при пропускании через них электрического тока напряжением 5–10 В. Электрохимическая очистка дает высокое качество поверхности отливок.
Правообладателям!
Это произведение, предположительно, находится в статусе 'public domain'. Если это не так и размещение материала нарушает чьи-либо права, то сообщите нам об этом.