Текст книги "Погрузка и разгрузка. Справочник груз-менеджера"
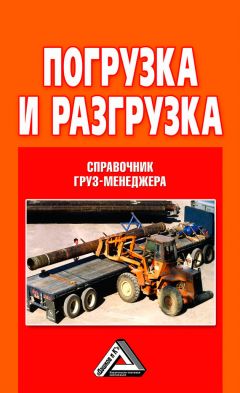
Автор книги: Владислав Волгин
Жанр: Отраслевые издания, Бизнес-Книги
сообщить о неприемлемом содержимом
Текущая страница: 16 (всего у книги 40 страниц)
Рекомендуемая знаковая сигнализация при перемещении грузов кранами[2]2
Рекомендуемая форма стропальщика: жилет и каска – желтого цвета, рубашка – голубого, повязка – красного.
[Закрыть]


Рекомендуемое
Наряд-допуск № ____
на право выхода на крановые пути и проходные галереи
мостовых и передвижных консольных кранов
для производства ремонтных и других работ


Примечания: 1. Наряд-допуск на право выхода на рельсовые пути и проходные галереи мостовых кранов для производства ремонтных и других работ выдается согласно приказу по организации руководителю работ (начальнику цеха, участка, прорабу, в подчинении которых находятся работники, производившие ремонт).
2. Наряд-допуск оформляется в двух экземплярах. Первый экземпляр выдается крановщику, второй выдается ответственному производителю работ.
Рекомендуемое
Наряд-допуск №____
на производство работ краном вблизи воздушной линии электропередачи


Примечания: 1. Наряд-допуск выписывается в двух экземплярах: первый выдается крановщику, второй – ответственному производителю работ.
2. Пункт 11 заполняется в случае работы крана в охранной зоне линии электропередачи.
3. Работы вблизи линий электропередачи выполняются в присутствии и под руководством лица, ответственного за безопасное производство работ кранами.
Рекомендуемое
Акт сдачи-приемки кранового рельсового пути в эксплуатацию


Схемы строповки штабелируемых грузов
Строповка валов


Строповка коленчатого вала двигателя

Строповка барабанов и обечаек

Строповка шестерен, шкивов, венцов, маховиков, бандажей

Строповка кубиков и дисков

Строповка бухт проволоки, короба

Строповка деталей пресса

Строповка конусных деталей

Строповка корпусов и рам

Строповка обрудования, узлов, деталей

Строповка малогабаритных ферм

Строповка арочной фермы балансирной траверсой

Строповка железобетонной фермы балансирной траверсой

Строповка легких колонн

Строповка крупного камня

Схемы строповки штабелируемых грузов
Строповка листового металла групповым стропом

Строповка листового металла рычажно-эксцентриковыми захватами

Строповка листового металла с помощью слесарных струбцин

Подхват для строповки пакета листового металла

Строповка болванки спаренными клещевыми захватами

Строповка профильного стального проката

Строповка пакета траверс высоковольтной опоры

Строповка пирамидообразной конструкции высоковольтной опоры

Захват Ларина

Строповка круглых болванок

Полуавтоматическая строп-удавка

Строповка прямоугольной конструкции специальным стропом

Схема строповки железобетонных изделий

Строповка лестничного марша

Строповка перегородки траверсным захватом

Строповка крупногабаритной плиты специальной траверсой

Клещевой захват для ящиков

Захват для деревянных бочек

Строповка кирпича на поддоне Черны вилочным подхватом

Строповка кирпича на поддоне Широкова

Строповка бревен захватом-траверсой


Строповка подтоварника универсальными стропами

Строповка бревен облегченным стропом со свободным крюком

Поштучная строповка бревен

Строповка пиломатериалов рамным захватом

Характеристика обрабатываемых грузов
1. В зависимости от вида, способа складирования и строповки грузы классифицируются на следующие группы:
1.1. Штучные нештабелируемые грузы – металлические конструкции, двигатели, станки, машины, механизмы, крупные железобетонные изделия и т. д. Группа штучных нештабелируемых грузов наиболее многочисленна и разнообразна по форме, поэтому единых типовых способов строповки их, пригодных для всех грузов этой группы, не существует;
1.2. Штучные штабелируемые грузы – прокатная сталь, трубы, лесо-и пиломатериалы, кирпич, шлакоблоки, типовые железобетонные изделия, плиты, панели, блоки, балки, лестничные марши, ящики, бочки и др. изделия геометрически правильной формы;
1.3. Насыпные грузы – транспортируются в таре, грейферами, транспортерами и др. Складируются в штабеля, определяющиеся углом естественного откоса материала и ограничивающих поверхностей (уголь, торф, шлак, песок, щебень, цемент, известь, мелкая металлическая стружка и т. п.);
1.4. Полужидкие пластичные грузы – грузы, обладающие способностью некоторое время сохранять приданную форму или с течением времени затвердевать. К таким грузам относятся бетонные массы, растворы, известковое тесто, битумы, смазывающие вещества и т. п. Вязкость полужидких грузов и зависание их на стенках емкостей транспортирующих средств, способность быстро схватываться и твердеть (бетон, раствор и др. грузы) затрудняют их транспортировку. Такие грузы должны транспортироваться в специальной таре;
1.5. Жидкие грузы – грузы, не имеющие определенной формы, транспортируются в бочках, бидонах, бутылях, цистернах, ковшах и т. д. (вода, жидкие горючие и смазочные вещества, кислоты, щелочи, мастики и т. д.);
1.6. Газообразные грузы транспортируются обычно под давлением в баллонах, других сосудах и трубопроводным транспортом.
2. В зависимости от массы грузы делятся на четыре категории:
2.1. Легковесные грузы – грузы массой не более 250 кг. К ним относятся такие материалы, как войлок, кожа, пакля, фанера, сухая штукатурка, легкие детали машин и др.;
2.2. Тяжеловесные грузы – грузы, масса которых находится в пределах от 250 кг до 50 т. К тяжеловесным грузам относятся все штабелируемые, насыпные, полужидкие, жидкие и нештабелируемые грузы, масса которых не превышает 50 т;
2.3. Весьма тяжелые грузы – грузы, масса которых превышает 50 т. К ним относятся штучные нештабелируемые грузы. Строповка этих грузов разрешается только стропальщикам высокой квалификации;
2.4. Мертвые грузы – особая категория грузов неизвестной массы. Мертвыми считаются грузы, закрепленные на фундаменте анкерными болтами, зарытые в землю, примерзшие к земле, прижатые другим грузом, а также поднимаемые при косой чалке. Поднимать мертвые грузы краном запрещается.
3. В зависимости от формы и размеров грузы делятся на габаритные и негабаритные:
3.1. Габаритный груз – груз, размеры которого не превышают габариты подвижного состава железных дорог, а для автомобильного и другого вида наземного безрельсового транспорта – норм, установленных Правилами дорожного движения Российской Федерации;
3.2. Негабаритный груз – груз, размеры которого выходят за габариты подвижного состава железных дорог или наземного безрельсового транспорта. Негабаритными грузами могут быть большие котлы, машины, трансформаторы и т. п. Размеры нарушений габарита не должны превышать определенных величин, при которых еще возможна перевозка груза за счет сокращения зазора между габаритами приближения строений и подвижного состава.
В зависимости от величины нарушения габарита грузы разделяются на пять степеней негабаритности, каждая из которых имеет свои предельные очертания.
На негабаритном грузе при перевозке его по железной дороге указывается соответствующая степень негабаритности.
4. Длинномерные грузы составляют особую группу грузов (детали и узлы крупных машин, оборудование, металлоконструкции и т. п.), которые перевозятся на специальных железнодорожных платформах или трайлерах. Негабаритные, сверхгабаритные и длинномерные грузы разрешаются к перевозке в вагонах или на платформах только после утверждения схемы погрузки отделением или управлением железной дороги.
5. Грузы по степени и характеру опасности разделяются в соответствии с ГОСТ 19433 на 9 классов опасности (табл. 1).
Классы опасности грузов
Таблица 1


6. Для подъема груза должны быть известны его масса, центр тяжести и схема строповки, при этом:
6.1. Определение массы груза может быть произведено по формулам:
Для простых грузов – Q = mV
Для сложных грузов – Q = m ΣVi;
где: Q – масса груза,
m – удельная масса (численно равна плотности) материала,
V – объем груза,
ΣVi – сумма всех частей объемов груза;
Удельная масса часто встречающихся материалов приведена в табл. 2.
Удельная масса материалов
Таблица 2

7. При выборе мест строповки груза необходимо определить расположение центра тяжести поднимаемого груза, для того чтобы избежать возможной аварийной перегрузки отдельных ветвей стропов грузоподъемных средств, потерю устойчивости и опрокидывание поднимаемого груза.
Объем и расположение центра тяжести простых геометрических фигур приведены в табл. 3.
Объем и расположение центра тяжести простых геометрических фигур
Таблица 3





Нормы браковки съемных грузозахватных приспособлений
Браковка съемных грузозахватных приспособлений, находящихся в эксплуатации, должна производиться согласно нормативным правовым актам, определяющим порядок, методы браковки и браковочные показатели.
При отсутствии у владельца нормативных правовых актов браковку элементов канатных и цепных стропов производят в соответствии с рекомендациями, приведенными в настоящем положении.
Канатный строп подлежит браковке, если число видимых обрывов наружных проволок каната превышает указанное в таблице.

Примечание: d – диаметр каната, мм.
Цепной строп подлежит браковке при удлинении звена цепи более 3 % от первоначального размера (рис. 1) и при уменьшении диаметра сечения звена цепи вследствии износа более 10 % (рис. 2).

Рис. 1. Увеличение звена цепи:
L0 – первоначальная длина звена, мм;
L1 – увеличенная длина звена, мм

Рис. 2. Уменьшение диаметра сечения звена цепи:
d0 – первоначальны диаметр, мм;
d1, d2 – фактические диаметры сечения звена, измеренные во взаимно перпендикулярных направлениях, мм
Нормы браковки канатов грузоподъемных машин
1. Браковку канатов грузоподъемных машин, находящихся в эксплуатации, проводят в соответствии с настоящим приложением.
Для оценки безопасности использования канатов применяют следующие критерии:
а) характер и число обрывов проволок (рис. 1–3), в том числе наличие обрывов проволок у концевых заделок, наличие мест сосредоточения обрывов проволок, интенсивность возрастания числа обрывов проволок;
б) разрыв пряди;
в) поверхностный и внутренний износ;
г) поверхностная и внутренняя коррозия;
д) местное уменьшение диаметра каната, включая разрыв сердечника;
е) уменьшение площади поперечного сечения проволок каната (потери внутреннего сечения)
ж) деформация в виде волнистости, корзинообразности, выдавливания проволок и прядей, раздавливания прядей, заломов, перегибов и т. п.;
з) повреждения в результате температурного воздействия или электрического дугового разряда.

Рис. 1. Обрывы и смещения проволок каната крестовой свивки


Рис. 2. Сочетание обрывов проволок с их износом:
а – в канате крестовой свивки; б – в канате односторонней свивки


Рис. 3. Обрывы проволок в зоне уравнительного блока: а – в нескольких прядях каната; б – в двух прядях в сочетании с местным износом
2. Браковку канатов, работающих со стальными и чугунными блоками, следует проводить по числу обрывов проволок в соответствии с табл. 1.
Канаты грузоподъемных машин, предназначенных для подъема людей, а также транспортирующих расплавленный или раскаленный металл, огнеопасные и ядовитые вещества, бракуют при вдвое меньшем числе обрывов проволок.
3. При уменьшении диаметра каната в результате поверхностного износа (рис. 4) или коррозии (рис. 5) на 7 % и более по сравнению с номинальным диаметром канат подлежит браковке даже при отсутствии видимых обрывов проволок.
При уменьшении диаметра каната в результате повреждения сердечника – внутреннего износа, обмятия, разрыва и т. п. (на 3 % от номинального диаметра у некрутящихся канатов и на 10 % у остальных канатов) канат подлежит браковке даже при отсутствии видимых обрывов проволок (рис. 6).
При наличии у каната поверхностного износа или коррозии проволок число обрывов как признак браковки должно быть уменьшено в соответствии с данными табл. 2.
При уменьшении первоначального диаметра наружных проволок в результате износа (см. рис. 4, д) или коррозии (см. рис. 5, д) на 40 % и более канат бракуется.
Определение износа или коррозии проволок по диаметру производится с помощью микрометра или иного инструмента, обеспечивающего аналогичную точность.
Таблица 1
Число обрывов проволок, при наличии которых канаты двойной свивки, работающие со стальными и чугунными блоками, бракуются


Примечания: 1. № – число несущих проволок в наружных прядях каната; d – диаметр каната, мм.
2. Проволоки заполнения не считаются несущими, поэтому не подлежат учету. В канатах с несколькими слоями прядей учитываются проволоки только видимого наружного слоя. В канатах со стальным сердечником последний рассматривается как внутренняя прядь и не учитывается.
3. Число обрывов не следует путать с количеством оборванных концов проволок, которых может быть в 2 раза больше.
4. Для канатов конструкций диаметром наружных проволок во внешних прядях, превышающим диаметр проволок нижележащих слоев, класс конструкции понижен и отмечен звездочкой.
5. При работе каната полностью или частично с блоками из синтетического материала или из металла с синтетической футеровкой отмечается появление значительного числа обрывов проволок внутри каната до появления видимых признаков обрывов проволок или интенсивного износа на наружной поверхности каната. Такие канаты отбраковываются с учетом потери внутреннего сечения.
6. Незаполненные строки в графе “Конструкция канатов по ИСО и государственным стандартам” означают отсутствие конструкций канатов с соответствующим числом проволок. При появлении таких конструкций канатов, а также для канатов с общим числом проволок более 300 число обрывов проволок, при которых канат бракуется, определяется по формулам, приведенным в нижней строке таблицы, причем полученное значение округляется до целого в большую сторону.
7. Канаты грузоподъемных машин, предназначенных для подъема людей, а также транспортирующих расплавленный или раскаленный металл, огнеопасные и ядовитые вещества, бракуются при вдвое меньшем числе обрывов проволок.

Рис. 4. Износ наружных проволок каната крестовой свивки: а – небольшие лыски в проволоках;
б – увеличенная длина лысок на отдельных проволоках; в – удлинение лысок в отдельных проволоках при заметном уменьшении диаметра проволок; г – лыски на всех проволоках, уменьшение диаметра каната; д – интенсивный износ всех наружных проволок каната (уменьшение диаметра проволок на 40 %)

Рис. 5. Поверхностная коррозия проволок каната крестовой свивки: а – начальное окисление поверхности; б – общее окисление поверхности; в – заметное окисление; г – сильное окисление; д – интенсивная коррозия

Рис. 6. Местное уменьшение диаметра каната на месте разрушения органического сердечника
При меньшем, чем указано в табл. 1, числе обрывов проволок, а также при наличии поверхностного износа проволок без их обрыва канат может быть допущен к работе при условии тщательного наблюдения за его состоянием при периодических осмотрах с записью результатов в журнал осмотров и смены каната по достижении степени износа, указанной в табл. 2
Таблица 2
Нормы браковки каната в зависимости от поверхностного износа или коррозии

Если груз подвешен на двух канатах, то каждый бракуется в отдельности, причем допускается замена одного, более изношенного, каната.
4. Для оценки состояния внутренних проволок, т. е. для контроля потери металлической части поперечного сечения каната (потери внутреннего сечения), вызванной обрывами, механическим износом и коррозией проволок внутренних слоев прядей (рис. 7), канат необходимо подвергать дефектоскопии по всей его длине. При регистрации с помощью дефектоскопа потери сечения металла проволок, достигшей 17,5 % и более, канат бракуется.
5. При обнаружении в канате одной или нескольких оборванных прядей канат к дальнейшей работе не допускается.
6. Волнистость каната характеризуется шагом и направлением ее спирали (рис. 8). При совпадении направлений спирали волнистости и свивки каната и равенстве шагов спирали волнистости Нв и свивки каната Нк канат бракуется при dв > 1,08 dк, где dв – диаметр спирали волнистости, dк – номинальный диаметр каната.
При несовпадении направлений спирали волнистости и свивки каната и неравенстве шагов спирали волнистости и свивки каната или совпадении одного из параметров канат подлежит браковке при dв > 4/3dк. Длина рассматриваемого отрезка каната не должна превышать 25dк.
7. Канаты не должны допускаться к дальнейшей работе при обнаружении: корзинообразной деформации (рис. 9); выдавливания сердечника (рис. 10); выдавливания или расслоения прядей (рис. 11); местного увеличения диаметра каната (рис. 12); местного уменьшения диаметра каната (см. рис. 6); раздавленных участков (рис. 13); перекручиваний (рис. 14); заломов (рис. 15); перегибов (рис. 16); повреждений в результате температурных воздействий или электрического дугового разряда.

Рис. 7. Уменьшение площади поперечного сечения проволок (интенсивная внутренняя коррозия)

Рис. 8. Волнистость каната (объяснение в тексте)

Рис. 9. Корзинообразная деформация

Рис. 10. Выдавливание сердечника


Рис. 11. Выдавливание проволок прядей:
а – в одной пряди;
б – в нескольких прядях

Рис. 12. Местное увеличение диаметра каната

Рис. 13. Раздавливание каната

Рис. 14. Перекручивание каната

Рис. 15. Залом каната

Рис. 16. Перегиб каната
Рекомендуемое
Журнал учета и периодического осмотра съемных грузозахватных приспособлений (СГЗП) и тары

Нормы и сроки испытаний ручных грузоподъемных механизмов и приспособлений


Примечания:
1. Рн – допустимая рабочая нагрузка, кН;
2. При неудовлетворительных результатах статических испытаний динамические испытания не проводятся. Статические и динамические испытания выполняются в соответствии с программой испытаний;
3. При статическом испытании пробный груз должен находиться на высоте около 100 мм от земли или пола;
4. При испытаниях канаты (цепи) должны выдерживать испытательную нагрузку без разрывов и заметного местного удлинения у каната и вытяжки отдельных звеньев у цепей;
5. Перед испытанием подъемные механизмы и приспособления должны быть проверены (осмотрены) и при необходимости отремонтированы;
6. Все механизмы и приспособления после капитального ремонта подлежат обязательному испытанию вне зависимости от очередного срока испытания;
7. Винтовые домкраты должны подвергаться осмотру 1 раз в 3 месяца
Предельные нормы браковки элементов грузоподъемных машин
Элементы грузоподъемных машин бракуются при наличии следующих дефектов:

Предельные величины отклонений рельсовых путей от проектного положения (в плане и профиле)


Примечания: * – 45 мм – для ширины колеи в 4,5 м;
60 мм – для ширины колеи в 6,0 м.
1. Показатели 1 и 3 замеряются с интервалом не более 5 м на всем протяжении кранового пути.
2. При изменении температуры на 10 °C показатель 5 изменяется на 1,5 мм.
Предельные нормы браковки основных элементов рельсовых крановых путей


Минимально допустимые расстояния для установки грузоподъемных машин в зданиях, на открытых площадках, вблизи ЛЭП и котлованов
Таблица 1


Примечания: * – допускается в обоснованных случаях от 500 до 1000 мм;
** – менее 30 м – с оформлением, в установленном порядке наряда-допуска.
Таблица 2
Допустимые расстояния от основания откоса котлована до ближайшей опоры стрелового передвижного крана

Способы и параметры укладки грузов




Примечание.
* – материал в связке, кипе.
Способы размещения и крепления грузов на открытом подвижном железнодорожном составе
1. Размещение и крепление лесо– и пиломатериалов
2. Размещение и крепление металлопроката
3. Размещение и крепление железобетонных, асбоцементных и других изделий и конструкций
4. Размещение и крепление грузов в ящичной упаковке, грузов цилиндрической формы, грузов в контейнерах
1. Размещение и крепление лесо– и пиломатериалов
1.1. Круглый лес
1.2. Пиломатериалы
1.3. Лесо– и пиломатериалы в пакетах
1.4. Лесоматериалы в специально оборудованных вагонах
1.1. Круглый лес
1.1.1. Лесоматериалы должны грузиться штабелями встык с предварительной сортировкой материала в штабеле по длине и толщине.
1.1.2. При погрузке на один вагон штабелей и пачек лесоматериалов различной длины лесоматериалы большей длины должны размещаться внизу укладки и по концам вагона.
1.1.3. Лесоматериалы, погруженные в верхней суженной части габарита погрузки, должны быть подсортированы по длине по одному размеру и по толщине – не более двух-трех смежных размеров.
1.1.4. Схемы размещения и крепления лесоматериалов на платформах и в полувагонах даны на рис. 1.1; 1.2; 1.3; 1.4.
1.2. Пиломатериалы
1.2.1. Пиломатериалы должны грузиться так, чтобы обеспечивалось их плотное прилегание друг к другу и к ограждающим стойкам.

Рис. 1.1:
1 – боковые стойки; 2 —верхние поперечные крепления; 3 – обвязка “шапки”; 4 – средние поперечные крепления; 5 – удлиненные прокладки; 6 – прокладки; 7 – утолщенные прокладки; 8 – подкладки

Рис. 1.2:
1 – боковые стойки; 2 – верхние поперечные крепления; 3 – удлиненные прокладки; 4 – обвязки “шапки”; 5 – проволочные закрепления крайних стоек
1.2.2. Толщина досок или брусьев в каждом ряду штабеля должна быть одинаковой.
1.2.3. Каждый штабель пиломатериалов длиной 2,7–5 м должен ограждаться с боков двумя парами стоек, длиной от 5 до 8 м – тремя парами стоек, длиной от 8 до 12 м – четырьмя парами стоек.
1.2.4. Лесо– и пиломатериалы длиной до 1,6 м должны грузиться вдоль полувагона с вертикальной сплошной оторцовкой грузом торцовых дверей и боковых стен полувагона по всей длине.
1.2.5. Схемы размещения и крепления пиломатериалов на платформах и в полувагонах даны на рис. 1.5; 1.6; 1.7.

Рис. 1.3:
1 – боковые стойки; 2 – верхние поперечные крепления; 3 – обвязки “шапки”; 4 — удлиненные прокладки; 5 – утолщенные прокладки; 6 — прокладки; 7 – средние поперечные крепления; 8 – подкладки

Рис. 1.4:
1 – боковые стойки; 2 – верхние поперечные крепления;
3 – обвязки “шапки”
1.3. Лесо– и пиломатериалы в пакетах
1.3.1. Пиломатериалы и круглые лесоматериалы длиной до 8 м должны перевозиться в пакетах, увязанных многооборотными полужесткими стропами, и их размещение в вагонах производится без применения подкладок и прокладок.
1.3.2. Пакеты из круглых лесоматериалов длиной менее 3 м, пиломатериалов длиной до 1,5 м должны перевозиться в полувагонах с закрытыми торцовыми дверями и с установкой торцовых щитов.

Рис. 1.5:
1 – боковая стойка; 2 – прокладки; 3 – верхние поперечные крепления;
4 – промежуточные прокладки; 5 – удлиненные прокладки; 6 – верхние поперечные бруски; 7 – проволочные увязки “шапки”; 8 – утолщенные прокладки; 9 – подкладки

Рис. 1.6:
1 – подкладки; 2 – проволочные закрепления крайних стоек; 3 – верхние поперечные крепления, 4 — боковые стойки; 5 – проволочные увязки “шапки”; 6 – удлиненные прокладки, 7— верхние поперечные бруски: 8 – промежуточные прокладки

Рис. 1.7:
1 – оторцовка; 2 – доски, скрепляющие оторцовку
1.3.3. Пакеты пиломатериалов 1350 х 1300 мм и длиной свыше 1500 мм должны укладываться в полувагоны без стоек и прокладок в два ряда по ширине, в два яруса по высоте, в несколько штабелей по длине вагона (в зависимости от длины пакета) с укладкой поверх второго яруса трапецеидальных пакетов “шапки” и их закреплением за основание пакетов второго яруса с использованием концов цепей многооборотных полужестких стропов.
1.3.4. Пакеты пиломатериалов длиной 3 м и более размещаются на платформе без прокладок до высоты стоек и крепятся как непакетированные пиломатериалы.
1.3.5. Пакеты из круглых лесоматериалов длиной от 3 до 8 м на платформу и в полувагон должны грузиться в два яруса по высоте без подкладок и прокладок.
1.3.6. Схемы размещения и крепления лесо– и пиломатериалов в пакетах на платформах и в полувагонах даны на рис. 1.8; 1.9; 1.10; 1.11, в брусково-проволочной обвязке – на рис. 1.12, в пакетах, обвязанных стальной лентой, – на рис. 1.13 и 1.14.

Рис. 1.8:
1 – проушина; 2 – цепь для закрепления; 3 – проволочная закрутка

Рис. 1.9

Рис. 1.10

Рис. 1.11

Рис. 1.12:
1 – верхние поперечные крепления; 2 – боковые стойки; 3 – продольные доски; 4 – соединительные доски; 5 – упорные бруски

Рис. 1.13:
1 – упор; 2 — утолщенная подкладка; 3 — средняя подкладка; 4 — межпакетная прокладка; 5, 6 – нижняя и средняя удлиненные прокладки;
7 – прижимной брусок; 8 — упорные доски; 9 — проволочная увязка “шапки”; 10 — стяжка стоек; 11 — распорная доска

Рис. 1.14:
1 – межпакетная прокладка; 2 — средняя стяжка стоек; 3 — верхняя стяжка стоек; 4 — прижимной брусок; 5 – проволочная увязка; 6, 7 – средняя и нижняя удлиненные прокладки; 8 — распорные доски; 9 — упорные доски; 10 — утолщенная подкладка; 11 – упор; 12 — средняя подкладка
1.4. Лесоматериалы в специально оборудованных вагонах
1.4.1. Для перевозки круглых лесоматериалов используются также четырехосные платформы грузоподъемностью 61 т со стационарно установленными металлическими рамами (с закреплением в стоечных скобах), обеспечивающими наклон штабелей груза к середине платформы и крепление груза в верхних стойках рамы с помощью цепей и с загрузкой в пределах обычного или зонального габаритов.
1.4.2. Схемы размещения и крепления лесоматериалов в специально оборудованных вагонах даны на рис. 1.15; 1.16; 1.17; 1.18; 1.19; 1.20.
2. Размещение и крепление металлопроката
2.1. Сортовая прокатная сталь
2.2. Листовой металл в пачках
2.3. Листовой металл толщиной 6-160 мм
2.4. Слябы
2.5. Рулоны
2.6. Трубы
2.1. Сортовая прокатная сталь
2.1.1. Сталь полосовая, круг, шестигранник, уголок, швеллер, зет, узкоколейные рельсы, арматурно-периодический профиль и др. в пачках на платформу или в полувагон должны укладываться параллельно друг другу без перекрещивания.
2.1.2. Сортовой металл длиной до 6,5 м размещают на платформе или в полувагоне в несколько штабелей, располагаемых последовательно вдоль вагона, и ограждают с торцев платформы с применением торцовых стоек.

Рис. 1.15
а – общий вид погрузки платформы с удлиненными звеньями (б) и наставками (в) стоек; 1 – платформа; 2 – металлическая рама; 3 – стоечная скоба платформы; 4 – уширенная площадка рамы; 5 – удлиненные звенья или наставки стоек; 6 – цепи для закрепления “шапки”; 7 – замковое кольцо рычага; 8 – фигурное звено

Рис. 1.16

Рис. 1.17

Рис. 1.18

Рис. 1.19

Рис. 1.20
2.1.3. Сортовой металл длиной от 6,5 до 10,5 м укладывают пачками в два штабеля внахлестку посередине платформы, длиной от 10, 6 до 13 м – в один штабель, длиной от 13,1 до 13,7 м – с откинутыми на кронштейны торцевыми бортами.
2.1.4. Схемы размещения и крепления сортового металла на платформах и в полувагонах даны на рис. 2.1; 2.2; 2.3; 2.4; 2.5.

Рис. 2.1:
1 – боковые стойки;.2 – увязка стоек; 3 – доски торцового ограждения; 4 – торцовые стойки

Рис 2.2:
1 – боковые стойки; 2 – увязка стоек; 3 — доски торцового ограждения; 4 – торцовые стойки

Рис. 2.3

Рис. 2.4

Рис 2.5:
1 – деревянный щит; 2 – квадратная заготовка; 3 – обвязка пачек;
4 — подкладка
2.2. Листовой металл в пачках
2.2.1. Пачки листового металла размером до 900 х 1100 мм должны размещаться в полувагонах вдоль и поперек равномерно по всей площади пола с погрузкой от торцовых дверей к середине вагона.
2.2.2. Пачки листового металла длиной 1,5–2,3 м и 2,8–5,5 м должны укладываться вдоль полувагона вплотную друг к другу в несколько штабелей симметрично продольной оси с размещением крайних пачек вплотную к боковым стенкам.
2.2.3. Пачки листового металла длиной от 5,5 до 7,5 м должны укладываться в один продольный ряд двумя штабелями внахлестку с отступлением от торцовых дверей на 1,0 м и с опорой на подкладки, уложенные по всем поперечным балкам полувагона.
2.2.4. Пачки листового металла длиной от 9,0 до 11,5 м должны размещаться одним штабелем с опорой на две подкладки, уложенные на шкворневые балки полувагона.
2.2.5. Схемы размещения и крепления листового металла в пачках на платформах и в полувагонах даны на рис. 2.6; 2.7; 2.8; 2.9.

Рис. 2.6:
1 – утолщенные подкладки; 2 — проволочная обвязка штабеля;
3 — подкладки

Рис. 2.7

Рис. 2.8:
1 – упорные бруски; 2 – распорные бруски; 3 – соединительные планки

Рис. 2.9
2.3. Листовой металл толщиной 6-160 мм
2.3.1. Листовой металл толщиной 6-160 мм должен размещаться и крепиться в четырехосных полувагонах в зависимости от ширины и длины листов с ограждением устанавливаемыми вертикально деревянными брусками стен и торцовых дверей полувагонов с деревянной обшивкой кузова.
2.3.2. Схемы размещения и крепления листового металла толщиной 6160 мм в полувагонах даны на:
рис. 2.10 – для металла (1300–1400) и (5910-11700) мм;
рис. 2.11 – для металла (1401–1700) и (2800–3600) мм;
рис. 2.12 – для металла (1401–1700) и (3610–3900) мм;
рис. 2.13 – для металла (1701–2700) и (5500–9000) мм.

Рис. 2.10:
1 – подкладки; 2 – поперечные упорные бруски; 3 – поперечные обвязки;
4 — доска; 5 – соединительные планки; 6 — распорные бруски

Рис. 2.11:
1 – деревянный вертикальный брусок;
2 — листы, погруженные горизонтально

Рис. 2.12:
1 – деревянный вертикальный брусок;
2, 3 — листы, погруженные соответственно горизонтально и внахлестку;
4 — деревянные прокладки

Рис. 2.13:
1 – подкладки; 2 — утолщенные подкладки; 3 —прокладки; 4 — соединительные планки; 5 – распорные бруски
2.4. Слябы
2.4.1. Слябы длиной 1150–1950 мм, шириной 1000–1250 мм и толщиной 100–200 мм должны укладываться в полувагон в три яруса симметрично продольной и поперечной осям вагона, на деревянные подкладки.
2.4.2. Слябы длиной 2000–2600 мм, шириной 1000–1250 мм и толщиной 100–200 мм должны укладываться в полувагон в три яруса с укладкой в нижнем ярусе на подкладках у торцовых дверей поперек по одному слябу.
2.4.3. Слябы длиной 2600–3500 мм, шириной 1000–1700 мм и толщиной 100–200 мм должны размещаться в два ряда на подкладках.
2.4.4. Схемы размещения и крепления слябов в полувагонах даны на рис. 2.14; 2.15; 2.16.

Рис. 2.14:
1 – подкладки; 2—щит

Рис 2.15:

Рис. 2.16:
1 – подкладки; 2 – щит
2.5. Рулоны
2.5.1. Ленточный металл толщиной до 6 мм и шириной до 700 мм в рулонах (кругах) наружным диаметром до 1300 мм и весом одной единицы до
2,5 т на платформу должен укладываться продольными рядами (в четыре ряда – диаметром 600–650 мм; в три ряда – диаметром от 700 до 900 мм; в два ряда – диаметром от 900 до 1300 мм) симметрично продольной оси платформы наклонно или вертикально, а у торцовых бортов платформы – горизонтально.
2.5.2. Рулонный металл весом от 2,0 до 3,5 т, наружным диаметром от 1000 до 1350 мм и высотой 500–700 мм должен размещаться в полувагоне в два яруса симметрично продольной и поперечной осям полувагона с опорой каждого ряда на две продольные прокладки. Верхний ярус укладывается вдоль вагона над хребтовой балкой.
2.5.3. Рулоны диаметром до 1400 мм и весом от 3,5 до 4,5 т должны укладываться в полувагоне вертикально в один ярус в 2–3 ряда симметрично продольной оси вагона.
Правообладателям!
Это произведение, предположительно, находится в статусе 'public domain'. Если это не так и размещение материала нарушает чьи-либо права, то сообщите нам об этом.