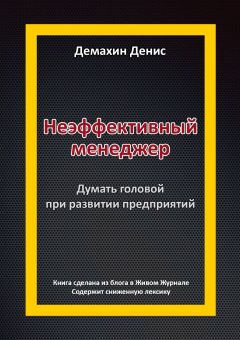
Автор книги: Денис Демахин
Жанр: Руководства, Справочники
Возрастные ограничения: +18
сообщить о неприемлемом содержимом
Текущая страница: 14 (всего у книги 17 страниц)
Глава 40. Ката развивальщика
Я думаю, главные черты развивальщика это энтузиазм и открытый разум. Быть развивальщиком очень интересно. В этой работе постоянно приходится продираться через непонятное и запутанное. Осваивать что-то новое. Держать нос по ветру. Быстро схватывать суть систем.

Людей со знанием сферы у заказчика ваших услуг – и так вся компания. Но развитие не движется. Потому что в лице вас им нужен человек с энтузиазмом, с проактивностью, со способностью посмотреть на всё иначе. Нужен тот, кому еще и больше всех надо. Нужен тащер. Да, у вас нет знаний в этой сфере, но вы можете взять их от сотрудников предприятия, и в итоге связать всю систему иначе.
В этой работе очень часто бывают конфликты. Это кажется, что развивальщик, он решает проблемы, всем помогает. Это так, но часто при этом приходится подсветить чью-то мутную водичку, где кто-то прятал свои косяки. Или кому-нибудь создать дополнительные обязанности. Святым тут быть не получится. Всегда будет обнаруживаться какой-нибудь конфликт интересов. Нужно быть готовым держать удар. Притом почти всегда находясь в положении самого ничего не знающего человека о предмете обсуждения.
Иногда влиятельности не хватает, чтобы реализовать хорошее улучшение. Потому что владельцы процесса в этом не заинтересованы, и все разом уперлись в дверь с другой стороны. В итоге, улучшение разработано, а все равно не реализовывается, и тут хоть тресни. К этому тоже нужно быть морально готовым. Много политики, много вопросов управления влиятельностью, властью. Об этом будут некоторые кейсы чуть ниже.
Как именно изучаю текущую ситуацию системы яСначала я разговариваю с каждым погруженным в ситуацию человеком по отдельности, и всю информацию записываю в блокнот. Наблюдаю за работой, собираю данные. Постепенно у меня в голове начинает выстраиваться цельная картина происходящего и сразу же – карта будущего состояния. Тогда я излагаю всё на двух блок-схемах и показываю их всем тем же участникам по очереди. Глядя на схему, они называют еще какие-нибудь нюансы, которые я учитываю. После того, как у всех закончатся мысли по поводу того, что еще нужно указать на схемах, тогда я собираю большое совещание, где все уже коллективно подводят итог, что двигаться мы все договорились вот к такому будущему состоянию.
На начальных этапах составления карты текущего состояния, она будет очень далека от идеала. Не пытайтесь сразу учесть всех на свете нюансов, иначе утратите динамику и впадете в аналитический паралич. Лучше набросайте мысли как есть, и сразу же покажите это руководителям самых базовых ячеек в исследуемой системе. Они скажут, что всё у вас неправильно. Но ничего в этом страшного нет, ведь они озвучат новую информацию, и вы продвинетесь в понимании на шаг дальше, и серая мгла неопределенности чуть рассеется перед вами.
Среди ваших собеседников могут оказаться особенно отъявленные защитники стабильности, которым будет не нравиться всё, что вы предлагаете. Защитники стабильности озвучат вам гору нестыковок, шероховатостей и прочих проблем в ваших предложениях. И спасибо им! Потому что если бы их не было, то вам пришлось бы потратить в 10 раз больше времени, чтобы найти все эти нюансы и подводные камни, и учесть их в своих предложениях. А тут они их предоставляют вам на блюдечке. Это нужно ценить. Консерваторов нужно не затыкать, а решать озвучиваемые ими проблемы, делая решение оптимальнее.
И когда на уровне пониже все уже выскажутся, тогда у вас появится крутая, проработанная бумага, с которой можно уже идти к более высоким начальникам и утверждать план действий и просить ресурсов для реализации.
В конце я дам подборку самых странных, но зато интересных проектов развития, которые мне подворачивались. Больше проектов описано в блоге.
Глава 41. Состояние потока
Я не знаю, как это устроено у других людей, поэтому напишу про себя.
Поток – это состояние максимальной концентрации, сопровождаемое душевным подъемом. В таком состоянии производительность взлетает многократно. После такого дня ты ощущаешь только удовлетворение и довольство собой. Спина выпрямляется, появляется улыбка, ускоряется шаг, речь становится громче и быстрее. Все действия оптимизируются и ускоряются. Ничего не отвлекает.
Это бесплатный наркотик, это мощь. Я постоянно ищу этого состояния. В нем ты как акула, плывущая на запах крови. В нем ты как будто спидранишь компьютерную игру. Это самое лучшее состояние для развивальщика.
Я пребывал в нем огромную часть времени моей работы на ОАО «НИПОМ». И я ловил с этого кайф. Да, я был как заноза в заду у сотрудников. Об этом мне говорил каждый третий, если не второй.
Как вызвать это состояниеОтвета на этот вопрос я не знаю. Оно приходит как-то само. Но все-таки есть некоторые факторы.
1. Реакция на стресс
«Наиболее естественное состояние человеческой особи – это война». Эту фразу я прочитал у какого-то писателя, когда еще читал художественную литературу. Кажется, это был Беркем аль Атоми. Стресс меня мобилизует. Моя на него реакция – гиперактивность. Мне нужно ощущение опасности. Но проблема с этим в том, что я не могу вызвать это ощущение сам, источник угрозы должен быть внешним. Это может быть начальник или же какая-то ситуация с клиентом, или полыхающие сроки по проекту. Должна быть ситуация «победа или смерть». Без внешнего стрессора я чахну. Меня покидают силы, и я засыпаю.
2. Перешутить кого-нибудь или обстебать в глаза
Выйти победителем из обмена подколками или сделать смешной розыгрыш, который удался, или высмеять кого-то в его присутствии. Это мгновенно и очень надолго заряжает внутренние батарейки. Это намертво приклеивает улыбку к лицу.
3. Задачи в стиле «добыть неизвестно где» или «сделать непонятно как»
С жестким ограничением по времени. Когда начальник говорит «У тебя час», то в этот момент в голове переключается какой-то тумблер, и открывается баллон с закисью азота.
4. Опыт в системе
Состояние не включается, если знаний о том, как всё устроено, недостаточно. Когда знаний, чтобы выполнить задачу, менее 10%, состояние потока как будто находится на ручном тормозе. Все действия становятся осторожными и очень обдуманными, десятикратно перепроверенными. Когда знаний для выполнения задачи около 50% (а остальные 50% надо найти здесь и сейчас), вероятность появления потока сильно возрастает. Когда знаний для выполнения задачи в наличии 100% – может быть уже слишком скучно делать это.
5. Когда есть идея
Когда идея ослепительной вспышкой появилась в голове сразу во всех деталях, и ее нужно только как можно быстрее переложить на бумагу. Именно под такой эйфорией я часто пишу свой блог.
Поэтому мне очень нравится моя профессия. Ее будни проходят в чреде сражений и побед. И с каждым днем становишься всё сильнее.
Глава 42. Матрица встроенного качества

Эту матрицу я сделал своими руками
В тот период (2012) наш отдел развития сначала делал, а потом думал. Мы сумели это запустить, потому что были как 22-летние революционные матросы, и всем выносили мозг. У нас был вагон энтузиазма. На эту матрицу нас надоумили развивальщики из нашей же головной компании, тоже не особо на тот момент думающие. Просто, они знали этот тойотовский инструмент управления качеством, и знали как он работает.
Это классический пример внедрения инструмента бережливого производства ради самого инструмента. Когда никто не понимает, зачем мы его внедряем. Но внедряем, потому что это же с Тойоты.
Концепция правильная
Логика матрицы в том, что чем раньше по цепочке процесса мы находим дефект, тем он дешевле в плане потерь для предприятия. Одно дело мы сразу же убираем бракованную деталь, а другое дело, что мы ее еще после этого отполировали, покрасили, установили в сборку, провели наладку, испытания. А теперь нужно разобрать половину изделия, чтобы ее оттуда достать. А потом заново делать наладку и испытания.
То есть, по концепции этой матрицы нам нужно добиваться того, чтобы мы находили и удаляли бракованные детали как можно раньше после их появления. Чтобы они не шли дальше по техпроцессу, и не создавали этим всё больше и больше потерь.
Цель, конечно, понятная и нужная. Особенно для автомобильного конвейера, для чего она и разрабатывалась. У нас же была стапельная сборка электрощитов.
Выглядит интересно
Предполагалось, что сотрудник со сборки каркасов, со сборочного участка, с участка электромонтажа, с испытаний, или наладки обнаруживает дефект, подходит к матрице, берет чистый бланк, описывает проблему, и помещает ее в кармашек на пересечении, где он дефект нашел, и где он, предположительно, появился.
И таким образом мы видим наглядную картину, что чем ниже и левее находятся бумаги, тем хуже. А это дает нам понимание приоритетов в решении проблем. А также мы видим, какой участок больше всех находит дефектов, а кто совсем ничего не пишет.
Тут же мы вывешиваем распечатки статистики по дефектам, а также инструкции, как пользоваться матрицей и как заполнять бланк.
Гладко было на бумаге
Все бланки вносил в экселевский файл (журнал) отдел качества, и якобы как-то там с этими дефектами работал. Отдел развития сделал своё черное дело – направил на отдел качества поток этих бланков о дефектах (алмазов, ага). Хлынуло как из брандспойта. И с чувством выполненного долга пошел по своим делам.
Я одного тогда не мог понять. А зачем рабочему думать о том, в какой карман что положить, если каждый день приходит инженер по качеству, собирает бланки со всех карманов в одну стопку, несет это всё в кабинет, и там переписывает в экселевский файл? Мне почему-то кажется, что на Тойоте рабочие писали бумаги в один карман, инженер это забирал, а раскладывал по карманам уже в своем кабинете. И матрица встроенного качества висела в его кабинете, а не в цехе.
Но зато наша матрица привлекала внимание, и своей структурой объясняла логику управления качеством. И может быть частично из-за этого писали немного больше.
Матрица встроенного стукачества
Рабочие у нас работали по нормочасам, и главным мотиватором для них было объявлено то, что если кто-то нашел дефект, он пишет в бланке, сколько времени он потерял на исправлении дефекта или замене детали, и ему возвращают эти нормочасы.
О штрафах за дефекты речь вообще не поднималась, но всё равно производственники на своих смежников писать ничего не хотели. Мы по поводу этого не тревожились, т.к. бланков писали и так целую гору.
Но на кого же тогда их писали, если никто не хотел стукачить? Ну конечно же на инженерный центр! Всё, что писали рабочие – это были дефекты в конструкторской документации. Написать 150 тысяч бумаг на инженера – это для рабочего милое дело. Стукачество – это только когда ты член этого коллектива. А инженеры – это совсем не подпадает под определение своего коллектива для рабочих. Там – отдельный коллектив, совершенно другой. Там упыри.
Внезапная остановка
В какой-то момент писать что-либо резко перестали. Прямо в момент, как будто вентиль одним махом перекрыли. Потому что не видели обратной связи, не видели никакого толку. Система с нормочасами была непрозрачной, и нельзя было проконтролировать, вернули рабочему нормочасы, или забыли.
Кроме того, рабочие видели повторение тех же самых дефектов, о которых они писали ранее, и это тоже сильно их расстраивало.
В-третьих, рабочие описывали дефект в КД, отдел качества направлял эту информацию в инженерный центр, оттуда приходила отписка типа «Сам дурак, в КД всё правильно». На это рабочий опять писал «Нет, это я прав, а ты нет». В результате рабочие только тем и занимались, что переписывались по поводу дефектов, а те не решались.
И в какой-то момент все одновременно решили прекратить это делать. Отдел развития не придумал ничего лучше, чем снять эту матрицу со стены и убрать в чулан. После этого, сделали еще одну, просто убрав из нее всё лишнее.

Ее запустили с перерывом в несколько месяцев от предыдущей. В нее почти ничего не писали, но она была, чтобы была возможность написать.
Глава 43. Быстрая переналадка размером с завод
В июне 2016 года от директора управляющей компании мне поступило задание путем изучения производственной системы нашего филиала придумать, каким образом повысить производительность предприятия. Главный технолог и начальник производства также были заняты этим вопросом. Проект выполнялся из должности специалиста по СМК.
Предприятие является химическим, работающим 24 часа в сутки. На предприятии присутствует сезонность. Около пяти месяцев в году предприятие работает на максимум производительности и 7 месяцев испытывает недозагруз производственных мощностей из-за падения спроса.
На следующий день я позвонил директору управляющей компании чтобы сообщить о том, в какую сторону собираюсь рыть. Дело в том, что на предприятии помимо «узких мест» есть еще и стадии полного перерыва производства – «огневые работы». Сложность заключается в том, что на данном химическом производстве используется легко-воспламеняющиеся сырье. Поэтому для того, чтобы в реакторном зале выполнять технические работы с присутствием открытого огня (сварка, резка) или электроинструмента, необходимо останавливать синтезы, освобождать трубопроводы от сырья и промывать их..
Для выполнения огневых работ производство останавливается на целый рабочий день или на половину дня. Это производится чаще, чем 2 раза в месяц.
При огневых работах бездействует весь завод, а это означает, что их следует производить как замену колес и дозаправку на гонках F-1: любая подготовка окупится. Кроме того, не следует забывать еще и о том аспекте, что производство останавливается не мгновенно и запускается тоже не мгновенно, что еще сильнее увеличивает простои, следовательно, и убытки.
Огневые работы выполняются ремонтной группой согласно плану, разработанному главным механиком.
Ремонтная группа состоит из:
– 1 бригадир (слесарь);
– 4 слесаря;
– 1 токарь;
– 2 сварщика.
Проблема состоит в том, что производство останавливают и начинают максимально неторопливо выполнять работы. В то время как должны делать это в экстренном, аварийном режиме. А в обычное время можно работать более размеренно. Как пожарные.
Первый хронометражПервый хронометраж выполнялся во время сезона высокого спроса. На первый хронометраж я вышел один, хотя рабочие были разделены на 2 группы и выполняли задания в разных местах предприятия. Так как следить за 2 группами, находящимися в разных местах, неотрывно невозможно, хронометраж получился не очень подробным, он содержал только основные временные вехи. По этой причине он даже специально был назван «хронология», а не «хронометраж». Также в процессе изучения были сделаны фотографии, на каком состоянии монтажа начались огневые работы и какие результаты были по его завершении.
Итоги первого хронометражаПервое изучение огневых дало довольно шокирующие результаты. Этот отчет был настоящей бомбой, которая эмоционально взорвала несколько людей. Это то, чего я и пытался добиться.
Огневые работы длились 5 часов 24 минуты: 45% времени было потрачено на то, для чего не требовалось останавливать производство. Все эти работы могли выполняться в рабочем порядке. Из этих 45% 34% было потрачено на откровенные потери: обед, перерывы на чай, курение и даже домино (суммарно достигло длительности 1 ч 49 мин).
Даже необходимые документы (наряд-допуск) были оформлены только к середине огневых, а без данного документа рабочие не приступят к работам с открытым огнем.
Остальные 55% времени были потрачены действительно на работы, для выполнения которых требовалась остановка производства, и на данном этапе детализировать их не было возможности и нужды. Они состояли из обсуждения, как далее вести трубы, из замеров, отрезания труб с помощью УШМ (болгарки) и из сварочных работ. Все эти операции в данном конкретном хронометраже были обозначены как полезные, но в дальнейшем я планировал детализировать этот блок, разобрать его на составляющие с целью дальнейшей оптимизации.
Для успеха проекта была критически необходима максимальная ангажированность руководителей, но никаких полномочий влиять на них у меня не было, поэтому отчет нужно было составлять максимально заметным, подробным и важным.
В отчете было указано, куда тратится время в процентном соотношении, стоимость одного часа простоя производства, а также частота выполнения огневых работ (17 раз за последние 7 месяцев).
В качестве предложений по улучшению было указано самое первоочередное и элементарное на данном этапе:
– Повысить дисциплину. Сократить перерывы до положенных 48 минут;
– Производить огневые работы максимальными промежутками времени: по 8, по 12 часов. Чтобы сократить количество остановок и пусков производства. Переработки компенсировать отгулами;
– Выносить все операции, которые могут быть выполнены без остановки производства, за пределы времени остановки производства;
– Максимально подготавливаться к огневым работам до их начала;
– Подготавливать наряд-допуск заранее.
Переходить к более сложным улучшениям нет смысла пока не будут выполнены эти.
Согласовал отчет с начальником производства, главным механиком и главным инженером, после чего разослал всем руководителям, а также директору управляющей компании (заказчику проекта).
После этого генеральный директор филиала инициировал совещание по проблемам огневых работ, на котором все руководители по очереди высказывали свои предложения. В основном эти предложения совпадали с теми, которые уже были написаны в отчете, но было и новое:
– Прикреплять к каждой из ремонтных групп по одному аппаратчику синтеза, который может помогать делом, а также отвечать на вопросы касательно нюансов прокладки трубопроводов (ему потом их эксплуатировать);
– Сделать плавающий обед. Чтобы не все одновременно уходили на обед, а по очереди.
Процесс монтажа трубопроводаВо время проведения хронометража я наблюдал сам процесс создания новой линии трубопровода. Новая линия может создаваться по рационализаторскому предложению или же по инвестиции. Сам трубопровод всегда имеет сложную геометрию: он проходит между реакторами, между другими трубопроводами, иногда сквозь этажные перекрытия и стены. Новый трубопровод имеет множество изгибов, фланцевых соединений и кранов. Он может быть настолько изогнутым, что на длине в 200 мм содержать по 5 сварных швов.
Никакого проекта никогда нет. Всё проектирование заключается в том, что главный механик словами по месту объясняет, как именно нужно вести трубу, где и как примерно она должна проходить. После этого слесари и сварщики приносят на место монтажа стандартные трубы, элементы и краны, и прямо здесь, на месте монтажа, их и отрезают.
Процесс монтажа состоит из этапов:
– замер рулеткой по месту;
– отрезка участка трубы с помощью УШМ (болгарки);
– наживление этого участка трубопровода (приваривание несколькими точечными касаниями сварочного аппарата);
– приваривание этого участка трубопровода;
– обстукивание шва сварочным молотком для снятия окалины;
– поливание шва водой для его охлаждения.
На тот момент мне пришла идея о том, что можно попробовать ввести эскизирование или проектирование трубопроводов для того, чтобы максимально сократить затраты времени во время остановки производства за счет времени перед наступлением момента остановки (пока предприятие производит продукцию, а не простаивает). С помощью проектной работы можно изготовить какие-то отрезки трубопровода заранее, доставить их на участок, а во время остановки приваривать один за одним.
Чтобы увидеть время, затрачиваемое на замеры и отрезку участков трубы, я предложил выделить эту операцию в отдельную графу бланка хронометража.
Главный механик грубо отверг эту идею, назвав ее бредом, сказав, что эти операции – неотъемлемая часть процесса и они однозначно должны быть классифицированы как полезные. Сказал, что он уже 7 лет занимается монтажом трубопроводов и знает, что невозможно так точно спроектировать трубопровод: всегда что-то где-то не сойдется.
После того, как все решения были озвучены, для моего проекта были выделены дополнительные силы: следующий хронометраж должен был быть выполнен не одним человеком, а таким количеством людей, сколько рабочих групп участвовало бы в проведении огневых работ (чтобы ничего не упустить и сделать хронометраж подробнее). Он должен был также показать и то, насколько владельцы процесса (главный инженер и главный механик) улучшили процесс и повысили производственную дисциплину.
Правообладателям!
Это произведение, предположительно, находится в статусе 'public domain'. Если это не так и размещение материала нарушает чьи-либо права, то сообщите нам об этом.