Текст книги "Нанотехнологии. Правда и вымысел"
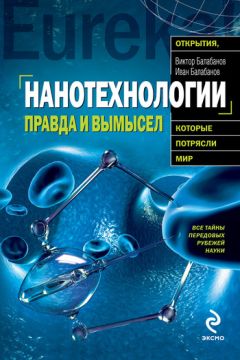
Автор книги: Виктор Балабанов
Жанр: Документальная литература, Публицистика
сообщить о неприемлемом содержимом
Текущая страница: 7 (всего у книги 23 страниц) [доступный отрывок для чтения: 8 страниц]
Создание искусственных наноматериалов
Нанотехнологии – это технологии XXI века. И страна, которая будет их внедрять, станет лидером XXI века…
А. Д. Жуков, вице-премьер Правительства Российской Федерации
Для исследования объектов и процессов нанотехнологий, создания наносистем и развития наноиндустрии необходимо было разработать эффективные способы получения наноструктур и наноматериалов в достаточном (коммерческом или промышленном) количестве.
Исходным сырьем для наноматериалов являются в первую очередь, металлы и их оксиды (например, порошки оксида титана, оксида кобальта и др.), монтмориллонит, природные и синтетические полимеры. Кроме того, в России имеются ценные отходы производств, переработка которых позволяет получать компоненты, используемые в нанотехнологиях для выпуска продукции с достаточно высокими эксплуатационными свойствами. В частности, при синтезе нанополимерных композиционных материалов с рекордными физико-химическими и эксплуатационными характеристиками. Наносистемы на основе природных полимеров могут служить исключительно эффективными носителями биологически активных веществ, сорбентов и других материалов, которые широко используются в медицине, фармацевтике, при решении экологических проблем, связанных с утилизацией токсичных компонентов почвы, воды, атмосферы, в агропромышленном комплексе.
Наибольшее распространение в настоящее время получили нанодисперсные (ультрадисперсные) порошковые материалы.
Для их производства применяются следующие технологии: восстановление, электролитический метод, разновидности золь-гель технологии и плазмохимический метод.
1. Получение ультрадисперсных порошковых материалов восстановлением – один из самых дешевых методов, широко используемых для производства высокочистых металлических порошков.
2. При электролитическом методе применяется электролиз водных растворов, дающий порошки Fe, Cu, Ni, а также расплавов солей Ti, Zr, Nb, Ta, Fe, U, что, естественно, повышает себестоимость получаемой конечной продукции. Данная технология обеспечивает получение частиц с размерами в несколько десятков нанометров, имеющих дендритную форму.
3. При синтезе нанопорошков методом золь-гель технологии в предварительно разогретую смесь первичного реагента с необходимыми добавками быстро добавляется второй реагент. В процессе химической реакции образуется пересыщенный раствор заданного соединения, стремительно проходящего нуклеацию (в данном случае – начальная стадия фазового перехода от жидкого агрегатного состояния вещества к твердому) и вступающего в стадию роста кристаллов. Создание условий, при которых продолжительность нуклеации значительно меньше стадии роста, позволяет получать кристаллы с достаточно стабильными нанометрическими размерами.
4. Разновидность данного метода заключается в том, что в начале готовится «холодная» смесь реагентов, в которой скорость образования целевого вещества незначительна. При нагревании приготовленного раствора до необходимых температур образуется заданный продукт с концентрацией, достаточной для нуклеации. После быстрой и интенсивной нуклеации концентрация падает, и дальше происходит только рост образовавшихся частиц. В период роста кристаллов поддерживается температура, при которой процесс образования целевого вещества медленнее процесса его кристаллизации.
Достоинство обеих разновидностей золь-метода – возможность управлять размером, формой и степенью кристалличности наночастиц, варьируя комбинацию температуры и соотношения концентраций исходных реагентов и стабилизатора. Осажденные наночастицы отделяют от реагента в центрифугах. Золь-метод обеспечивает возможность формирования достаточно монодисперсных наночастиц различных полупроводников и металлов. Как мы видим, именно золь-методами получают радиоактивные материалы, при этом особое место отводится качеству и производительности задействованных центрифуг.
5. Наиболее рационально получать нанодисперсные порошки тугоплавких металлов (W, Mo, Ni) и их соединений (карбидов, нитридов и др.) плазмохимическим методом, представляющим собой восстановление металлов из их соединений под действием восстанавливающих газов. Электрической дугой высокой интенсивности в плазмотроне поддерживается плазма с температурой до 10 000 °C. При такой температуре в плазме, через которую пропускают газообразный восстановитель (водород или углеводороды и конвертированный природный газ), исходный материал расплавляется, а затем конденсируется в твердую дисперсную фазу.
Для получения фуллеренов оптимальным материалом является графит, поскольку он сам изначально имеет много общего со структурой фуллеренов. Однако в настоящее время ведутся интенсивные поиски и других способов синтеза, в которых исходным сырьем служат, например, смолистые остатки пиролиза углеродсодержащих материалов, нафталина и ряда других материалов.
В таблице 6 представлены наиболее распространенные способы получения наноматериалов.
Таблица 6. Основные способы получения наноматериалов


Известны работы, в которых электрическую дугу между электродами пропускают в среде растворителя – толуола и бензола. При этом, как показывает последующий масс-спектрометрический анализ, растворитель заполняется кластерами углерода с числом атомов, меняющимся от 4 до 76.
Газофазный метод (при 4000 °C и выше), обычно используемый для получения фуллерена С60СНТ, годится только для «гостевых» молекул, которые термически стабильны и могут подвергаться сублимации или испарению.
Наиболее эффективный способ получения фуллеренов основан на термическом разложении графита. Используется как электролитический нагрев графитового электрода, так и лазерное облучение поверхности графита. На рис. 24 показана простейшая схема установки для получения фуллеренов, предложенная В. Кречмером.

Рис. 24. Простейшая схема установки для получения фуллеренов: 1 – графитовые электроды; 2 – охлаждаемые медные шины; 3 – медный корпус; 4 – упругие пластины (пружины)
Распыление графита осуществляется при пропускании через его электроды 1, расположенные на охлаждаемых шинах 2 тока с частотой 60 Гц, силой тока от 100 до 200 А и напряжением 10–20 В. Регулируя натяжение пружин 4, можно добиться, чтобы основная часть подводимой мощности выделялась в дуге, а не в графитовом стержне. Камера заполняется гелием с давлением 100 торр (то же, что 1 мм рт. ст.). Эффективность испарения графита в установке может достигать 10 г/В. При этом поверхность медного корпуса 3, охлаждаемого водой, покрывается продуктом испарения графита, то есть графитовой сажей. Если получаемый порошок соскоблить и выдержать в течение нескольких часов в кипящем толуоле, получится темно-бурая жидкость. При выпаривании ее во вращающемся испарителе образуется мелкодисперсный порошок. Его масса составляет не более 10 % массы исходной графитовой сажи. В порошке содержится до 10 % фуллеренов С60 (90 %) и С70 (10 %). Этот метод получил название «фуллереновая дуга».
В описанном способе гелий играет роль буферного газа. Атомы гелия наиболее эффективно «гасят» колебательные движения возбужденных углеродных фрагментов, препятствующих их объединению в стабильные структуры. Кроме того, атомы гелия поглощают энергию, выделяющуюся при объединении углеродных фрагментов. Опыты показывают, что оптимальное давление гелия составляет 100 торр. При более высоком давлении агрегация фрагментов углерода затрудняется.
Для получения углеродных нанотрубок в настоящее время разработана более совершенная технология – синтез в плазме дугового разряда между графитовыми электродами в атмосфере гелия. Типовая схема электродуговой установки для изготовления наноматериалов, содержащих как нанотрубки и фуллерены, так и другие углеродные образования (например, конусы), показана на рис. 25.
При данном способе дуговой разряд возникает и поддерживается в камере с охлаждаемыми водой стенками при давлении буферного газа (гелия или аргона) порядка 500 торр. Обычно межэлектродное расстояние, устанавливаемое автоматически, составляет 1–2 мм. Для получения максимального количества нанотрубок ток дуги должен составлять 65–75 А, напряжение – 20–22 В, а температура электронной плазмы – порядка 4000 К. В этих условиях графитовый анод интенсивно испаряется, поставляя отдельные атомы или пары атомов углерода внутрь камеры. Из этих паров на катоде или на охлажденных водой стенках формируются различные углеродные наноструктуры.

Рис. 25. Схема установки для получения нанотрубок электродуговым методом
В большинстве случаев на катоде формируется твердый осадок макроскопического размера (в виде плоского пятна диаметром 11–12 мм и толщиной до 1,0–1,5 мм). Он состоит из наносвязок – нитей длиной 1–3 мкм и диаметром 20–60 нм, содержащих 100–150 однослойных или многослойных нанотрубок, уложенных в гексагональную упаковку. Такие связки напоминают связки круглых бревен, которые перевозят на лесовозах, или плоские плоты на лесосплаве. Нити наносвязок и отдельные нанотрубки часто образуют беспорядочную (а иногда и упорядоченную) сеть, похожую на паутину. Пространство этой паутины заполнено другими компонентами частиц углерода. Поскольку электронная плазма дуги неоднородна, не весь графит идет на строительство нанотрубок. Из большей части графитового анода образуются различные наночастицы или даже аморфный углерод, которые можно назвать общим словом «сажа».
Чтобы освободиться от других углеродных образований, осадок подвергают ультразвуковой обработке в какой-либо жидкости: этаноле, толуоле, дихлорэтане, бензоле или иных неполярных растворителях. В результате диспергирования можно получить как отдельные нанотрубки, так и нерасщепленные наносвязки (в основном, C60 и C70) с выходом до 10 % по массе. Для отделения сажи раствор после диспергирования заливают в центрифугу. То, что остается в жидкости, и есть раствор, содержащий нанотрубки или наносвязки, которые используют для исследований и практического применения.
Считается, что при образовании фуллеренов сначала формируются жидкие кластеры углерода, а затем эти кластеры кристаллизуются в фуллерены с испусканием свободных атомов и микрокластеров. Однако имеются и другие способы образования фуллеренов (например, посредством отжига углеродных кластеров). Эти способы, в отличие от различных моделей «сборки» фуллеренов, не предусматривают определенной структуры кластеров – предшественников фуллеренов.
При абляции (испарении) графита углеродные кластеры образуются в результате конгломерации атомов и микрокластеров, состоящих из нескольких атомов, что подтверждается расчетами. Образование кластеров в парах углерода может происходить как гомогенная нуклеация (образование зародышей жидкой фазы в метастабильном пересыщенном паре) или как спиноидальный распад (разделение на фазы вещества, находящегося в термодинамически нестабильном состоянии).
Другая возможность эффективного образования больших углеродных кластеров – конгломерация нескольких кластеров, состоящих из десятков атомов. Такой процесс происходит, например, при абляции высших оксидов углерода. Масс-спектр углеродных кластеров, полученных при абляции сажи, указывает на возможность сосуществования этих двух путей образования больших углеродных кластеров: масс-спектр имеет два максимума в распределении фуллеренов. Первый максимум (n = 154) соответствует конгломерации атомов и микрокластеров, второй (n = 450–500) – конгломерации кластеров, содержащих десятки атомов. Фуллерены образуются также из изначально больших кластеров, испаренных из материала, в состав которого входит углерод. Это происходит, например, при испарении мелкодисперсной графитовой фольги или вторичной лазерной абляции того же участка поверхности графита.
Если для получения чистого С60 в макроколичествах достаточно использовать электродуговой разрядник, то получение высших фуллеренов требует сложной и дорогостоящей процедуры экстракции, основанной на жидкостной хроматографии. Этот способ позволяет не только отделить, но и накопить редко встречающиеся фуллерены С76, С84, С90 и С94. Данные процессы идут параллельно получению С60, отделение которого позволяет обогатить смесь высшими фуллеренами.
Например, при использовании угольного конденсата, полученного путем термического испарения графитового электрода под действием электрической дуги, чистый С60 выделяется при обработке смесью гексана с толуолом в соотношении 95:5. Это приводит к вымыванию и последующему выделению чистого фуллерена С60. Увеличение в растворе содержания толуола до 50 % позволяет выделить чистый фуллерен С70 (рис. 26), а дальнейшее увеличение выделяет четыре желтоватые фракции. При повторном хроматографировании этих фракций на алюминиевой поверхности получаются достаточно чистые фуллерены С76, С84, С90 и С94. Обработка первой из указанных фракций, адсорбированной на алюминиевой поверхности, смесью гексана с толуолом в соотношении 95:5 приводит к полному растворению молекул С70 в смеси. Оставшийся желтоватый конденсат практически полностью состоит из молекул С76, что подтверждается данными жидкостного хроматографического анализа.
Существенные достижения в технологии получения нанотрубок связаны с использованием процесса каталитического разложения углеводородов. На рис. 27 изображена простейшая схема установки для такого процесса.

Рис. 26. Получение из фуллерена С60 фуллерена Суо (более темным цветом выделен добавленный пояс шестиугольников)
В качестве катализатора используется мелкодисперсный металлический порошок, который засыпают в керамический тигель 3, расположенный в кварцевой трубке 1. Последнюю помещают в нагревательное устройство (печь) 2, позволяющее поддерживать температуру в интервале от 700 до 1000 °C. Через кварцевую трубку продувают смесь газообразного углеводорода и буферного газа 4, например атомарного азота.

Рис. 27. Схема установки для получения нанотрубок методом химического осаждения: 1 – кварцевая труба; 2 – печь; 3 – тигель с катализатором; 4 – поток буферного газа
Типичной является смесь, в которой соотношение соединения C2H2 к N2 составляет 1:10. Процесс может продолжаться от нескольких минут до нескольких часов. На поверхности катализатора вырастают длинные углеродные нити, многослойные нанотрубки длиной до нескольких десятков микрометров с внутренним диаметром от 10 нм и внешним диаметром 100 нм. Имеются также металлические частицы, покрытые многослойной графитовой оболочкой. В этом процессе трудно получить однородные нанотрубки, поскольку каталитический порошок – слишком неоднородная среда.
В результате многочисленных исследований был найден оптимальный вариант: подложка для выращивания нанотрубок должна быть пористой, с высокой степенью однородности пор, заполненных частицами металлического катализатора. Если размеры частиц и пор совпадают, диаметр вырастающих трубок оказывается практически таким же. Если глубина пор и их поверхностная плотность достаточны, трубки вырастают строго перпендикулярно поверхности подложки и оказываются в высокой степени однородными.
Таким образом, проблема сводится к приготовлению подложки, поверхность которой была бы пронизана многочисленными глубокими однородными порами. На их дне должен располагаться металлический катализатор – «основа» для начальной стадии роста трубки. Катализаторами обычно выступают железо, никель и кобальт.
В России производством коммерческих партий наночастиц занимается ряд известных научно-исследовательских центров (табл. 7).
Таблица 7. Некоторые российские производители наноматериалов


Несмотря на очевидные успехи хроматографической технологии сепарации и очистки фуллеренов и нанотрубок, проблема получения высших фуллеренов в количествах, достаточных для полного и всестороннего исследования их свойств в конденсированном состоянии, еще далека от решения. Производительность лучших хроматографических установок не превышает нескольких миллиграммов в час, а этого явно недостаточно для обеспечения исследований (тем более для промышленного использования). Стоимость высших фуллеренов на мировом рынке составляет тысячи долларов за грамм, что делает их труднодоступными для многих научных лабораторий.
Создание дендримеров – один из примеров технологии «снизу вверх», когда объемные конструкции создаются из блоков посредством последовательной сборки, аналогично детскому конструктору. При этом размер и форму конечной конструкции можно очень точно задать при химическом синтезе. Дендримеры получают из мономеров, проводя последовательную конвергентную и дивергентную полимеризацию (в том числе методы пептидного синтеза), чем обеспечивается конфигурация ветвления.
Классическим строительным материалом для синтеза (создания) дендримеров являются полиамидоамин и лизиновая аминокислота. При этом имеется практическая возможность для задания и контроля размера и свойств поверхности. Регулирование и получаемая стабильность свойств дендримеров открывают перспективы их использования в качестве переносчиков лекарственных и косметических средств.
Для этого дендримеры формируют в присутствии необходимого медикаментозного вещества. В результате «полезные молекулы» образуют комплексы с поверхностью дендримера или, встраиваясь между полимерными цепями, заполняют многочисленные имеющиеся полости. Синтезированный таким способом дендример становится лекарственной нанокапсулой, способной к транспортировке данного препарата внутри живого организма. Заполнив полость дендримера веществом с радиоактивной или иной меткой, полученные нанокапсулы можно использовать в качестве диагностического средства при клинических исследованиях и лечении различных заболеваний.
Несколько слов стоит сказать о квантовых точках. Известны два основных способа их получения: коллоидный синтез, осуществляемый смешиванием предшественников в реакторе, и эпитаксия – ориентированное выращивание (копирование) кристаллов на поверхности подложки.
Коллоидный синтез может быть реализован при различных температурах и средах (в инертной атмосфере, в среде органических растворителей, в водном растворе и т. д.). Для повышения эффективности процесса часто используются металлоорганические предшественники или молекулярные кластеры, облегчающие «зародышеобразование» квантовых точек.
Наиболее часто применяют высокотемпературный химический синтез, осуществляемый в инертной атмосфере путем нагревания неорганометаллических предшественников, растворенных в высококипящих органических растворителях. Для этого на ядре (атомарной заготовке) из узкозонного полупроводника (например, CdSe) вначале осаждается оболочка из широкозонного полупроводника (например, ZnS), а затем на поверхности формируется защитная органическая оболочка из адсорбированных органических молекул.
В результате получаются нанокристаллы с поверхностью, защищенной слоем адсорбированных поверхностно-активных органических молекул. Этот метод (коллоидный синтез) обеспечивает получение стабильных по размеру и свойствам (высоким квантовым выходом флуоресценции) квантовых точек. Из-за наличия защитной гидрофобной органической оболочки коллоидные квантовые точки легко растворяются в неполярных растворителях (а при определенной ее модификации – в спиртах и воде).
Данная технология позволяет получать квантовые точки в субкилограммовых объемах, что делает ее привлекательной для их массового производства.
Метод эпитаксии – формирование наноструктур на поверхности другого материала (подложке) – требует уникального дорогостоящего оборудования. При этом получаемые квантовые точки связаны с подложкой и нуждаются в технологии отделения или использования вместе с подложкой. В связи с этим данный метод плохо реализуется на промышленном уровне.
По сообщениям сайта нанотехнологического сообщества России «Нанометр» (http://www.nanometer.ru), в Физико-техническом институте им. А. Ф. Иоффе в августе 2009 года был закончен монтаж уникального двухреакторного ростового комплекса молекулярно-пучковой эпитаксии STE3526 (рис. 28).
Двухреакторный комплекс STE3526 разработан и создан отечественным предприятием ЗАО «Научное и технологическое оборудование» специально для выращивания гибридных наногетероструктур с учетом последних достижений в области молекулярно-пучковой эпитаксии полупроводников в данных системах материалов.
Установка STE3526 предназначена для проведения фундаментальных и прикладных научных исследований, опытно-конструкторских работ и мелкосерийного экспериментального производства эпитаксиальных наноструктур на основе широкозонных материалов (типа Cd(Zn)Se/ZnMgSSe) с использованием предварительно выращенных в реакторе высококачественных буферных слоев GaAs. Данный комплекс обеспечивает ультра-чистый сверх-высоковакуумный (защита от неконтролируемого загрязнения ростового интерфейса на поверхности буферного слоя GaAs) транспорт подготовленной подложки в реактор для выращивания конечных гетероструктур.

Рис. 28. Двухреакторный ростовый комплекс молекулярно-пучковой эпитаксии STE3526
Следует отметить, что число фирм-производителей различных наноматериалов постоянно растет. При этом совершенствуется не только процесс получения и очистки наноматериалов, но и значительно повышается их качество, что позволяет находить новые сферы применения подобных материалов.
Правообладателям!
Данное произведение размещено по согласованию с ООО "ЛитРес" (20% исходного текста). Если размещение книги нарушает чьи-либо права, то сообщите об этом.Читателям!
Оплатили, но не знаете что делать дальше?