Текст книги "Устройство полов. Материалы и технологии"
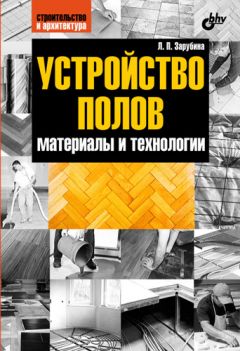
Автор книги: Людмила Зарубина
Жанр: Хобби и Ремесла, Дом и Семья
сообщить о неприемлемом содержимом
Текущая страница: 1 (всего у книги 18 страниц)
Людмила Зарубина
Устройство полов. Материалы и технологии
Введение
Пол – один из важнейших элементов конструкции и интерьера здания, который воспринимает эксплуатационные воздействия. Устройство полов является одним из наиболее трудоемких строительных процессов. В гражданском строительстве трудоемкость изготовления полов составляет 17–20 % от общестроительных работ.
К полу предъявляется комплекс требований – разнообразных и порой противоречивых (конструктивных, эксплуатационных, санитарно-гигиенических, декоративных и др.), зависящих от назначения помещения.
Полы гражданских зданий должны быть прочными, износостойкими, упругими, гладкими (но не скользкими), обладать малым теплоусвоением, легко очищаться от загрязнений, иметь эстетичный вид и соответствовать архитектуре интерьера.
К полам промышленных зданий предъявляют повышенные требования по сопротивляемости механическим воздействиям (истиранию, удару и др.), а для некоторых производств – по химической стойкости, теплостойкости и др.
В помещениях с повышенной влажностью и "мокрым" режимом эксплуатации полы должны быть водостойкими и водонепроницаемыми, а в пожароопасных – несгораемыми. Развитие современных отраслей промышленности (например, радиоэлектроники), а также повсеместное использование компьютерной техники выдвигает повышенные требования к таким характеристикам полов, как беспыльность, безыскровость, электропроводность.
Современный пол представляет собой многослойную конструкцию и состоит из покрытия, прослойки, гидроизоляции и основания. Каждый слой пола выполняет свою роль в единой конструкции и обеспечивает общее слагаемое качества всего сооружения.
Основание под пол (стяжка) может быть устроено как на монолитных бетонных перекрытиях, так и на грунтах (подстилающем слое) при выполнении соответствующих требований СНиПа.
Основание под покрытие (стяжка) – это слой пола, служащий для выравнивания поверхности нижележащего слоя перекрытия заданного уклона, укрытия различных трубопроводов, распределения нагрузок по нежестким нижележащим слоям.
Покрытие – это верхний слой пола, непосредственно подвергающийся различным эксплуатационным воздействиям. К ним можно отнести статические или динамические нагрузки, попадание на поверхность пола различных химических веществ, температурные перепады и т. п. Покрытие пола соединяется с основанием посредством прослойки, которая обеспечивает их надежное соединение, не допуская отслаивания покрытия от основания в процессе его эксплуатации.
В тех случаях, когда условия эксплуатации требуют исключения проникновения через пол сточных вод или других жидкостей, а также грунтовых вод, устраивают гидроизоляционный слой (или слои).
Устройство каждого из этих элементов пола требует удобоукладываемости применяемых материалов, определенных технологий, оборудования, а также профессионализма персонала. Все это вместе обеспечивает качественное выполнение работ. Стоимость работ по устройству пола составляет 10–15 % от стоимости возведения здания (при капитальном ремонте – до 30 % сметной стоимости) или 40 % от стоимости отделочных работ. [1, 2]
Часть I
Подготовка под покрытия полов
Глава 1
Бетонное основание
Самым важным этапом изготовления полов с различными видами покрытий является качественное изготовление бетонного основания (стяжки) под полы. Контроль качества подготовки поверхности бетона производится по ГОСТ 13015-2003, 12730.5-84*, 22690-88 и т. д.
Бетонное основание должно обеспечить такие важные показатели, как необходимую ровность, надежное сцепление с покрытием, а также исключить трещинообразование, связанное с усадкой бетона.
Одним из главных параметров, обеспечивающих качество пола, является его ровность.
Ровность бетонного основания напрямую зависит от технологии укладки, состава и однородности бетона, способа и ритмичности его доставки на объект, погодно-климатических факторов, обусловливающих образование воздушных потоков, резких температурных перепадов на месте производства работ.
В ряде случаев предъявляются повышенные требования к ровности поверхности пола. Это относится к складским помещениям, где используются узкопроходные штабелеры с большой высотой подъема грузов, например, при трехъярусном складировании. Здесь особенно важно получение "сверхровного" бетонного основания и покрытия.
Чтобы гарантировать такую ровность, необходимо обеспечить контроль всех процессов по устройству бетонного основания.
Первый этап контроля производится на этапе доставки бетонной смеси для ее укладки. Должна быть обеспечена бесперебойная ее доставка к месту укладки. Паузы не должны превышать 20–30 мин. Одновременно необходимо следить за качеством и однородностью бетона. Разница по осадке конуса (ОК) в смежных порциях, поставляемых на укладку, не должна превосходить 3–4 см.
Несоблюдение этих требований приводит к неравномерным осадкам и дополнительным работам и затратам, связанным с ликвидацией возможных дефектов, таких как неровности, появляющиеся на стыках уложенного в равных порциях бетона ("холодные" швы), а в дальнейшем к необходимости их фрезерования с целью выравнивания поверхности.
Следующий этап – укладка бетона. Укладка бетона может осуществляться как вручную, так и с помощью бетоноукладчика, как с направляющими, так и без направляющих. Устройство без направляющих позволяет укладывать бетон значительно быстрее, что важно, когда нет высоких требований к качеству и сжаты сроки строительства.
В качестве направляющих используются либо специальные бетонные изделия, либо металлические формы. Для полов с высокой ровностью должны использоваться только специальные формы с повышенной жесткостью и ровностью верхней кромки. Установка таких направляющих должна производиться только на жесткое основание и с обязательным использованием оптических или лазерных нивелиров.
Укладка вручную не дает высокой ровности укладываемой поверхности, т. к. контроль выполняют по жидким маякам, а разравнивание производят правилом либо виброрейкой типа Strike, Wacker или Magic Screed. Получаемая ровность пола при этом невысока, перепад может достигать 3–4 мм при контроле двухметровой рейкой. При машинной укладке бетона с контролирующей системой типа Laser Screed (компания "Конвинс") или бетоноукладчиком с лазерной системой автоматического управления Copperllcad XD (Ingri Flooring Technology, Somero) ровность выше, чем при ручной, однако и она не может обеспечить тех сверхвысоких требований, которые предъявляются к полам высотных складов.
Контроль ровности полов традиционно выполняется с помощью измерительной контрольной двух– или трехметровой рейки, уложенной в произвольном направлении. Определенный интерес представляют методы и средства контроля "сверхровных" полов, где максимальные величины перепадов составляют 1–2 мм на 1 м. Так, компания Likom предлагает методику и средство контроля ровности полов, разработанную в США, которая легла в основу стандарта ASTM 1155М (вариант, представленный в метрических единицах). Для измерения ровности используется прибор Face-F-meter компании Allen, который выдаст показатели FF и FL непосредственно после измерения. Точность измерений составляет 0,03 мм. Здесь параметр FF характеризует показатель неровности или волнистости пола, а FL – общий уклон пола. Для сверхплоских полов величины FF и FL должны быть выше 50.
При устройстве полов с "суперровностью" необходимо предусмотреть соответствующую технологию работ и систему контроля.
Бетоноукладочные комплексы с автоматизированными системами контроля позволяют существенно снизить долю трудозатрат на выравнивание и уплотнение бетонной смеси, однако не позволяют полностью отказаться от ручного труда при выравнивании поверхности. При ручном выравнивании используют различные рейки и виброрейки, деревянные, алюминиевые прямоугольного сечения или специальные заглаживающие профили с телескопическими ручками и поворотными шарнирами.
Бетон, приготовленный на основе портландцемента, характеризуется усадкой при твердении. Усадка бетона протекает в течение достаточно длительного периода времени. Особенно активная структуризация его происходит в течение первых трех месяцев. Для снижения усадки бетона и уменьшения трещинообразования применяется армирование или используется фибробетон, или прибегают к их комбинации, в зависимости от предполагаемых нагрузок на пол. Фибробетон – это смесь бетона со стальными волокнами длиной 30–50 мм и толщиной 0,5–3,0 мм. Их вводят в бетонную смесь на стадии перемешивания, равномерно распределяя в объеме, фибра равномерно армирует бетон во всех направлениях. Расход фибры на 1 м3 составляет 20–40 кг.
Большую роль в формировании прочностных и других свойств бетонного основания играет процесс уплотнения уложенного слоя смеси.
Перед уплотнением бетонная смесь распределяется по захваткам. Ширина захваток для "сверхплоских" полов не должна превышать 4–6 м, а их длина определяется дневной производительностью укладки. При этом необходимо избегать "холодных" швов в захватке, образующихся, как отмечалось ранее, из-за перерывов в бетонировании.
Смесь распределяется по захваткам и уплотняется с помощью различных виброреек и глубинных вибраторов. Последние применяются в случае укладки слоя повышенной толщины – свыше 150–200 мм. Уплотнение производят одинарными или двойными виброрейками. Жесткость их конструкции должна быть достаточно высокой, чтобы исключить их прогиб в процессе уплотнения бетона. Ровность уплотняющей поверхности реек должна проверяться и при необходимости регулироваться после каждой смены. При небольших объемах работ используют одинарные виброрейки, которыми управляют два человека: один тянет, стабилизируя их движение по направляющим, а другой осуществляет подготовительные работы, обеспечивая перед рейками валик бетонной смеси диаметром 10–20 мм. Глубина уплотнения при этом составляет 100–150 мм.
Вибрация, передаваемая бетонной среде от инструмента, по мере удаления от источника колебаний затухает, амплитуда уменьшается и снижается эффект уплотнения смеси. Эффект вибрирования, передачи колебаний уплотняемой среды тоже уменьшается, если вибрирующая плоскость рейки плохо контактирует с поверхностью бетона. С этой целью необходимо удерживать горизонтальную плоскость рейки, передающей колебания бетонной среде. Скорость протаскивания рейки не должна быть большой (до 0,5–1,0 м/мин), поскольку для хорошей проработки бетона, удаления из него вовлеченного воздуха необходимо время. Продолжительность вибрирования в минутах можно рассчитать по формуле:
t = с / n,
где с – число повторений приложения нагрузки, необходимое для доведения бетона до требуемой плотности, при этом с = 1,5–3x103; п – частота колебаний вибратора в минуту.
Поэтому для более качественной проработки бетона целесообразно выполнить два подхода: прямым и обратным ходом. Или надо использовать двойные рейки с регулируемыми параметрами вибратора. Они обеспечивают более качественное уплотнение до глубины 200 мм и позволяют получить ровную поверхность. Для уплотнения более толстых слоев (более 200 мм) совместно с виброрейками используют и глубинные вибраторы. Они позволяют не только уплотнять слои большой толщины, но и использовать бетон с меньшим содержанием воды. Вибрирование также улучшает сцепление бетона со стальной арматурой. При работе с двойной виброрейкой необходима бригада из трех или четырех человек. Двое тянут и управляют движением виброрейки, остальные лопатами обеспечивают требуемое количество бетона перед рейкой. Перемещение виброрейки следует выполнять плавно и непрерывно, следя за горизонтальностью положения ее вибрирующей плоскости. Нельзя останавливать движение рейки с работающим вибратором, а также останавливать ее сразу после выключения вибратора.
Перед началом затирки свежеуложенной бетонной смеси ее можно подвергнуть вакуумной обработке с помощью вакуумной установки типа Dynapac BA/BB, что обеспечит дополнительное уплотнение бетона за счет удаления излишков воды и воздуха. Установка состоит из вакуумного насоса (BA40), соединенного с многослойным матом (ВВ). Размеры матов составляют по площади от 1,5x5 до 5x6 м (всего 6 типоразмеров).
Отсасывающий мат выполнен в виде гибкого трехслойного ковра, в котором каждый слой имеет определенное назначение: нижний, из ткани, – фильтрует; средний, из объемной капроновой сетки, – создает капиллярность потока воды; верхний, из полимерной герметизирующей ткани со встроенным в средней части коллектором, – собирает и отводит воду. Подключается он к вакуум-агрегату гибким шлангом с помощью быстроразъемных соединений.
На поверхность уплотненного бетона накладывается отсасывающий мат и начинается вакуумная обработка, продолжительность которой зависит от толщины слоя бетонной массы, пластичности и состава смеси, величины разрежения и других факторов. При толщине бетонной смеси, например, 100 мм, она составляет 30–35 мин. Это определяет периодичность циклов.
После вакуумной обработки бетон становится достаточно жестким для окончательного заглаживания машиной, что и выполняется сразу же после снятия отсасывающего мата. При этом различаются две операции – грубая и чистая обработки.
Первая производится вращающимся со скоростью 60 об/мин круглым диском с целью подготовки поверхности к заглаживанию или получения готовой поверхности с качеством, удовлетворяющим требованиям для полов в гаражах, подвалах, складских помещениях и т. д.
Вторая выполняется радиально расположенными лопастями из высококачественной стали через 3–4 часа после первой, в результате чего поверхность становится идеально ровной и приобретает металлический блеск.
После проведения вакуумной обработки содержание воды в уплотненной бетонной смеси снижается на 20–30 %, водоцементное отношение в той же степени, что приводит к повышению предела прочности бетона при сжатии. Вакуумная обработка, эквивалентная 28-дневной выдержке в естественных условиях, достигается в среднем за 7 суток, что имеет существенное преимущество с точки зрения сдачи пола под эксплуатационные нагрузки. Практически готовый, он может использоваться на второй день после его укладки.
Установлено, что прочность отвакуумированного бетона превышает прочность обычного в возрасте 3 суток в среднем на 84 %, в возрасте 7 суток в среднем на 47 %; 14 суток – на 41 % и 28 суток – на 37 %. Кроме того, смесь в процессе обработки дополнительно уплотняется нагрузкой 6–7 т/м2 за счет атмосферного давления. Поэтому бетон образуется с более плотной структурой и повышенной объемной массой. Объемная масса отвакуумированного бетона в возрасте 28 суток выше обычного по абсолютной величине на 60–80 кг/м3.
Для создания необходимой адгезии, надежного сцепления покрытия с основанием при любом типе покрытия требуется определенная шероховатость поверхности.
Наиболее эффективным способом, обеспечивающим надежную адгезию и шероховатость поверхности, является дробеструйная обработка. Она дает равномерную шероховатость поверхности, увеличивает площадь сцепления, удаляет пленку цементного "молока" и обнажает зерна заполнителя, повышая сцепные качества бетонной поверхности. Для определения сцепных качеств бетонной поверхности можно использовать прибор "ПОКС", предназначенный для определения сцепных качеств различных поверхностей. Прибор прост в конструкции и применении, не требует источника питания и в течение нескольких секунд определяет коэффициент трения в измеряемой точке поверхности.
В ряде случаев возникает необходимость определить пористость бетонной поверхности. Для этих целей можно использовать выпускаемый прибор для определения пористости покрытий – "ПР-10", который также обладает простотой конструкции, отсутствием источников питания, пересчетных устройств и в течение нескольких секунд определяет пористость контролируемой поверхности. Такая информация поможет качественно выполнить работы, связанные с окраской бетонных поверхностей, нанесением грунтовки (праймера), обнаружением трещин для дальнейшей их обработки, нанесения слоя цветного защитно-декоративного покрытия и т. п. [2, 3]
В НИИЖБ (Москва) была разработана железобетонная плита (рис. 1.1) для устройства основания пола на слабых и промороженных грунтах на нагрузки до 8 т/м2.

Рис. 1.1. Железобетонная плита для устройства основания пола на слабых и промороженных грунтах
Плита армирована легкой арматурной сеткой и предварительно напряженной канатной арматурой без сцепления арматуры с бетоном. Натяжение канатной арматуры производится на затвердевший бетон гидравлическими домкратами.
Благодаря особенностям конструкции, плита имеет непревзойденные показатели материалоемкости при высоких эксплуатационных характеристиках: толщина бетона – 120 мм, расход ненапрягаемой арматуры – 3 кг/м2, расход канатной арматуры – 1,5 кг/м2.
Плита пола, предлагаемая фирмой "Практик", может быть основанием для устройства "чистых" полов из керамической плитки, полимерных полов. Возможен вариант, предлагаемый фирмой "Практик", плиты как плиты "чистого" пола с одновременной затиркой поверхности бетоноотделочными машинами с применением "топпингов" или без них.
Первое внедрение этой конструкции плиты пола состоялось в торговом комплексе "Карусель" на пр. Жукова в Санкт-Петербурге.
Плита была выполнена на площади 8000 м2, точность поверхности плиты после затирки 1–2 мм. Благодаря предварительно напряженной арматуре при устройстве плиты пола не требовалось виброуплотнение грунтового основания. [4]
Глава 2
Стяжки
Стяжка является обязательным элементом практически каждого пола и представляет собой слой, образующий жесткую, плотную, ровную корку по неровным элементам перекрытия (основания).
Анализ данных по разрушению конструкций полов показал, что в подавляющем большинстве случаев причиной выхода пола из строя является некачественное состояние стяжки: наличие в верхнем слое ослабленной зоны, высокая влажность, низкая адгезия материала стяжки к смежным элементам пола. Среди всех нагрузок, воспринимаемых полом (механических, тепловых, агрессивных, химических и др.), в наибольшей степени влияют на его долговечность механические ударные воздействия. Для обеспечения высокой долговечности пола необходимо, чтобы стяжка была сухой, имела прочную и ровную поверхность, обладала высокой адгезией к смежным элементам пола. Весьма желательным является требование к материалу стяжки иметь высокую технологичность, под которой понимается максимально полная механизация работ по ее приготовлению и укладке, отсутствие операций по разравниванию и шлифовке поверхности и т. п. [5]
Используют стяжки сплошные и сборные.
Сплошные стяжки обычно устраиваются из цементно-песчаного раствора марки не менее 150, а также из бетона (керамзитобетона, шлакобетона и др.). Применяют ксилолитовые и асфальтобетонные стяжки. При устройстве стяжек из бетонов и растворов на основе портландцемента следует учитывать, что для твердения этих материалов необходимы влажные условия. Поэтому в течение 7—10 суток после укладки стяжка требует специального ухода. Такие стяжки для нашего строительства традиционны, однако трудоемки и нетехнологичны.
Применение специальных сухих смесей заводского изготовления на различных минеральных вяжущих, модифицированных полимерными добавками, позволяет упростить и значительно ускорить устройство стяжек. Все более широкое применение находят самовыравнивающиеся композиции, при затворении которых образуется подвижная смесь, растекающаяся под собственным весом. Заданная толщина покрытия достигается при помощи простейшего ручного инструмента. Для устройства наливных стяжек, наряду с импортными сухими смесями, такими как Ветонит, Атлас, Сопро и др., производятся высококачественные отечественные смеси "Опытного завода сухих смесей" на основе цемента, смеси ТИГИ Кнауф на гипсовой и цементной основе, стяжки Маглит-1 фирмы "БиКам" на магнезиальном вяжущем.
Перспективны стяжки, совмещающие в себе функции теплозвукоизоляционного или гидроизоляционного слоя. Основной недостаток сплошных монолитных стяжек – необходимость выдержки их для набора прочности и удаления влаги перед укладкой лицевого покрытия, что удлиняет сроки проведения работ, а несоблюдение этих требований приводит к браку.
Сборные стяжки монтируются из крупноразмерных листов и плит – фанеры, ДСП и ДВП, гипсоволокнистых листов (ГВЛ). Масса элементов сборных стяжек невелика, что позволяет одному человеку справиться с монтажом. Применение сборных стяжек исключает «мокрые» процессы, поэтому можно практически сразу приступать к укладке лицевого покрытия. Однако использование сборных стяжек возможно не для всех видов лицевых покрытий.
Правообладателям!
Это произведение, предположительно, находится в статусе 'public domain'. Если это не так и размещение материала нарушает чьи-либо права, то сообщите нам об этом.