Текст книги "Благоустройство территории вокруг коттеджа"
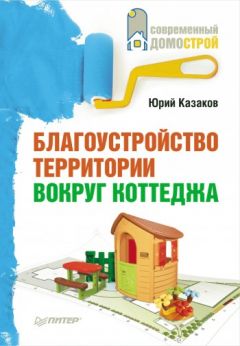
Автор книги: Юрий Казаков
Жанр: Хобби и Ремесла, Дом и Семья
сообщить о неприемлемом содержимом
Текущая страница: 4 (всего у книги 14 страниц) [доступный отрывок для чтения: 5 страниц]
Благоустройство границ участка
Ограждение участка можно выполнить в виде живой изгороди, высадив один или несколько рядов кустарника и, при желании, деревьев, либо в виде забора из древесины, сборных железобетонных элементов, металлических секций, кирпича (рис. 3.6).

Рис. 3.6. Живая изгородь
Устройство живой изгороди начинают с высадки одного ряда кустарника в заранее подготовленные траншеи шириной и глубиной не менее 60 см. Для каждого последующего ряда кустарника необходимо увеличивать ширину траншей на 25 см. В состав многорядной живой изгороди могут быть включены деревья, а также заполнения из проволоки на стойках. Подробнее об устройстве живых изгородей читайте в разделе «Озеленение участка».
Постоянные и временные ограды устанавливают с учетом технологических требований. Осевые линии ограды закрепляют на местности установкой створных знаков, долговременность которых определяется исходя из конкретных условий стройки. Траншея под цоколь ограды должна быть открыта механизированным способом с запасом по ширине до 10 см в обе стороны от оси и на 10 см глубже, чем отметка положения низа цоколя (для устройства дренирующего слоя). Длину захватки открываемой траншеи устанавливают с учетом осыпания грунта ее стенок. Ямы под стойки ограды следует бурить на 10 см глубже, чем глубина установки стоек. Это позволит установить верх стоек по одной горизонтальной линии на возможно больших по длине участках, устроить дренирующую подушку и исключить необходимость ручной подчистки дна ямы. Глубина ям зависит от качества грунта: в глинах и суглинках она должна быть не менее 80 см, а в песках и супесях – не менее 1 м.
Дренирующий материал в ямах и траншеях должен быть уплотнен. Песок уплотняется поливом, гравий и щебень – трамбованием до состояния, при котором прекращается подвижка щебня и гравия под воздействием уплотняющих средств. В песчаных и супесчаных грунтах дренирующие подушки под цоколи и стойки оград не делаются.
Ограды на стойках, устанавливаемых без бетонирования подземной части, следует устраивать сразу после установки стоек. Ограды на железобетонных или металлических стойках, устанавливаемых с бетонированием подземной части, следует устраивать не ранее чем через две недели после бетонирования низа стоек.
Деревянные стойки для оград должны иметь диаметр не менее 15 см и длину не менее 2,5 м. Погружаемая в землю часть стойки не менее чем на 1 м обмазывается разогретым битумом или обжигается на костре до образования угольного слоя. Эти меры позволят предохранить дерево от загнивания. Верхняя часть стойки должна быть заострена под углом 120°.
Стойки без башмаков следует устанавливать в ямы диаметром 30 см и засыпать смесью грунта и щебня или гравия. В процессе засыпки материалы послойно утрамбовываются. На уровне поверхности земли стойку необходимо обсыпать конусом из грунта высотой до 5 см.
Стойки, укрепляемые в грунте посредством бетонирования подземной части, следует бетонировать только после выверки их положения по вертикали и в плане. Максимальное отклонение стоек в обоих случаях – 10 мм.
Возведение оград из проволоки, натягиваемой на стойки, начинают с установки угловых диагональных и крестовых связей между стойками. Крестовые связи устанавливаются не более чем через 50 м.
Диагональные и крестовые связи должны быть врублены в стойки, плотно пригнаны и закреплены скобами. Связи врубают в стойки на глубину 2 см с притеской и припиливанием плоскостей соприкосновения до плотного их прилегания. Скобы забивают перпендикулярно оси связующего элемента. В верхней части стойки связи срезают на высоте не менее 20 см от начала заострения, а в нижней части – не более 20 см от поверхности земли.
Проволоку прикрепляют, начиная с нижнего ряда, на высоте не более 20 см от поверхности земли. К деревянным стойкам проволоку крепят гвоздями. К железобетонным и металлическим стойкам проволоку, диагональные и крестовые связи прикрепляют специальными захватами, предусматриваемыми в проекте. Проволоку натягивают до исчезновения прогиба. Длина натягиваемой проволоки должна быть не более 50 м.
Ограды из стальной сетки выполняют в виде секций, устанавливаемых между стойками (рис. 3.7). Секции к стойкам крепят приваркой к закладным частям. Стойки для оград из стальной сетки могут устанавливаться заранее или одновременно с монтажом секций. В последнем случае закреплять стойки в грунте следует после выверки положения ограды в плане и в профиле, стоек – по вертикали, а верха секций – по горизонтали. Металлические и железобетонные стойки укрепляют при помощи бетона.
Сооружение оград из сборных железобетонных элементов начинают с установки первых двух стоек на временных креплениях, удерживающих стойки в вертикальном положении. В стойках прочищают пазы и в них вводят сборные элементы ограды. Собранную секцию устанавливают на временных креплениях в проектное положение. После этого панель заполнения секции следует обжать монтажными струбцинами до плотного прилегания к стойкам в пазах. Затем на временных креплениях устанавливают третью стойку и аналогично собирают и крепят заполнение второй секции ограды. После монтажа нескольких секций следует выверить положение ограды в плане и по горизонтали и забетонировать все стойки, кроме последней, которую бетонируют после сборки и выверки положения последующих нескольких секций ограды. Стойки сборной железобетонной ограды должны быть забетонированы и выдержаны на временных креплениях не менее одной недели. Бетон для крепления стоек должен иметь класс не ниже В 15 и морозостойкость не менее 50 циклов.

Рис. 3.7. Стальная ограда
В местах понижения дневной поверхности земли и на наклонной поверхности устраивают подсыпки или доборные цоколи, располагая секции горизонтально, уступами с разницей высот не более 1/4 высоты секции. Цоколи выполняют из типовых элементов или из кирпича шириной не менее 39 см. Верх кирпичного цоколя должен быть прикрыт двускатным сливом из раствора марки не ниже 150 и морозостойкостью не менее 50 циклов.
При строительстве оград на вечномерзлых грунтах необходимо обеспечивать заглубление стоек не менее чем на 1 м ниже деятельного слоя вечной мерзлоты. Допускается засыпка стоек несвязными грунтами или обмазка низа стоек противопучинной гидроизоляционной смазкой на всю глубину погружения в грунт.
Приемку ограды следует осуществлять путем проверки ее прямолинейности и вертикальности. Не допускаются отклонения в положении всей ограды и отдельных ее элементов в плане, по вертикали и по горизонтали более чем на 15 мм, а также наличие дефектов, сказывающихся на эстетическом восприятии ограды или на ее прочности. Диагональные и крестовые связи следует плотно пригнать и надежно закрепить. Стойки оград не должны качаться. Кроме того, нужно, чтобы сборные элементы оград плотно сидели в пазах. Металлические элементы оград и сварные соединения необходимо прокрасить атмосферостойкими красками.
Глава 4
Хозяйственные постройки на участке
Технологии возведения хозяйственных построек
Существуют четыре основные технологии возведения надворных хозяйственных построек. Так, самые необходимые постройки – гараж и баня – чаще всего сооружаются из монолитного бетона, легких металлоконструкций, полимерных материалов либо из панелей поэлементной сборки («сэндвич»). Все названные технологии имеют свои особенности, плюсы и минусы. Предлагаем ознакомиться с каждой из них, а затем выбрать ту, которая наиболее подойдет именно вам.
Вариант 1.Монолитное и сборно-монолитное возведение гаража и бани
Коротко процесс строительства из монолитного бетона и железобетона можно описать так: прямо на стройплощадке монтируются специальные формы (опалубки), которые повторяют контуры каждого из элементов будущего здания. В опалубки в соответствии с проектом устанавливается каркас из арматуры и заливается бетон. Выдерживается время, необходимое для застывания бетона, затем, если это нужно, опалубки снимают (помимо сборно-разборных, существуют несъемные опалубки, которые не требуют распалубливания).
Степень трудоемкости этих четырех процессов соотносится таким образом: устройство опалубки – 25-35 %, армирование – 15-25 %, бетонирование и уход за бетоном – 20-30 %, распалубливание – 20-30 %.
Аргументы в пользу технологии монолитного бетонирования приводят и строители, и заказчики. Наиболее часто она применяется при возведении комбинированных конструктивных систем – зданий с монолитным каркасом и внешними стенами, выполненными из штучных материалов. Что касается возведения фундаментов, подземных частей построек, пространственных конструкций и строительства в районах с повышенной сейсмической активностью, здесь, пожалуй, монолитное домостроение вне конкуренции.
Перечислим главные преимущества монолитного строительства.
Эта технология дает возможность создавать свободные планировки с большими пролетами за счет перехода к неразрезным пространственным системам и самые разнообразные криволинейные формы. Иными словами, она позволяет воплотить в жизнь практически любые архитектурные проекты.
Монолитные конструкции, как видно из названия, почти бесшовные. Следовательно, они имеют высокий уровень теплотехнических, изоляционных свойств, не нуждаются в герметизации стыков. Если сравнить такие конструкции со сборными железобетонными конструкциями, можно проследить такую экономию: расход стали снижается на 7-20 %, а бетона – до 15 %.
Однако даже с учетом этих достоинств описанная технология не является идеальной. Так, к ее недостаткам можно отнести тот факт, что производственный цикл осуществляется под открытым небом. На производство конструктивных элементов воздействуют дождь, снег, жара и т. д. Но особенно негативно на нем сказываются низкие температуры, являющиеся причиной замерзания воды, происходящего в начальный период застывания бетона, и остановки реакции гидратации. При переходе в лед вода увеличивается в объеме примерно на 9 %. Возникает внутреннее давление, которое разрушает структуру бетона, не успевшего набрать необходимую прочность. Кроме того, образуется ледяная пленка на поверхности фракций заполнителя (щебня), что препятствует уплотнению структуры даже после оттаивания. При плюсовых температурах вода возвращается в жидкое состояние и процесс гидратации цемента возобновляется, но нарушенные структурные связи в бетоне в полном объеме уже не восстанавливаются. В итоге бетон, который подвергался «заморозке», примерно на 20 % менее прочен, чем предусмотрено проектом, он теряет плотность, водонепроницаемость, морозостойкость. Уменьшается и срок его службы. Правда, вышеописанный процесс не повлияет на качество бетона, если он успеет набрать достаточную начальную прочность до замораживания. Следовательно, первостепенная задача строителей, выполняющих бетонные работы в зимний период, – максимально сократить сроки набора бетоном начальной прочности и обеспечить оптимальные температурные условия его выдерживания. Выполнить эти условия можно, если соблюдать некоторые требования.
В холодный период необходимо применять бетонные смеси на быстротвердеющих и высокоактивных цементах и с водоцементным отношением не более 0,5. В некоторых случаях положительный эффект можно получить, повысив марку цемента и увеличив его расход. Перед приготовлением воду и остальные компоненты следует подогреть. Основание, на которое планируется укладывать бетон, нуждается в подготовке. И наконец, свои особенности имеет процесс распалубливания: при снятии опалубки соприкасающийся с ней слой бетона должен иметь температуру не ниже +5 °С.
Кроме того, существуют специфические методы зимнего бетонирования и их комплексы, которые могут применяться при наличии технико-экономического обоснования.
Метод термоса заключается в подогреве воды и заполнителей либо готовой смеси. При их остывании выделяется теплота, и в результате подогрев опалубки уже не требуется, поскольку бетон быстро набирает заданную прочность. Метод достаточно экономичен и допускает использование добавок, ускоряющих процесс затвердения. Часто применяется для масштабных конструкций.
Применение противоморозных добавок. Специальные добавки, вводимые в бетонную смесь в момент ее приготовления, способны снизить температуру замерзания воды. Трудоемкость этого метода минимальна, но следует учитывать, что добавки увеличивают время, необходимое для набора бетоном критической прочности.
Электропрогрев бетона. Суть данного метода, одного из самых распространенных, заключается в том, что в тело конструкции вводятся электрические провода или электроды. Это позволяет поднять температуру свежеуложенной смеси до максимально допустимого уровня и поддерживать ее на протяжении времени, необходимого для достижения бетоном критической прочности. В таких условиях процесс твердения идет очень быстро.
Конвективный прогрев бетона. Свежеуложенная смесь прогревается через воздушный слой. Для этого используются электрокалориферы либо тепловые пушки. Метод отличается низким уровнем трудовых затрат, но может быть применен только в помещении.
Греющая опалубка отличается от обычной тем, что она оснащена нагревательными элементами, в качестве которых могут использоваться провода, ленты и т. п. В греющую опалубку может быть переоборудована любая обычная.
Вариант 2.Быстровозводимые гаражи и бани (полнокомплектные) из легких металлоконструкций
На современном этапе технология строительства быстровозводимых зданий из легких металлоконструкций весьма распространена. Главный ее секрет заключается в использовании такого качества металла, как высокая теплопроводность. Специальные конструкции из стали (так называемые термопрофили) с минимальным поперечным сечением и сквозными бороздками, прорезанными в шахматном порядке, увеличивают путь прохождения теплового потока. Это дает возможность при уменьшении несущей способности примерно на 10 % уменьшить теплопроводность на 80-90 % (в зависимости от типа профиля). В итоге конструкция по тепловым параметрам не уступает деревянной.
В строительстве быстровозводимых зданий используются также внутренние стеновые профили, имеющие улучшенные виброакустические характеристики, стальная обрешетка, металлические стропила или фермы и т. д. Все стальные элементы конструкции оцинкованы, и это значительно увеличивает срок их эксплуатации, исключает коррозийные процессы.
Конструкция стены при данной технологии имеет следующее строение:
♦ каркас из стальных перфорированных профилей (термопрофилей);
♦ внутренняя обшивка из гипсокартонных листов, цементно-стружечных плит или других материалов;
♦ слой пароизоляции;
♦ слой теплоизоляции (в большинстве случаев это минераловатные плиты, располагаемые в полости каркаса);
♦ внешняя обшивка из гипсокартонных листов и защитно-декоративного слоя.
Наружный, защитно-декоративный, слой зданий из легких металлоконструкций выполняется по принципу «вентилируемого фасада» и допускает большое разнообразие в выборе материалов. Так, в качестве облицовки можно применять кирпич или плиты, его имитирующие, деревянную вагонку, сайдинг, профлисты, имеющие полимерное покрытие, фасадные кассеты и т. д. Ветрозащитным барьером служат плиты из гипсокартона, древесных волокон или других материалов со сходными качествами.
Профили, составляющие каркас конструкции, могут иметь разную ширину. Это зависит от толщины утеплителя, которая должна быть достаточной для того, чтобы удовлетворять требованиям СНиП, регулирующим теплоизоляцию жилых зданий.
Качественный монтаж зданий из легких металлоконструкций дает возможность получить высокий показатель влажностного режима. Главное условие – не допускать образования полостей и зазоров в местах соприкосновения изоляции и поверхности плит, в углах плит. Ветрозащитные плиты должны быть выполнены с минимально возможным количеством швов. Достаточную пароизоляцию позволяют обеспечить аккуратное ведение работ и соблюдение инструкций по настилу пароизоляционной пленки под гипсокартонные плиты. Поскольку температура на поверхностях внутренних стен в месте профилей достаточно высока, конденсат на них не образуется, как и на поверхности парозащитной пленки.
Есть два варианта монтажа стен из легких металлоконструкций. Иногда стены собираются непосредственно на фундаменте, но чаще применяется другая технология: заготовки делаются в виде панелей на строительной площадке, специально отведенном участке или в заводских условиях и потом монтируются. Если возникает необходимость, то возможна подгонка панелей в процессе сборки конструкции, но обычно она не требуется, так как все стальные профили проходят обрезку по размеру на заводе в соответствии со спецификацией. Такой способ ведения работ позволяет значительно сократить сроки строительства и не требует применения тяжелой грузовой техники, поскольку даже готовые панели довольно легки.
Таким образом, эта технология имеет достаточно преимуществ, дающих возможность использовать ее при возведении надворных хозяйственных построек. Перечислим их еще раз.
Итак, сооружение быстровозводимых зданий из легких металлоконструкций позволяет:
♦ сократить сроки строительства за счет применения готовых заводских элементов;
♦ закупить все элементы в комплексе;
♦ не использовать тяжелые грузоподъемные механизмы и не устраивать фундаменты глубокого заложения, поскольку детали имеют малый вес;
♦ снизить трудовые затраты, так как монтаж элементов очень прост;
♦ исключить «мокрые» процессы;
♦ реализовать свободную планировку внутренних помещений постройки и разнообразные решения фасада;
♦ подготовить внутреннюю поверхность стен под чистовую отделку;
♦ сэкономить на электроэнергии;
♦ получить в результате экологически безопасную, пожаробезопасную, долговечную постройку.
Следует отметить, что эта технология применяется не только в малоэтажном домостроении.
Вариант 3.«Сэндвич» для возведения гаража и бани
Панели поэлементной сборки не зря получили название «сэндвич». Это слово в достаточной мере отражает строение ограждающей конструкции: закрепленная на несущем каркасе постройки кассета + вставляемый в нее утеплитель (чаще всего – минеральная вата) + ветровой барьер + облицовка. Последняя может выполняться из металлического сайдинга, профилированных плит, кассет.
Местонахождение кассеты в конструкции и тип нагрузки (давление, всасывание) определяются предъявляемыми к этому элементу требованиями. Выполненная из оцинкованной стали (иногда – с покрытием из полимерного материала), кассета должна обладать высоким уровнем прочности, усталостной прочности, огнеупорности. Последнее качество обеспечивается ячеистой структурой кассет. Выбирая глубину фасадных кассет, следует ориентироваться на толщину теплоизоляции, которая будет в нее закладываться. Обычно толщина теплоизоляционного слоя колеблется от 10 до 20 см в зависимости от требований к теплосбережению конструкции.
Монтаж панелей поэлементной сборки осуществляется в следующем порядке в семь этапов.
1. Кассета закрепляется за оба края к стойке каркаса как минимум тремя фиксирующими деталями и крепится над цоколем здания. Способы укрепления могут быть различными с учетом ситуации. В это же время в месте стыка кассеты и каркаса устанавливается уплотнительная лента.
2. Стыки между кассетами закрываются. Для этого используются два уплотнителя из искусственного каучука (EPDM) или составы для уплотнения швов.
3. На верхний край каждой кассеты устанавливается следующая кассета, они скрепляются шурупами.
4. Прикрепленные к каркасу и загерметизированные кассеты заполняются утеплителем.
5. Устанавливается ветровой барьер.
6. В соответствии с особенностями материала облицовки ставятся опорные прогоны с целью создания зазора между ветровым барьером и внешней облицовкой. Промежуток необходим для циркуляции воздуха и вентиляции всей конструкции. Нормальное проветривание обеспечивает зазор шириной не менее 2 см.
7. Выполняется наружная облицовка постройки в соответствии с особенностями материала.
Вариант 4.Надворные постройки из полимерных материалов
При грамотном применении полимерные материалы вполне заменяют стекло практически в любых конструкциях и позволяют реализовать весьма разнообразные и оригинальные проекты.
Первый из полимеров, который стали активно использовать в строительстве, – это органическое стекло (акрил), точнее, его монолитные листы. Данный материал прекрасно поддается горячему формованию, прозрачен, устойчив к большим механическим нагрузкам и хорошо пропускает ультрафиолетовые лучи.
Существует также структурированное оргстекло, которое, благодаря наполненным воздухом каналам внутри, имеет ряд преимуществ. Такие листы на порядок легче монолитных, имеют более высокий уровень теплоизоляционных свойств и конструктивной прочности.
Особыми характеристиками обладает полимерный материал, изобретенный позже, – поликарбонат. В сравнении с акрилом этот полимер выигрывает, поскольку способен выдерживать, не изменяя свойств, огромную амплитуду температур: от -45 до +120 °С. Кроме того, ударная стойкость поликарбоната выше аналогичного показателя стекла в 100 раз и акрила – в 10 раз.
Так же, как и акрил, поликарбонат бывает двух видов: монолитные плиты и структурированные плиты. Каждый из этих видов занимает в строительстве свою нишу и позволяет решать специфические задачи.
Так, монолитные поликарбонатные плиты, несмотря на относительную дороговизну, очень часто применяются в изготовлении элементов криволинейных форм, поскольку отлично поддаются горячему формованию. Современные модификации монолитных плит из поликарбоната, оснащенные ребрами жесткости, дают возможность изготавливать самонесущие перекрытия без использования металлического каркаса. Такие конструкции обладают высоким уровнем пароизоляции.
Структурированные поликарбонатные плиты имеют ячеистую структуру. Чаще всего применяются в изготовлении элементов горизонтального или арочного типа – крыш, навесов, арочных перекрытий и т. д.
В строительстве также используются полимерные материалы из ПВХ (рис. 4.1).

Рис. 4.1.
ПВХ-листы
На российском рынке представлены полимерные листы толщиной 4, 6, 8, 10, 16 и 25 мм. Существуют также панели толщиной 32 мм, но в нашей стране они пока еще редкость. Стандартные горизонтальные размеры панелей: ширина – 2100 мм, длина – 6000 или 12 000 мм, хотя некоторые фирмы готовы варьировать эти параметры в соответствии с желанием заказчика.
Выбирая панели, учитывайте, что самые тонкие из них (толщиной 4 и 6 мм) не годятся для наружных конструкций, поскольку плохо выдерживают снеговые и ветровые нагрузки. Для применения в архитектурных целях оптимальны материалы толщиной от 8 до 16 мм; наиболее толстые позволяют обеспечить высокий уровень теплоизоляции.
О качествах полимеров, делающих их незаменимыми в изготовлении теплиц и парников, читайте в следующем разделе книги.
Полимерные плиты различных производителей могут существенно различаться. Наиболее крупные изготовители постоянно совершенствуют технологию производства, представляют на рынке модификации с дополнительными возможностями за счет особого состава, систем крепления и т. д.
Подведем итоги всего вышесказанного. Несомненными плюсами полимерных материалов можно назвать:
♦ малый удельный вес (от 1,5 до 3,5 кг/м2), дающий возможность проектировать легкие конструкции с большим количеством дизайнерских возможностей и удешевляющий покрытие;
♦ высокие теплоизоляционные свойства (коэффициент приведенного сопротивления теплопередаче составляет примерно 0,36-0,57 м2 • С/Вт);
♦ высокую ударную прочность;
♦ высокую несущую способность (до 250 кг/м2 при шаге обрешетки 1-2 м), сохраняемую при температуре от -40 до +120 °С;
♦ прозрачность;
♦ пластичность, позволяющую изготавливать арочные перекрытия;
♦ высокую химическую стойкость;
♦ долговечность (гарантированный срок службы – 10-12 лет);
♦ огнеупорность.
Стоит сказать и о недостатках полимерных материалов. Их пластичность, являющаяся несомненным достоинством, требует, однако, пристального внимания к техническим решениям, особенно в покрытиях, имеющих плоскую форму и большую площадь, так как температурное расширение у полимеров выше, чем у материалов конструкций. Следует опасаться и механических повреждений, к которым склонны полимеры. Здесь, правда, на помощь приходят специальные покрытия, которыми можно обработать поверхность. Еще один вариант решения проблемы – сохранение заводской защитной пленки на панелях до завершения монтажа конструкции.
Правообладателям!
Данное произведение размещено по согласованию с ООО "ЛитРес" (20% исходного текста). Если размещение книги нарушает чьи-либо права, то сообщите об этом.Читателям!
Оплатили, но не знаете что делать дальше?