Текст книги "Современные работы по возведению стен и перегородок"
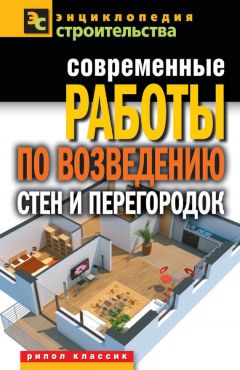
Автор книги: Галина Серикова
Жанр: Хобби и Ремесла, Дом и Семья
Возрастные ограничения: +12
сообщить о неприемлемом содержимом
Текущая страница: 7 (всего у книги 11 страниц)
Представляем несколько вариантов облегченной кладки стен.
Облегченная кирпично-бетонная кладка (рис. 70) – это конструкция из двух стенок толщиной в 1/2 кирпича, пространство между которыми заполняется легким бетоном.

Рис. 70. Выполнение облегченно-кирпичной кладки (размеры указаны в миллиметрах): а – при размещении тычковых рядов в одной плоскости; б – при расположении тычковых рядов вразбежку; 1 – тычковые ряды; 2 – ложковые ряды; 3 – легкий бетон
Чтобы связать стенки, выполняются тычковые ряды (диафрагмы), которые углубляются в бетон на 1/2 кирпича и выкладываются через каждые 3–5 ложковых рядов. Диафрагмы допускается располагать в одной плоскости или вразбежку, что определяется толщиной стены – 380–680 мм.
Продольные стены можно связывать и по-другому – отдельными кирпичами, которые при этом необходимо выкладывать в продольных стенках тычковыми рядами через каждые 2 ряда по высоте и не реже чем через 2 кирпича, размещенных ложками по длине продольных стенок.
Такой способ кладки используется при строительстве зданий высотой не более четырех этажей. При этом применяются легкие бетоны М10 и ниже, которые производятся на местных вяжущих (портландцемент не применяется).
В процессе кладки таких стен работы ведутся ярусами, высота которых зависит от расположения тычковых рядов. Если они находятся в одной плоскости, то кладка выполняется с тычкового ряда. Потом наружная верста поднимается на высоту двух ложковых рядов, внутренняя верста доводится до такой же высоты, зазор между ними заполняется легким бетоном. Далее кладется тычковый ряд, и кладка продолжается в указанной последовательности.
При размещении тычковых рядов вразбежку порядок работ иной, завершив который, кладка ведется в том же порядке:
1) наружная тычковая верста;
2) внутренняя ложковая верста;
3) 2 наружных и 2 внутренних ложковых ряда;
4) легкий бетон, которым заливается образовавшееся пространство;
5) наружная ложковая верста;
6) внутренняя ложковая верста, причем первый ряд тычковый, следующие два ложковые.
В порядке информирования
Чтобы кладка шла не только качественно, но и быстро, необходимо правильно организовать рабочее место (в длину оно занимает примерно 2,5 м). Обычно выделяются участки в виде свободной полосы, где работает мастер, и зоны, где размещаются строительные материалы. При выполнении кирпичной стены стопки кирпича или поддоны с ним удобнее расставлять по линии работ вперемешку с емкостями для раствора (оптимально, если расстояние между последними равно 3–3,5 м), запас кирпича должен быть таким, чтобы его хватило на 2–4 ч. При этом не следует перегружать рабочую зону, тем более когда работа будет вестись на подмостях или лесах.
Если кладка осуществляется без облицовки, то материалы (кирпич и раствор) расставляются в один ряд; при одновременно выполняющейся облицовке – в два ряда (в первом основной материал, во втором облицовочный).
Если кладку стен после закладки фундамента можно вести, стоя на земле, то, когда высота стены достигнет 120 см, это будет уже проблематично. Поэтому рабочее место необходимо переместить на подмости, представляющие собой настил на опорах, которые обязательно оснащаются приставными лестницами и ограждениями.
Леса – это система стоечных опор, к которым крепятся перемещающиеся (через 1 м) рабочие площадки. Леса устанавливаются, когда высота постройки достигает 5 м.
Облегченная колодцевая кладка (рис. 71) тоже представляет собой конструкцию из двух продольных стенок толщиной в 1/2 кирпича, расстояние между которыми составляет 140–340 мм. Для связи между ними с шагом 650–1200 мм по длине выполняются поперечные стенки толщиной в 1/2 кирпича.
Поперечные и продольные стенки связываются через каждый ряд по высоте. При этом образуются колодцы, которые можно заполнить различными материалами: легким бетоном, керамзитом, щебнем, шлаком и др. Если толщина стены не кратна 1/2 кирпича, то поперечные стенки выполняются с уширенными швами (рис. 72).


Рис. 71. Выполнение облегченной колодцевой кладки (размеры указаны в миллиметрах): а – фрагмент кладки; 1–4 – ряды кладки; 5 – поперечная стенка; 6 – раскладка кирпича на стене; 7 – заполненный колодец; 8 – растворная постель; б – кладка угла; 1 – продольные стенки; 2 – поперечные стенки; 3 – легкий бетон или засыпка; 4 – пробка
Чтобы не допустить оседания термоизолирующей засыпки, она производится слоями толщиной 100–150 мм, при этом каждый из них поливается раствором через каждые 100–500 мм и утрамбовывается. Кроме того, могут быть предусмотрены армированные прутками или скобами растворные диафрагмы (рис. 73). Жесткость контура кладки позволяет делать термоизолирующую засыпку после того, как подняты 5 рядов стенки, т. е. работы можно вести ярусами.

Рис. 72. Кладка поперечной стенки с уширенными швами (размеры указаны в миллиметрах)
Кирпичную кладку отличает значительная тепловая инерционность. Это означает, что стена из кирпича требует достаточного времени для прогревания, но и остывает она так же медленно. Если говорить о доме для постоянного проживания, то это качество кирпича можно расценивать как положительное, поскольку внутренние помещения, как правило, не испытывают серьезных температурных колебаний. Что касается домов временного проживания – в них эту особенность кирпича скорее можно отнести к негативным. Когда хозяева отсутствуют, температура стен настолько снижается, что для их прогревания необходимо довольно много времени и энергии (топлива). Именно для таких случаев (хотя и не только, так как подобные конструкции используются и при постройке жилых домов), помогающих смягчить это отрицательное явление, стены возводятся в виде многослойных конструкций, структуру которых образуют слои, разные по теплопроводности и тепловой инерционности.

Рис. 73. Кладка с растворными диафрагмами, армированными прутками (размеры указаны в миллиметрах): 1 – продольная стенка; 2 – утеплитель; 3 – армированная диафрагма
Система, в которой кирпич играет роль облицовки, называется многослойной. Она представлена двумя разновидностями. В первой облицовка из кирпича представляет собой самонесущий слой, который не предназначен для восприятия нагрузки, оказываемой перекрытиями и кровлей (рис. 74).

Рис. 74. Стена в виде многослойной конструкции: 1 – кирпичная облицовка; 2 – вентиляционный зазор; 3 – ветрозащита; 4 – слой теплоизоляции; 5 – несущая стена
Основная нагрузка приходится на несущую стену, которая традиционно возводится из полнотелого кирпича, блоков, керамзитобетона и пр. На нее монтируется слой теплоизоляции, после которой следует облицовочный слой.
Для прочности слои скрепляются гибкими Z-образными связями из нержавеющей или оцинкованной стали. Кроме того, несущая и облицовочная стены на уровне перекрытий объединяются железобетонным поясом.
При второй разновидности несущая и облицовочная стены жестко связаны и воспринимают нагрузку от вышележащих конструкций. Обычно несущая стена выполняется из кирпича или блоков, изготовленных по различным технологиям.
Многослойные системы имеют целый ряд преимуществ:
1) защищают стены от сменяющихся циклов замораживания и оттаивания;
2) сглаживают температурные колебания основной ограждающей конструкции;
3) увеличивают долговечность стен;
4) смещают точку росы в сторону наружного теплоизоляционного слоя, что обеспечивает паропроницаемость стен, не уменьшает площадь внутренних помещений, позволяет применять различные конструкции для оформления фасада.
В порядке информирования
При выполнении кладки, как и при других работах, необходимо соблюдать технику безопасности.
1. Все инструменты должны использоваться только по своему прямому назначению. Перед началом работы они проверяются на предмет исправности, поскольку инструмент должен быть прочно насажен на рукоятки, рабочие поверхности должны быть ровными, без зазоров и заусенцев. Сломанным инструментом пользоваться запрещается.
2. При кладке руки должны быть защищены рукавицами.
3. Подмости и леса надо устанавливать на ровные, хорошо утрамбованные площадки (на покрытый снегом или льдом грунт стойки лесов ставить нельзя). Крепления следует проверять.
4. Леса и подмости во избежание их обрушения нельзя перегружать строительными материалами, кроме того, не нужно концентрировать их в одном месте, поскольку они не должны создавать препятствий для перемещения.
5. Настилы для лесов и подмостей не должны иметь щелей.
6. Промежуток между лесами и постройкой должен составлять не более 5 см (этого вполне достаточно, чтобы с помощью отвеса проверить вертикальность кладки).
7. При перемонтировании лесов стена должна находиться на 70 см выше уровня настила, иначе мастер должен работать в предохранительном поясе.
8. На лесах и подмостях нельзя оставлять инструменты, мусор и пр.
9. Расшивка швов осуществляется по окончании каждого ряда с подмостей или междуэтажного перекрытия – на стене находиться нельзя.
Помимо кирпича, в качестве строительного материала используется и натуральный камень (известняк, ракушечник, туф, песчаник, гранит). Каменные стены отличаются прочностью, долговечностью и обходятся достаточно дешево там, где этот материал является местным. Поскольку камень холодный, то из него обычно возводятся хозяйственные постройки, хотя при необходимости теплопроводность таких стен можно понизить, отделав их изнутри теплоизоляционными плитами, например пенобетонными, гипсокартонными и др. Для усиления эффекта сторону плит, ориентированную к кладке, можно дополнительно обшить, например, алюминиевой фольгой. Наружные стены в таких случаях оштукатуриваются.
Камни имеют правильную и неправильную форму. Кладка из камней второго вида называется бутовой. Перед началом работы следует все рассортировать, выяснив соотношение камней той и другой формы, а также количество крупных и мелких экземпляров. Для работы надо подбирать примерно одинаковые по высоте камни и не более 300 мм, с двумя (желательно параллельными) постелями. Вес бутового камня, применяющегося в строительстве, обычно составляет не более 30 кг. Экземпляры, имеющие большую массу, раскалывают (процесс называется плинтовкой). Вместе с плинтовкой также стесывают острые углы, стараясь придать форму, близкую к параллелепипеду.
В процессе кладки надо совмещать камни, различные по величине и форме, так как это позволит выложить равномерный рисунок (разумеется, и времени для этого потребуется больше). При кладке следует располагать материал так, чтобы верхние грани камня либо были горизонтальными, либо имели некоторый уклон к середине стены.
Как и кирпичная, бутовая кладка осуществляется с перевязкой швов на цементно-известковом растворе подвижностью 4–6 см.
В процессе кладки камни подбираются и подгоняются таким образом, чтобы по высоте ряды были примерно одинаковыми – 20–25 см и чтобы можно было выдерживать горизонтальность швов. Для достижения этого в одном ряду встречаются 2–3 тонких камня, нередко крупные камни входят в смежные ряды, над несколькими мелкими камнями надо положить большой, чтобы поддержать перевязку швов.
Сначала более крупные (маячные) камни, у которых смежные грани перпендикулярны друг другу, кладутся по углам, на пересечениях и примерно через 4–5 м на протяженных участках стены, из них же выполняются и версты. С обеих сторон маячных камней натягивается шнур-причалка. Для прочности камни первого ряда утрамбовываются в грунт выкопанной траншеи. По ее краям поднимаются внутренняя и наружная версты, камни для которых подбираются по высоте. Сначала они выкладываются насухо, чтобы для каждого подобрать наиболее устойчивое положение. Потом под них накладывается раствор толщиной 25 мм, и камень осаживается. Чтобы повысить прочность кладки, периодически следует выполнять горизонтальные «стяжки», т. е. перпендикулярно стене класть крупные камни, которые свяжут наружную и внутреннюю версты.
Промежуток между верстами заполняется раствором (его должно быть достаточно для того, чтобы излишек выдавливался в швы между отдельными камнями).
Требования к камням забутки менее строгие, они могут иметь любую форму и размер. Но при этом необходимо следить, чтобы камни не касались друг друга без прослойки раствора (это негативно сказывается на прочности кладки), не качались, нужно осаживать их молотком. Работа по заполнению забутки завершается расщебенкой, при которой в раствор погружаются мелкие камни и щебень. После этого поверхность ряда выравнивается, при необходимости добавляется раствор в возникшие углубления между камнями.
Остальные ряды кладутся в таком же порядке и с соблюдением перевязки швов.
Через 30–40 мин после окончания кладки швы расшиваются, и для очередного ряда снова устанавливаются угловые камни, между которыми вкладываются штыри для крепления шнура-причалки. Если нижняя поверхность камня не отличается особой ровностью, то под него следует подложить прокладку, которая придаст ему устойчивое положение (после того как раствор схватится, ее надо вынуть, а открывшуюся полость заполнить свежим раствором). Иногда камень не удается зафиксировать прокладкой. В таком случае его можно подпереть бруском (100 x 50 мм), установленным под небольшим углом к стене.
Достигнуть такой тщательной перевязки, как при кирпичной кладке, конечно, невозможно. Но тем не менее необходимо стараться подбирать камни для верст и забутки так, чтобы можно было поочередно класть камни то длинными сторонами (ложками), то короткими (тычками), в смежных рядах над ложковыми размещать тычковые камни, и наоборот (рис. 75), обеспечивая тем самым перевязку швов, аналогичную той, которая создается при цепной системе.


Рис. 75. Перевязка швов при кладке из бутового камня: а – стен; 1 – ложок; 2 – тычок; б – пересечения стен; в – углов
Для усиления декоративности стен применяется циклопическая кладка (рис. 76), при которой для наружной версты подбираются камни и выкладываются так, чтобы швы между ними образовывали рисунок.

Рис. 76. Фрагмент циклопической кладки
Для оформления дверных и оконных проемов подбираются камни более правильной формы (при необходимости внешние плоскости можно подтесать), или бутовая кладка совмещается с кирпичной (кирпичи перевязываются с бутом). В этом случае и перемычка должна быть кирпичной. В остальных применяются железобетонные или деревянные перемычки.
Чтобы уменьшить толщину каменной стены, довести ее до наименьшей толщины 400 мм (это существенно сократит финансовые, трудовые, временные расходы) и при этом значительно улучшить теплотехнические свойства, целесообразно отделать ее современными теплоизоляционными материалами с внутренней или внешней стороны.
Из известняка, туфа и других мягких пород (плотность не более 1800 кг/м3) выпиливаются камни правильной формы. В них не должно быть трещин, прослоек глины и других дефектов. В зависимости от точности размеров, качества углов и ребер камни подразделяются на первый и второй сорт. Первосортные используются для лицевой кладки и облицовки.
В порядке информирования
Как вариант, может использоваться комбинированная «наливная» стена. Она не менее прочная, чем чисто каменная, но требует меньше времени для возведения и является менее трудоемкой. Чтобы внешний вид стены был более красивым, наружную версту нужно выложить из камня, а потом с внутренней стороны устанавливать опалубку (ее лучше сделать скользящей) и залить бетонную смесь из раствора и щебня, взятых в равной пропорции. Поскольку изнутри стена получается ровной, ее будет легче обшить каким-либо стеновым материалом, например сосновыми панелями, гипсокартоном и др. Для усиления прочности через каждые 2–3 ряда надо устанавливать стяжные камни, глубоко утапливая их в раствор. Для опалубки подойдут бруски сечением 50 x 100 мм и доски толщиной 25 мм, которые сшиваются в виде панелей размером 600 x 2400 мм. Внизу и вверху в них необходимо просверлить отверстия диаметром 20 мм, причем верхние и нижние должны совпадать по вертикали. При использовании таких панелей стена толщиной 350 мм будет возведена в пять этапов. Кроме того, понадобятся болты диаметром 16 мм и длиной 230 мм.
Весь процесс осуществляется следующим образом.
1. Сначала выкладывается из камней наружная верста высотой, которая немного превышает высоту панели (600 мм).
2. Когда раствор схватится (для стяжки стены с бетоном между камнями надо проложить проволоку и анкерные связи из гофрированного металла длиной 80 мм (через каждые 60 см по горизонтали и 30 см по вертикали), потом с шагом 90 см установить арматурные прутки диаметром 13 мм), с внутренней стороны устанавливаются панели опалубки (их вертикальность контролируется отвесом), которые стягиваются болтами и подпираются подкосами из брусков сечением 50 x 100 мм.
3. В образовавшийся промежуток заливается раствор. Когда его уровень достигнет верхних отверстий в панелях, в них нужно вложить болты, залить оставшийся раствор в виде бетонной подушки и выложить несколько рядов камней наружной версты.
4. Как только бетон схватится, нужно перевесить панели, надев их нижними отверстиями на вставленные вверху болты.
5. Далее все действия повторяются. До стены высотой 3000 мм понадобилось 5 заливок и 150 болтов, торчащие концы которых необходимо срезать заподлицо с внутренней стороны по окончании строительства.
Для наглядности описанный процесс представлен на рис. 77, 78.

Рис. 78. Стена (вид в разрезе): 1 – бетонная подушка; 2 – литая стена; 3 – анкерная связь; 4 – каменная кладка; 5 – стяжные камни
Заливка бетона: монолитные стены, несъемная опалубка
В индивидуальном строительстве применяются не только мелкоблочные материалы. Стены можно возвести и в виде монолита из легких бетонов. Преимущества таких технологий заключаются в том, что они достаточно просты и могут использоваться застройщиком даже при отсутствии большого опыта, обходятся довольно дешево и при этом отличаются хорошими эксплуатационными характеристиками.
Заполнителями в легких бетонах выступают шлак, кирпичный бой, керамзит, опилки и различные местные материалы, связующими – цемент, известь, гипс, глина. Чаще всего в качестве заполнителя используется топливный или доменный шлак, для увеличения прочности которого добавляется примерно 10–20 % от его объема песка.
Как песок, так и шлак не должен содержать никаких примесей: глины, грунта, золы и пр. Прочность и теплоизоляционные свойства шлакобетона в немалой степени определяются его гранулометрическим составом – соотношением крупных (5–40 мм) и мелких (0,2–5 мм) фракций заполнителя. Если преобладают крупные частицы, то шлакобетон получается легким, но недостаточно прочным; если большую часть заполнителя составляет мелкий шлак, то шлакобетон будет не только более плотным, но и более теплопроводным. Исходя из этого, опытным путем установлено, что для наружных стен оптимально соотношение мелкого и крупного шлака – от 3: 7 до 4: 6; для внутренних несущих стен, в которых более важным показателем является прочность, пропорции сдвигаются в сторону мелких фракций. Более того, частицы размером более 10 мм в смесь не вводятся вообще.
Основным связующим является цемент, в который добавляется глина или известь. Это позволяет не только сэкономить дорогой материал, но и улучшить качество шлакобетона, который благодаря добавкам приобретает пластичность.
В табл. 8 представлены компоненты для приготовления шлакобетона.
Таблица 8
Соотношение компонентов в составе шлакобетона

Перед приготовлением шлакобетона заполнитель надо пропустить через сита с ячейками 5 x 5 и 1 x 1 мм. Шлак, оставшийся на первом, относится к крупным, на втором – к мелким. Соединив 60–70 % крупной фракции с 30–40 % мелкой, можно переходить к дальнейшим действиям.
Чтобы приготовить шлакобетон, цемент, песок и шлак (крупные фрагменты надо увлажнить) тщательно перемешиваются в сухом состоянии, потом добавляются известковое или глиняное тесто и вода. Состав еще раз перемешивается и может сразу же использоваться. При этом необходимо такое количество смеси, чтобы ее можно было израсходовать в течение не более 2 ч.
Для выполнения монолитной стены необходимо сделать опалубку высотой 40–60 см, доски которой следует хорошо подогнать, иначе цементное молоко просто вытечет. Для опалубки подойдут как строганые, так и нестроганые доски. Первые – в том случае, если дальнейшая отделка стен не предполагается, вторые – если поверхности будут оштукатурены.
Удобнее всего воспользоваться переставной опалубкой (рис. 79), выполненной из горизонтальных деревянных щитов и стяжек или вертикальных металлических щитов и стержней.


Рис. 79. Конструкция переставной опалубки: а – деревянной;
б – металлической; 1 – струбцина; 2, 3 – горизонтальные наружные и внутренние щиты; 4, 5 – верхняя и нижняя деревянные стяжки; 6 – металлическая стяжка; 7 – шлакобетон; 8 – вертикальный брус; 9 – клинья
Толщина монолитных стен равна 550–650 мм. Если в качестве заполнителя применяются керамзит или пемза, стенка может быть и тоньше – 450–500 мм.
Подготовленная и установленная опалубка послойно заполняется шлакобетоном (примерно 150–200 мм), после чего уплотняется и штыкуется, чтобы удалить из материала воздух, который может образовать в массиве стены карманы и нарушить ее прочность.
Примерно через 2–3 дня (в зависимости от погоды) опалубка разбирается и монтируется на другом месте. Возведенный участок стены нуждается в уходе, который состоит в защите от солнечных лучей и увлажнении.
К окончательной отделке стены можно приступить через 3–4 недели, дождавшись, пока шлакобетон полностью отвердеет и наберет прочность.
С внешней стороны стены оштукатуриваются или отделываются другими современными материалами. Неплохим технологическим решением нужно признать облицовку стен кирпичом.
Будучи выполненной с расшивкой швов, кирпичная стена не только придаст монолиту более эффектный вид, но и может служить опалубкой в процессе бетонирования.
Перемычки над оконными и дверными проемами в силу специфики материала стен выполняются рядовыми из монолитного железобетонного пояса толщиной 300–400 мм, укладывающегося по деревянной опалубке. При этом опорные части перемычек имеют длину 400–500 мм с обеих сторон проема.
Монолитные стены, как и мелкоблочные, могут выполняться с пустотами. Это имеет ряд плюсов: прежде всего уменьшается расход строительного материала и повышаются теплоизоляционные свойства ограждающей конструкции.
В качестве пустотообразователей выступают вкладыши из легкого бетона, пенополистирола и др. Чтобы пустоты не снизили прочность стены, плотность шлакобетона следует повысить.
Возведение стен обойдется дешевле (на 30–40 % по сравнению со шлакобетонными и в 2–3 раза по сравнению с кирпичными), если использовать отходы деревообрабатывающей промышленности, в частности опилки (табл. 9). Дополнительно рекомендуется вводить хлористый кальций, жидкое стекло и др. (примерно 2–4 % от объема вяжущего).
Таблица 9
Соотношение компонентов в составе опилкобетона

Опилкобетонный состав готовится следующим образом: по отдельности просеянные через сито с ячейками 1 x 1 см опилки смешиваются с песком, а цемент – с известковым тестом, после чего смеси соединяются, перемешиваются, выкладываются в опалубку слоями толщиной 10–15 см, после чего штыкуются, уплотняются и оставляются на 2–3 дня.
Стены из опилкобетона легкие, экологичные, отличаются низкой теплопроводностью, достаточно долговечные, особенно если предпринять для этого некоторые меры, в частности обеспечить гидроизоляцию фундамента, увеличить свес кровли до 600 мм. Прочность стен повысится, если их армировать металлическим прутком через 30–40 см по высоте в двух – трех местах по ширине стены (наибольшее внимание следует уделить местам примыкания и пересечения наружных и внутренних стен); на уровне перекрытия выполнить обвязку из досок сечением 150–200 x 50 мм с заделкой концов в полдерева; оконные проемы размещать на расстоянии не менее 1,5 м от углов; выполнять простенки шириной не менее 1 м; перемычки над оконными и дверными проемами заделывать в стены, предварительно изолировав, на глубину не менее 250 мм.
Толщина наружных опилкобетонных стен зависит от средней температуры самой холодной пятидневки в году. Если она составляет –20 °C, то достаточно 350 мм, при –40 °C – 400 мм. Толщина внутренних стен – 300 мм.
В порядке информирования
Выше мы представили традиционный способ возведения монолитных стен. Но современные технологии ушли далеко вперед, более того, они сейчас находятся на таком уровне, который позволяет архитекторам и дизайнерам не только принимать, но и реализовывать самые смелые решения, в частности совершенно не обязательно, чтобы дом выглядел скучной серой бетонной коробкой. Новые опалубочные конструкции дают возможность «ломать» фасад, придавать ему особую архитектурную выразительность.
Кроме того, монолитный дом строится очень быстро, особенно если снимается проблема с подачей раствора на строительную площадку и используется современная опалубочная конструкция. Кстати, надо заметить, что необходимости в ее приобретении нет.
Такие устройства можно арендовать, если вы планируете вести строительство собственными силами, или нанять бригаду, у которой есть опалубочная система. Но очень важно, какой именно опалубкой они владеют, поскольку от этого зависят и сроки возведения стен, и их качество, и то, в какую сумму обойдется дом.
Мировые лидеры по изготовлению опалубочных систем – немецкие производители, например фирма PERI, работающая в этой области с 1970-х гг. Опалубка Trio – одна из лучших ее разработок, которая отличается универсальностью и используется для строительства объекта любой сложности. Опалубка представляет собой оцинкованную с обеих сторон стальную раму с нанесенным на нее специальным порошковым покрытием, благодаря которому она легко очищается после распалубки. Рама обшита финской фанерой толщиной 18 мм. Монтаж системы, состоящей из шести типоразмеров щитов (30, 60, 72, 120, 240 см), которые могут собираться в вертикальном и горизонтальном положении, осуществляется с помощью универсального (подходит для всех соединений) замка BFD. Конструкция имеет высоту 540 см, но при сборке не потребует никаких ригелей – достаточно на ребра жесткости установить этот замок (рис. 80).
На поверхность опалубки путем распыления наносится специальная смазка (периклин или перибиоклин), благодаря которой стыки максимально хорошо подгоняются и стены получаются выровненными. Помимо этого, смазка облегчает очистку конструкции после распалубки (моментально отходит прилипший бетон, обрызганный таким составом). В течение семи дней смазка испаряется с поверхности стены, поэтому не является препятствием для ее отделки.


Рис. 80. Опалубка Trio: а – элементы опалубки; б – универсальный замок BFD; в – фрагмент смонтированной опалубки
Неплохо себя зарекомендовала итальянская опалубочная система Faresin, которая располагает большим количеством модулей и позволяет создавать практически неограниченное число разнообразных строительных конструкций, причем для ее монтажа не требуются высококвалифицированные специалисты. В данной конструкции оптимально сочетаются показатели жесткости, прочности и веса.
Каркас выполнен с высокой точностью из стальных и алюминиевых профилей, щиты – из ламинированной фанеры толщиной 18 мм. Собранная алюминиевая конструкция весит 28–32 кг/м2, стальная – 40–45 кг/м2. Два человека с помощью крана монтируют опалубку за 27 мин.
Отечественные опалубочные системы вполне конкурентоспособны и отличаются доступной ценой, например опалубка СТАЛФОРМ из стальных и алюминиевых модулей высотой 3 и 3,3 м с ламинированной фанерой и весом 30 и 50 кг/м2 соответственно.
Для того чтобы дом отвечал всем требованиям по теплосбережению, уровню комфорта, архитектурной выразительности, разрабатываются новые технологии, внедряются современные материалы. Если говорить упрощенно, то технология монолитного строительства осуществляется так: на площадке, отведенной под дом, по контуру стены будущего строения монтируется опалубка, в которую устанавливается каркас из арматуры и заливается бетон. Когда он наберет необходимую мощность, опалубка или демонтируется, или становится частью только что возведенной стены. Во втором случае она называется несъемной. Ее перспективность уже не вызывает сомнений.
Способ возведения стен с применением несъемной опалубки – это гибрид двух технологий: монолитного домостроения и строительства стен из пустотных блоков или панелей. Поэтому неудивительно, что весь процесс состоит из тех же этапов, за исключением последнего (опалубка остается на месте):
1) возведение стены из блоков или панелей;
2) армирование;
3) заполнение бетоном внутренних пустот.
Блоки и панели играют роль опалубки, которая потом не демонтируется, а превращается в многослойную ограждающую конструкцию. По данной технологии, получившей в европейских странах широкое распространение, строятся жилые дома, хозяйственные и небольшие промышленные здания (как правило, не выше пяти этажей).
Отличительными особенностями несъемной опалубки являются небольшой вес элементов, простая технология и отсутствие необходимости в применении тяжелой техники.
В настоящее время наибольшую известность получили несъемные опалубки из пенополистирола, хотя есть и другие технологии с использованием, например, ДСП, ЦСП и др. Рассмотрим некоторые из них.
«ИЗОДОМ» – это технология, доказавшая свою надежность и прошедшая проверку временем. В соответствии с ней несъемная опалубка изготавливается из строительного пенополистирола, который был изобретен еще в 1951 г. в Германии. Практически сразу его начали применять в качестве теплоизолятора для утепления наружных стен (на 97 % состоит из воздуха).
В начале 1960-х гг. была разработана и внедрена технология, согласно которой из пенополистирола стали делать опалубку в виде блоков, установленных на строительной площадке и залитых жидким бетоном. Этот способ заменил собой утепление стен пенополистирольными плитами (хотя он по-прежнему применяется для теплоизоляции уже построенных зданий). С течением времени пенополистирольные блоки модернизировались, усовершенствовались и в конечном итоге превратились в удобные, прочные, технологичные конструкции, которые позволяют реализовать любое архитектурное решение.
Несъемная опалубка «ИЗОДОМ» – это блоки (рис. 81), выполненные из твердого пенополистирола, со сквозными пустотами. На их поверхности имеется специальная система замков, которая обеспечивает герметичность конструкции и предотвращает потери бетона. Монтаж модулей осуществляется без каких-либо усилий, тем более что блоки длиной 1,5 м практически невесомы.
Правообладателям!
Это произведение, предположительно, находится в статусе 'public domain'. Если это не так и размещение материала нарушает чьи-либо права, то сообщите нам об этом.