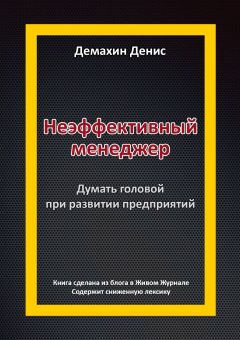
Автор книги: Денис Демахин
Жанр: Руководства, Справочники
Возрастные ограничения: +18
сообщить о неприемлемом содержимом
Текущая страница: 13 (всего у книги 17 страниц)
1. Главное – чтобы мне было удобно работать
Данная фраза – это уступка агитаторов за бережливое производство, чтобы втянуть в эту деятельность персонал. Но потом это становится мантрой, которой этот же самый персонал будет прикрываться вечно, тормозя развитие бережливки.
Фраза очень популярна при внедрении системы 5S. Но покажите мне хоть одного человека в мире, с любым, каким угодно бардаком на рабочем месте, который не считал бы, что ему так удобно. Так, как ему удобно, мы и так видим до того, как начали что-то внедрять.
Главное – это как удобно бизнесу, а вовсе не сотруднику. Хорошо, когда это совпадает. А когда не совпадает – приоритет за бизнесом.
Примеры, когда сотруднику неудобно, а бизнесу удобно:
– Стандартизация. Это снижает незаменимость сотрудника, и ему лично почти ничем не помогает.
– Порядок в файлах. Сотрудник и в беспорядке найдет свои файлы. Если получится чуть дольше – ну что ж, такова судьба. Но зато без него никто больше в них не разберется, а значит его не уволят.
– Оптимизация процессов между отделами. Сотруднику удобно занять позицию «моя хата с краю», и наплевать, как будут мучаться в других отделах.
На Тойоте стандарты выполнения рабочих операций на конвейере сделаны для проверяющего или для начальника, а вовсе не для рабочего. Рабочий и так наизусть помнит, как что делать, он туда и не смотрит. Но стандарт нужен, чтобы любой мог подойти и проверить, всё ли правильно выполняет рабочий.
2. Деление рабочих операций на 3 категории
– Создающие ценность;
– Необходимые, но не создающие ценность;
– Потери.
И в зависимости от этой классификации поступаем с ними так:
– Создающие ценность – операции нужны. В идеале весь рабочий процесс должен состоять только из таких операций.
– Необходимая, но не создающая ценность работа должна быть максимально сокращена.
– Потери должны быть устранены.
Данная нехитрая система – это криво понятая концепция от Тайити Оно.
Что с этим не так
А с чего взяли, что операции, создающие ценность, не нужно сокращать? Они же тоже должны занимать всё меньше и меньше времени! А мы по этой методике просто проходим мимо них и никак не воздействуем.
А если воздействуем, то чем тогда они эти операции отличаются от не создающих ценность и чем от потерь? А если ничем, то зачем тогда эта классификация?
Любую операцию нужно постараться устранить или максимально уменьшить! Полезную операцию тоже нужно устранить!!! Например, заменив более прогрессивным методом. Или повысить интенсивность. Принцип ТРИЗ: устройства (операции) нет, а процесс выполняется.
Иногда какую-то не создающую ценность операцию нужно чуть увеличить, чтобы суметь из-за этого сильно уменьшить другую операцию, и тогда суммарная длительность должна снизиться. Но на моей памяти неукоснительное стремление исполнять эту бережливую парадигму мешало так сделать.
Однажды я хотел немного добавить работы (добавить небольшую операцию в цикл) сотруднику, создающему ценность, чтобы решить много проблем, которые возникали у сотрудника, который ценность не создавал. И мне не дали этого сделать, т.к. сотрудник, создающий ценность – (якобы) важнее. Почему? Непонятно. И тот и тот получают зарплату. И тот и тот делает свое дело.
Я признаю, что польза от такого разделения может быть только на самом первоначальном этапе обучения специалиста. Чтобы рассказать принцип, основы. Но в реальной работе нужно эту концепцию отбросить, аннулировать.
Моя парадигма вместо этой, ошибочной: сокращать длительность всех операций. Поэтому классификация не нужна.
3. Деление персонала на тот, который приносит ценность, и на вспомогательный
Это больше похоже на дискриминацию. Если эти рабочие места на предприятии есть, то значит у них есть функция. Иначе зачем их создавали? Почему не расформируют? Допустим, оператор отдела планирования не создает ценность. И что из этого? Осознание этого чем-то помогает нам?
Также много пользы можно принести (нет) постоянно напоминая, что вы, сударь / сударыня, не создаете ценность.
Эта недо-концепция доводит даже до таких разговоров, что на доску почета предприятия надо помещать только тех, кто приносит ценность.
Только вот вопрос: делает ли это обстоятельство сотрудника бесполезным? Что-то наталкивает на мысль, что если оставить в компании только те штатные единицы, которые создают ценность, то это будет катастрофа. Это могут себе позволить только мелкие шараш-монтаж производства.
Однажды я проводил бенчмаркинг-сессию, и один из гостей у меня спросил, сколько у нас рабочих, и сколько всех остальных. Я ответил, что рабочих где-то 200, а всех остальных 400, и в сумме всех 600.
И тогда он сказал насмешливо:
– Это что значит, 200 человек ценность создают, а остальные 400 её кушают?
Вы когда-нибудь получали нокаут от невыносимого идиотизма? Когда вы теряете дар речи и перед глазами только красная пелена? Вот у меня как раз такое и случилось.
Не важна численность тех и этих. Важна только прибыль! Только себестоимость! Каким бы способом она ни достигалась.
Допустим, на предприятии есть автоматическая линия, на ней 3 рабочих создают ценность. А все остальные 50 сотрудников ценность не создают. Они занимаются охраной труда, кадровой работой, продажами, закупками, уборкой. И что с того?
Моя парадигма вместо этой, ошибочной: не делить сотрудников на касты. Добиваться финансового результата компании, а не процентного соотношения количества сотрудников по признаку создания ценности.
4. Деление логистических потоков на прямые, обратные и пересекающиеся
Я давно потерял счёт количеству планировок технологических линий, которые разработал. При их проектировании нужно понимать, как изделие будет двигаться.
Если потоки движения изделий будут пересекаться, то они будут мешать друг другу, создавать ДТП, создавать пробки. Но если изделие проходит по потоку раз в час, то они никогда друг другу не помешают.
Если потоки движения изделий будут делать возвратные петли, а не только двигаться вперед, то изделие будет проделывать лишний путь. Поэтому назад ничего двигаться не должно.
Однажды я проектировал технологическую линию, в которой был какой-то такой кусок:
И я никак не мог ее согласовать, т.к. тут были возвратные потоки, которые я показал красным (также отмечено цифрами 1).

И мне пришлось сделать так, чтобы согласовать её:

Я просто потратил больше площади, а длина пути не изменилась. Зато нет возвратных потоков. Вторая планировка явно хуже.
Моя парадигма вместо этой, ошибочной: логистические потоки должны быть как можно короче и проще. С минимизацией занимаемой площади.
Формулировка «как можно» подразумевает оптимальность и компромиссы, а не выполнение жестких правил.
5. Сдельная система оплаты труда – зло!
Фанатичные бережливцы шарахаются от сдельщины как черт от ладана потому что в японских книжках написано, что это главный враг бережливого производства. Но всё это от непонимания сути.
Японцы писали сугубо ПРО СЕБЯ. На их конвейерах это действительно было зло. Потому что ЗП работника зависела от того, сколько деталей он сделает. Он делал их и делал, и накапливал огромные запасы. А когда японцы решили перейти на вытягивающую систему, то поняли, что тогда всех операторов нужно переводить на оклад, т.к. если работать по канбану, то нужно делать столько деталей, сколько написано в канбане. Ни больше, ни меньше. И что если оставить сделку, то рабочие будут сильно против канбана, т.к. он заставляет их делать и зарабатывать меньше. Поэтому японские рабочие бы сказали, уберите свой канбан и дайте нам как раньше делать бесконечные горы деталей.
Но это же совершенно не означает, что сделка это всегда и везде зло! Если делать нужно действительно чем больше тем лучше. Если результат легко измерим, а работников нужно очень жестко замотивировать, то почему нет? От ситуации отталкиваться надо. Как минимум это полезно тем, что становится не надо мотивировать. Это хорошо, когда процесс прост как 5 копеек, и нужна только энергичность, и объем работы «чем больше, чем лучше».
Моя парадигма вместо этой, ошибочной: сдельная оплата труда допустима, если здесь и сейчас она вам подходит.
6. Запасы – зло!
Не всегда запасы зло. Если у вас производится много номенклатур товаров, а быстрая переналадка имеет свои пределы, то хороший способ снизить сроки отгрузки готовой продукции клиенту – иметь определенные запасы готовой продукции. При поступлении заказа – сразу же их отгружать, и начинать производство продукции, чтобы снова восполнить неснижаемый остаток. То же относится и к незавершенному производству.
По возможности запасы нужно снижать. Но только пока это целесообразно. И точно не жертвуя сроками отгрузки, чрезмерно частой переналадкой или чем-то еще более дорогим, чем запасы. Да и если объединять закупки в одну поставку, можно получить скидки, и поставщики будут лучше к вам относиться. Так что это надо еще посчитать, в какой точке потерь меньше.

Моя парадигма вместо этой, ошибочной: нужно решить, какое количество запасов незавершенного производства и готовой продукции вы должны держать, и что вы от этого выиграете.
У меня был очный и публичный разговор с одним бережливцем из РЦК. Он делал выступление о сокращении запасов. Я спросил, что он скажет на то, что многие компании после начала COVID-19 и СВО выжили только благодаря запасам? Ещё этот корабль застрявший – Ever Given. Он ответил, что всё это – черный лебедь, а их невозможно предсказывать. А раз их не предсказать, то и не надо брать их в расчет. Нассим Талеб писал в своей книге «Черный лебедь» буквально противоположное. Что черных лебедей нельзя предсказать и под них НАДО закладывать резервы. Только делать это надо с умом, а не просто громоздя завалы из хлама.
7. Семь (8, 9, 10) видов потерь
Это даже и близко не весь спектр потерь!
– Где перерасход материалов, энергоресурсов?
– Где перерасход площадей?
– Где перерасход фонда оплаты труда?
– Где ускоренный износ?
– Где неверное ценообразование?
Концентрируясь на 7 видах потерь, можно не заметить гораздо больше!
У этого есть два популярных возражения:
– То, что я дописал – это не потери, а затраты.
– То, что я дописал и так входит в 7 видов потерь, просто нужно смотреть глубже. Оно там зашифровано.
А затраты от потерь чем отличаются? Тем, что их не нужно снижать, что ли? Лишние затраты и есть потери.
А объединение потерь не выполняет свою единственную функцию – не помогает увидеть потери на производстве. А значит, ничем не помогает в работе.
То есть проблема не в принципах как таковых, а в фанатиках
Они НЕ считают, что само бережливое производство тоже нужно совершенствовать и улучшать.
Я предполагаю, что если тех японцев (может быть это были и не японцы, а американцы или советские люди), кто впервые определили эти парадигмы, поставить в эти спорные ситуации, они бы не задумываясь вышли бы за рамки своих же парадигм. И сказали бы, что их принципы носят рекомендательный общий характер, но вот тут же очевидно, что нужно сделать не так.
В книге «Тойота Ката» написано, что японцы всегда в легком замешательстве от того, что иностранцы раз за разом приезжают и изучают решения, которые на Тойоте были приняты для решения совершенно определенных проблем. Но почему-то приезжающие не заостряют внимание на том, как японцы додумались до этих решений. В той книге написано, что японцы считают ошибкой копировать инструменты. Считают, что лучше бы скопировали метод придумывания инструментов.
За рамки бережливого производства можно легко и быстро выходить, когда это нужно. Важно то, что есть цель – достичь лучших показателей бизнеса. А способы могут быть любыми, и во что бы то ни стало пытаться вписать их в рамки БП – глупо.
Глава 38. LEAN второго поколения
У lean, очевидно, есть недостатки, которые зашиты в саму его структуру:
– При всплеске спроса может не хватить ресурсов для изготовления всех внезапно свалившихся заказов, и тогда срок отгрузки увеличивается еще сильнее. Потому что в Lean на предприятии есть какие-то неснижаемые запасы материалов, но в наибольшей степени закупка материалов привязана к поступлению новых заказов.
– Уязвимость к подставе от поставщиков. Хорошо, когда ваш поставщик никогда не срывает сроков поставки. Но если это происходит, вы не можете выполнить свои договорные обязательства, т.к. ваши запасы малы. А массовое производство – может. Даже если поставщик задержал поставку, у них настолько много жира в виде материалов, что они могут совершенно спокойно работать еще хоть целый месяц.
Коронакризис
Производственная система Тойоты возникла как раз в ответ на кризис! Это изначально антикризисная система и была. Потому что денег не было, и приходилось изготавливать автомобили, которые уже купили, а не в запас гнать. Это была вынужденная мера, чтобы выжить, а не какая-нибудь выдумка ради выдумки, чтобы потом писать книжки о TPS.
Поэтому сама постановка вопроса «переделывать ли компанию в бережливое производство в условиях сложившегося кризиса, или сейчас не время, и нужно выждать более тучных времен» для меня абсурдна. Это и есть система для работы в кризисе. А массовое производство обычно процветает в тучные времена, на растущем рынке, в условиях неограниченного спроса.
Lean второго поколения (прижившиеся мутации)Можно пойти еще дальше. Об этом ни Тайити Оно ни Джеффри Лайкер ничего не писали. «Второго поколения», потому что это не то, о чем писали 30 лет назад.
1. Вытягивание не только производства, но и разработкиДопустим, есть сайт, который продает много разных аппаратов явно не штучного, а типового производства. За этим сайтом стоит производство. Производство выполняется по разработанным проектам.
Но проекты есть только на 50% от представленного ассортимента. У остального ассортимента есть только картинка на сайте и больше ничего. На сайте 100% предоплата и оговоренные сроки поставки. Вы вносите предоплату, и с этого дня начинается РАЗРАБОТКА ПРОЕКТА по изготовлению этого аппарата. То есть у компании не было НИЧЕГО кроме вот этой картинки в формате. jpg на сайте. И за большинством картинок на их сайте также ничего не стоит. А откуда тогда картинка? С сайта конкурентов или нарисована. Проект, как именно это изготавливать, начинает появляться после того, как кто-то вносит предоплату. И когда такой аппарат кто-то покупает во второй и последующий разы, то в этом случае проект на изготовление уже есть.
Компания ничего не теряет, производя те аппараты, от которых уже есть проекты. А новые не проектирует. Потому что вдруг этот аппарат никто никогда не купит? Тогда его проектирование было произведено зря, а это затраченные ресурсы. Чем не вытягивание? Чем не lean? Следующий его шаг.
Пришла идея с новым аппаратом. Нужен такой кому-то или нет? Пофиг на сомнения – выложили на сайт, и ждем, пока купят. Когда у разработчика появляется лишнее время, он может спроектировать один из аппаратов на будущее. Но при этом на сайте еще 50 «просто картинок».
Вы скажете, что это неправильно, что это не производство, а какая-то голь перекатная, у которой за душой ничего нет, одни картинки из интернета. Да, это так. И что? А у Тайити Оно не было ничего по сравнению с General Motors. Пустой склад. Ни машин, ни материалов, ни полуфабрикатов. Примерно так же ему все говорили в то время. Он 10 лет подряд переубеждал людей.
Нассим Талеб писал о том, что имеет смысл то, что ВЫЖИЛО, что прижилось. Оно своим существованием доказывает свою конкурентоспособность. Да, эта модель бизнеса выглядит как глубоководная рыба-удильщик. Лежит такая на дне, в анабиозе, ждет, светит фонариком. Но до чего же они живучие.
Если ваше производство привязано к интернет-магазину (а такое я видел несколько раз), то реальным шагом к бережливому производству, к сокращению времени выполнения заказа (lead time), будет не просто быстро производить то, что у вас фактически заказали, но также и отслеживать, что клиенты надобавляли в корзину покупок, и не оплатив и пошли спать.
Это даст вам информацию, куда примерно дует ветер. Какие примерно материалы ставить на закупку, как приблизительно распланировать производство, чтобы быть более готовыми к тому, когда наполнение корзин все-таки оплатят. Да, информация будет приблизительная, но она будет. А вы уже сами будете принимать решения, как вам поступать.
Одно дело опираться на статистику предыдущих продаж. Но ничто не мешает смотреть еще и на прогнозные данные.
2. Сокращение не только запасов сырья, незавершенного производства, и готовой продукции, но еще и капитализацииНи для кого не секрет, что бизнес в России не защищен, что в любой момент может произойти рейдерский захват или еще чего-нибудь плохое. И в результате выстраивания бизнеса на пороховой бочке рождается система нулевой капитализации. Чем не Lean? Тот же Lean. Только на шаг дальше. Минимум запасов. Минимум запасов в активах. Иными словами, никакого своего имущества предприятия. Это ведь тоже запасы.
Смысл в том, чтобы выстроить такую компанию, которую можно было бы закрыть, закрыв ноутбук и выйдя из здания. И сразу же свалить за границу с деньгами на счетах. Не тратя время на распродажу имущества компании, потому что имущества и нет. Абсолютно всё материальное находится в аренде. Всё, что можно, на аутсорсинге и фрилансе. Безусловно, такая модель больше всего подходит для сферы услуг, т.к. в такую компанию сложно привлечь инвестиции, сложно получить кредиты, и сложности с контрагентами. Но услуги выполнять можно.
Вы можете застрелить из ружья слона. Но не можете застрелить рой мух, который суммарно весит как этот слон. Поэтому такие компании состоят из нескольких десятков отдельных юр. лиц. А главная муха вообще на Кипре или в Дубае.
Американские компании уязвимы, в частности, еще и потому, что у них есть главная муха. Если она умирает, то другие мухи колонии не будут знать, что им делать. А вот у японцев этот баг отсутствует. Там главный настолько отстранен от управления компанией и сконцентрирован на более высоких материях, что если он выходит из строя, то совершенно ничего в компании не меняется. Вы не представляете, до какой степени огромная компания может напоминать цыганский табор. Много зданий, автомобилей, техники (такой как бульдозеры, экскаваторы, краны). Абсолютно всё не в собственности.
На некоторых рынках арендный путь без капитализации не самый эффективный, т.к. за аренду, по сравнению с собственностью, всегда переплачиваешь. Но зато он надежный в условиях непредсказуемого рынка. Когда кормовая база внезапно иссякает, можно выжить не только за счет жировых запасов, но и за счет впадения в анабиоз или закопанных запасов еды (которые не нужно таскать на себе как жир) или замедления метаболизма (черепахи, ленивцы) или перехода на другой источник питания (плотоядные растения). У живых организмов очень много путей выживания, и только у тех организмов он является неправильным, которые вымерли. Выживает тот, кто быстрее всего приспосабливается к изменяющимся условиям.
Поколение Z
По теории поколений, говорится, что поколение X инстинктивно стремится к накоплению активов. Побольше квартир, загородных домов, машин и яхт, и всё в собственности. А поколение Z инстинктивно стремится к сокращению активов. Они копят деньги в долларах, подписчиков в соцсетях, навыки, знания и впечатления. А всё остальное используют в аренду.
Часть 4. Как это всё происходит на практике
Глава 39. Как попал в сферу развития предприятий
Это была случайность, я о таком и не помышлял.
Но меня с самого детства бесило всё неэффективное, любая бесполезная работа, бездарная трата времени.
Я проучился на инженера-электрика 5 курсов, и у меня осталось еще 6 месяцев на написание диплома. В 2010 мы с однокурсником пошли на завод, чтобы устроиться инженерами-электриками. Там сказали, что на работу нас берут, однако посадить нас некуда, т.к. нет компьютеров и столов, и их надо купить. И дождаться их нам предложили в производственном цехе в качестве слесарей-сборщиков.
Это были мучительные 3 недели, т.к. работы не было ВООБЩЕ. Мы слонялись по цеху, разговаривали и не знали, чем себя занять, т.к. совершенно вся работа была сделана. Как только появлялись какие-то дела, мы моментально их делали и продолжали слоняться. Попросить еще работы у мастера не получалось, потому что была проблема с поставками, и на предприятии просто не было комплектующих, из которых делать продукцию.
Скуку я переносить вообще не в состоянии, поэтому, когда директор по персоналу вышел в цех и спросил, кто умеет работать за компьютером, я, конечно же, вызвался. Кроме меня было еще трое претендентов, но взяли меня. Так я попал в управление по развитию. Я рассуждал так: «я согласен на что угодно, лишь бы не безделье в цехе».
В начале работы в отделе развития не получалось вообще абсолютно ничего, но мной руководила сильнейшая мотивация избегания. Больше всего я боялся вернуться обратно в цех и ничего там не делать.
Зарплату мне дали тогда 10 тысяч рублей. Микроскопическая даже по меркам 2010 года, даже по меркам Дзержинска.
Совсем уволиться я тоже не мог. Спустя первую неделю в управлении по развитию у меня ничего не получилось настолько сильно и было это настолько стремно, что в какой-то момент я просто выдохнул и сказал себе:
«Ок, я буду просто работать изо всех сил до тех пор, пока меня не уволят. Сколько успею продержаться, всё моё».
Всё усугублялось еще и тем, что мой начальник начитался дурацких книжек про нейро-лингвистическое программирование, в которых написано, что для того, чтобы тебя воспринимали лидером, нужно говорить очень тихо. Чтобы прислушивались, тянулись, замирали т. д. Когда я говорил ему, что не слышу, что он говорит, он вдруг переходил на крик. Причем, кричать начинал с того момента, на котором остановился, а не возвращался на тот кусок, который я не слышал. Надеюсь, он это когда-нибудь прочитает и ему будет стыдно.
В общем, это всё не способствовало пониманию заданий и их выполнению. Но в целом я ему благодарен, ведь он же вытащил меня из цеха. А покинуть его отдел я мог в любой момент.
До меня за моим столом работал какой-то сотрудник, и он оставил после себя целую гору бумаги в каждом из выдвижных ящиков и на столе. Я сразу же всё выбросил, потому что это были беспорядочные кучи бумаги без какой-либо системы, а не подписанные папки и каталоги в шкафу. Потом был всего 1 единственный раз, когда что-то из тех документов кому-то понадобилось, и тому человеку я ответил «Я всё выбросил».
В какой-то момент моя гипер-мотивация начала приносить плоды и я начал выплывать все лучше и лучше с каждой неделей. В кабинет проектировщиков так, по-моему, никаких столов тогда и не купили, и мой друг, с которым я пришел, тоже не устроился проектировщиком, а ушел в продажи на этом же заводе.
Через полгода (когда я должен был защитить свой диплом) этих сверхусилий я уже прокачался настолько, что мой начальник начал намекать мне, что он не хотел бы, чтобы я сразу же свалил куда-нибудь, получив диплом. Ещё он очень не хотел, чтобы меня забрали в армию. Какое-никакое признание. Я не хотел никуда сваливать, т.к. уже втянулся и начал получать кайф от этой работы. У меня тогда еще одна мысль пришла, что то, чем я тут занимаюсь, очень похоже на то, чем я занимаюсь в компьютерных играх: оптимизирую свою базу, всё обустраиваю. И эта мысль помогла мне полюбить свою работу еще сильнее и найти в ней азарт.
Срочной-обморочной работы было настолько много, что мой стол был завален невероятными кучами бумаги, и мне что-то абсолютно некогда было ее разобрать. Но всем было пофиг на это. Нужно было выполнять поставленные цели, и методы достижения этих целей никого не интересовали.
Электриком я так ни дня за всю жизнь и не работал.
Правообладателям!
Это произведение, предположительно, находится в статусе 'public domain'. Если это не так и размещение материала нарушает чьи-либо права, то сообщите нам об этом.