Текст книги "Общая технология отрасли"
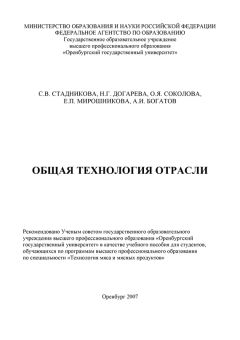
Автор книги: Наталия Догарева
Жанр: Техническая литература, Наука и Образование
сообщить о неприемлемом содержимом
Текущая страница: 16 (всего у книги 18 страниц)
Для очистки костный жир обрабатывают серной кислотой в деревянных чанах при перемешивании открытым паром. Костный жир, полученный в процессе обезжиривания и освобожденный в дистилляторе от растворителя, содержит большое количество воды (конденсат пара), примеси белковых веществ и загрязнения.
Процесс очистки достигается следующим способом: эмульсия жира разрушается, благодаря чему жир легко освобождается от воды, белковые вещества в виде продуктов распада удаляются, кальциевые мыла расщепляются с выделением жирных кислот.
(RCOO)2Ca+H2SO4→CaSO4+2nCOOH,
где R – радикал жирной кислоты.
Все другие органические загрязнения также разрушаются в кислоте. Серная кислота применяется 65 %, удельный вес 1,56, более крепкая разрушает жир. Расход серной кислоты – 2 – 5 % от веса жира в зависимости от загрязнений жира и ассортимента кости. Содержание влаги в жире должно быть не более 1,5 %.
13.1.5 Очистка обезжиренной кости (полировка)На поверхности обезжиренной кости после выгрузки ее из экстракторов имеется значительное количество неклейдающих веществ (грязь, песок, и пр.) или веществ, дающих клей плохого качества (некостенеющий хрящ, который в большом количестве имеется на колбасной кости, балластные белки, сопутствующие коллагену). Все загрязнения затрудняют последующую обработку кости, кроме того, сокращается емкость аппаратуры и ухудшается качество готового клея.
Обезжиренную кость подвергают тщательной очистке – полировке – в специальных непрерывно действующих барабанах, после этого кость приобретает чистую, гладкую поверхность. Очищается кость в результате трения кусков ее друг о друга и о стенки барабана при его вращении. В процессе полировки загрязнения и мелкая кость проходят через сетчатую поверхность барабана, образуя азотистый отход, который сортируют на сито-бурате. Сито-бураты устанавливаются в отдельном помещении или непосредственно под полировочным барабаном. Азотистый отход применяется как удобрение и в небольших количествах на металлургических заводах для закалки стали.
13.1.6 Замочка костиПолированный шрот поступает на замочку в воде или частичную мацерацию в слабых растворах кислот. Обводнение кости перед обесклеиванием имеет большое значение в производстве клея. Благодаря набуханию коллагенновой ткани процесс обесклеивания можно производить при смягченном тепловом режиме, что способствует получению более концентрированных бульонов, извлечению основной части клея в начале процесса обесклеивания, уменьшению гидролиза глютина и повышению качества клея.
На клеевых заводах применяют два метода обработки кости (шрота) перед обесклеиванием: обработка водой и мацерация сернистой кислотой. Под мацерацией не следует понимать процесс деминерализации кости, которая проводится в желатиновом производстве. При обработке кости водой получается примерно такой же эффект набухания, как и при обработке 1,0 – 1,5 % раствором сернистой кислоты, причем в первом случае процесс значительно проще и дешевле. В воде кость замачивают в отдельных чанах или в диффузорах, меняя воду через каждые 4 – 6 часов. К воде добавляют сернокислый цинк, который обладает консервирующими свойствами.
Работами ВНИИМПа установлено, что замочку следует производить под гидравлическим давлением не менее 2 атм., при этом набухание происходит значительно быстрее, чем без давления. Набухание кости при двухчасовой замочке под давлением соответствует набуханию при двенадцатичасовой за мочке без давления.
13.1.7 Обесклеивание кости (диффузия)Костяной шрот после промывки подвергают обесклеиванию. В практике этот процесс называют диффузией. Диффузия – процесс перевода клейдающего вещества кости оссеина в клеевое вещество глютин. Клей (глютин) образуется при переменном воздействии на влажную кость пара и горячей воды. Под действием пара оссеин (коллаген кости) переходит в глютин. Вода выщелачивает образовавшийся глютин и превращает его в клеевой бульон (раствор клея в воде). Процесс обесклеивания кости можно вести в одном диффузоре (автоклаве), переменно производя распарку и заливку кости свежей горячей водой. Однако этот способ не выгоден несмотря на хорошее качество клея, так как получаются слабые бульоны (2 – 3 %) и требуется мощное вакуум-аппаратное отделение.
Обесклеивание кости производят способом последовательного насыщения в диффузорах, соединенных в батареи по 3 – 6 штук. Циркуляционные воды (бульоны) по мере насыщения передаются по трубопроводам в диффузоры с менее обесклеенной костью. Наиболее концентрированные бульоны, попадают на свежую кость, а свежая вода – на кость, в значительной степени обесклеенную (принцип противотока). В результате получаются бульоны концентрацией 6 – 10 %, которые передаются на упаривание. Качество клея, получаемого при работе в диффузионной батарее, несколько ниже, чем при работе в одном диффузоре, так как бульон, проходя через 5 – 6 диффузоров, подвергается более продолжительному действию температур.
Цикл работы каждого диффузора складывается из следующих операций: загрузка, замочка кости в холодной воде, обработка паром (распарка и циркуляционными водами – бульонами (повторяется 6 – 12 раз), обработка паром (распарка) и свежей водой (повторяется 2 – 3 раза), выгрузка.
Общее количество распарок 8 – 15. Общая продолжительность работы диффузора 18 – 24 часа. Полноту обесклеивания проверяют по содержанию азота в обесклеенной кости, которое не должно быть выше 0,9 % (1 % азота соответствует 5,5 % клея). Пар, отходящий из диффузоров, используют для подогрева воды, поступающей в диффузоры. Клеевые бульоны первых двух-трех вод подают на упаривание. Обесклеенную кость (паренка), содержащую до 40 % воды, выгружают из диффузоров и передают на сушку в сушильные барабаны, откуда она поступает на размол (влажность 8 – 10 %). Размалывают сухую паренку на шаровых или молотковых мельницах. Полученную тонкоизмельченную костную муку применяют в качестве удобрений, а частично используют для подкормки животных (фосфорин).
13.1.8 Упаривание клеевого бульонаКлеевые бульоны, полученные в процессе обесклеивания кости и имеющие концентрацию 6 – 10 %, сливают в приемные баки, откуда их центробежным насосом подают на упаривание. Бульоны нельзя долго держать в приемнике, так как они являются благоприятной средой для развития микроорганизмов. Упаривать бульон при 100 °С нельзя, так как ухудшается качество клея: понижается вязкость, клеящая способность, способность к желатинизации. Поэтому процессы упаривания клеевых бульонов ведут в вакуумаппаратах, в которых поддерживается давление ниже атмосферного. По мере понижения давления температура кипения жидкости понижается. Например, при атмосферном давлении 760 мм ртутного столба вода кипит при 100 °С, если же давление в аппарате снизить до 50 мм ртутного столба то вода будет кипеть при 40 °С.
Разрежение в аппарате создается вакуум-насосом через конденсатор.
Пар, получающий в аппарате при упаривании, конденсируется вследствие охлаждения его холодной водой, непрерывно поступающей в конденсатор. Нагревают упариваемую жидкость паром, подводимым в паровую камеру. Упаривание стремятся проводить с наименьшими затратами пара, для чего пользуются многокорпусными вакуум-аппаратами. В однокорпусном аппарате весь пар, образовавшийся при упаривании жидкостей (соковый пар), поступает в конденсатор и отдает свое тепло охлаждающей воде. Если же соковый пар направить в обогревающее пространство другого аппарата, то он будет использован для упаривания бульона. Соковый пар из первого корпуса можно направить в обогревающее пространство второго корпуса.
На клеевых заводах распространены двух– и трехкорпусные вакуумаппараты непрерывного действия «Виганд» и системы «Большевик» (рисунок 13.2 – 13.3).

1 – питательная коробка; 2-труба снабженная дроссельным клапаном; 3 – подогреиатель; 4 – отделитель первого корпуса; 5 – труба для подачи пара к тепловому насосу; 6 – тепловой насос; 7 – труба для подачи сгущенного бульона в рабочее пространство второго корпуса; 8 – труба, соединяющая отделитель с подогревателем; 9 – отделитель второго корпуса; 10 – груба, по которой откачивается упаренный бульон; 11 – насос; 12-поверхностный конденсатор; 13 – труба мокровоздушный насос; 14 – циркуляционные трубки.
Рисунок 13.2 – Двухкорпусный вакуум-аппарат системы «Виганд»

Рисунок 13.3 – Схема трехкорпусного вакуум-аппарата «Большевик»:
В аппаратах непрерывного действия упаренный клей откачивается насосом из последнего корпуса в отстойный чан. Конденсаторы применяются смесительные и поверхностные. В смесительных конденсаторах соковый пар конденсируется, смешиваясь с охлаждающей водой. Вода и конденсат уходят самотеком по барометрической трубе. Из верхней части конденсатора воздух откачивается насосом. В поверхностном конденсаторе охлаждающая вода циркулирует в трубках, а конденсируемый пар обтекает трубки снаружи. Конденсат и воздух отсасываются одним насосом (мокровоздушным).
Поверхностный конденсатор имеет недостатки: латунные трубки быстро изнашиваются и требуют частой замены. Поршневой насос для откачивания, упаренного клеевого раствора находится на одном валу с вакуум-насосом. Основные показатели работы вакуум-аппаратов приведены в таблице 13.2.
Таблица 13.2 – Показатели работы вакуум-аппаратов


Производительность вакуум-аппаратов определяется количеством испаряемой воды в час. Отсюда следует, что производительность вакуум-аппарата по количеству упаренного раствора будет зависеть от начальной концентрации бульона и той концентрации, до которой его упаривают.
Расчет делают по следующей формуле:
В = Б (1– К1/К2), (1)
где В – вес воды, упаренной за какой-либо промежуток времени, кг;
Б – вес бульона, подающегося в аппарат, кг;
К1 – начальная концентрация бульона, %;
К2 – концентрация после упаривания, %.
13.1.9 Консервирование клеевого бульонаКлеевые бульоны являются благоприятной средой для развития микроорганизмов и способны быстро загнивать. Поэтому необходимо их своевременно консервировать. В большинстве случаев для консервирования и отбелки клеевого бульона применяют сернистый газ, сернистую кислоту и соли гидросернистой кислоты; рН среды после консервирования 5,6 – 6,0 в зависимости от времени года. Летом среда должна быть более кислая, так как возможность развития микроорганизмов наибольшая.
Сернистым газом бульон обрабатывают в газовочных чанах, внутри чана устанавливают два змеевика с отверстиями, по которым поступает сернистый газ. Сернистый газ получают при сжигании серы в серных печах, компрессор нагнетает в печь воздух. Сернистый газ очищают, пропуская его через воду в специальных резервуарах (скрубберах). По окончании консервирования подачу сернистого газа прекращают и бульону (упаренный раствор клея) дают отстояться до полного удаления воздуха в течение 10 – 12 часов.
13.1.10 Желатинизация клеяПри охлаждении клеевые растворы переходят из жидкого состояния в студнеобразное, т.е. из золя в гель. Этот процесс называется желатинизацией. Упаренные и консервированные растворы клея являются готовым продуктом, пригодным для применения его в качестве склеивающего вещества. Растворы клея разливают в бочки и направляют в реализацию. Применение клея в таком виде ограничено, так как его трудно транспортировать на далекие расстояния, он может загнить при неблагоприятных условиях обработки и хранении, поэтому необходимо выпускать клей в сухом виде.
В большинстве случаев клеевые растворы обезвоживают путем поверхностной сушки в студнеобразном состоянии. При обезвоживании в распылительных или барабанных сушилках желатинизация не производится. Температура и скорость застудневания бульонов зависит от их концентрации: сильно разбавленные растворы не застудневают даже при низких температурах. Имеются различные способы желателизации в зависимости от размеров и формы получаемого студня и от техники охлаждения растворов: желателизация в блоках (формах), на столах, на непрерывно движущейся ленте, с последующей резкой полученного студня на плитки различных размеров.
При желантинизации клеевые растворы охлаждают воздухом, водой, рассолом или в органических растворителях. Желатинизация клея на столах и в блоках является трудоемким процессом, так как процессы розлива, резки, укладки сеток на вагонетки и съемки плиток с сеток не механизированы; большой расход воды (до 100 т на 1 т сухого клея); требуются большие площади для столов и желатинизаторов.
Более прогрессивные методы – это желатинизация на непрерывно движущейся ленте и в органических растворителях в специальных установках (клей в виде гранул). Концентрация растворов клея перед желантинизацией 43 – 45 %, температура 40 – 42 °С. Температура охлаждающих растворов при желантинизации на ленте 6 – 10 °С, при желантинизации в органических растворителях 0 – 2 °С. На плитке клей режут на столах вручную; из форм бруски разрезают на специальной резательной машине. Разрезанные плитки клея раскладывают на сушильные сетки, которые укладывают на вагонетки (лафеты) и ставят в сушильные камеры.
13.1.11 Сушка клеяСушат клей нагретым воздухом, который поглощает влагу из галерты.
Скорость высыхания зависит от интенсивности испарения влаги с внешней поверхности плитки и от скорости прохождения паров воды из внутренних слоев плитки к ее поверхности.
Интенсивность испарения влаги можно увеличить, повышая температуру воздуха, увеличивая количество воздуха, подаваемого в сушила. Чем суше воздух, подаваемый в сушила, тем быстрее высыхает клей. Наивысшая температура в начале сушки клея определяется точкой плавления галерты (22 – 25 °С), которая зависит от качества клея (концентрация, вязкость). Повышение температуры увеличивает скорость сушки, но высокая температура может вызвать частичное или полное плавление студня, в результате чего клей прилипнет к сеткам. Следовательно, температура воздуха в сушилке должна быть на всем протяжении сушки несколько ниже температуры плавления студня. Одно и тоже количество воздуха не может беспредельно поглощать влагу; наступает момент, когда воздух полностью насыщается влагой и прекращает дальнейшее ее поглощение. Отсюда следует, что нужно беспрерывно отводить отработанный воздух, т.е. воздух, насыщенный влагой.
Для сушки клея применяют туннельные сушки. Это каналы длиной 45 – 50 м с поперечным сечением, соответствующим ширине и высоте двух рядом стоящих вагонеток. С одной стороны камеры установлен паровой калорифер, а с другой – вентилятор. В процессе сушки вагонетки с плитками сырого клея подаются в сушильный канал и устанавливаются со стороны вентилятора. Постепенно по мере высушивания вагонетки передвигаются к калориферу.
В процессе сушки воздух, подогретый в калорифере, перемещаясь вдоль сушильного канала, отдает свое тепло клею и сам охлаждается. Нагревание воздуха в калорифере регулируют так, чтобы в конце сушильного канала, где устанавливаются вагонетки с плитками сырого клея, температура была 22 – 25 °С. Разность температуры воздуха у калорифера и у вентилятора зависит от количества клея, загруженного в сушильный канал. Она равна 8 – 10 °С. Поскольку в одном канале нельзя создать большой разницы между температурой подогретого и отработанного воздуха, процесс сушки клея разделяют на две ступени (в отдельных каналах): предварительную сушку и окончательное досушивание.
В первом канале при температуре воздуха у калорифера 35 °С и у вентилятора 20 – 25 °С в течение 3 – 4 дней удаляется основная масса воды, повышается концентрация и точка плавления галерты, после чего вагонетки с клеем переводят в другие каналы для досушивания при более высоких температурах. Обмен воздуха в горячих камерах должен быть замедлен и согласован с относительной влажностью и температурой отработанного воздуха: чем ниже (при прочих равных условиях) относительная влажность и температура отработанного воздуха, тем меньше требуется воздуха для сушки, и наоборот. Продолжительность сушки плиточного клея 7 – 11 дней в зависимости от атмосферных условий, толщины плитки, концентрации и других факторов. Зимой климатические условия более благоприятствуют сушке клея благодаря большей разнице температур наружного и подогретого воздуха, при этом увеличивается его влагоемкость.
Особое внимание при сушке клея должно быть обращено на относительную влажность отработанного воздуха; она должна колебаться в пределах 75 – 80 %. Если относительная влажность воздуха сильно понижается, что может быть вызвано похолоданием, необходимо сократить обмен воздуха. В жаркое время года создается опасность, что воздух, не успев дойти до последних вагонеток со свежей галертой, полностью насытится влагой, следовательно, только что поставленный клей не будет сохнуть.
При соприкосновении отходящего воздуха с холодной поверхностью студня не должно происходить конденсации паров воды из воздуха. Влага размягчает поверхность студня, при этом он частично может расплавиться и протечь через сетку. Кроме того, увлажнение способствует плесневению и загниванию студня. В случае значительного увеличения относительной влажности необходимо уменьшить загрузку сушильных камер или прекратить подачу клея. Чтобы предотвратить загнивание, необходимо время от времени пропускать через камеры сернистый газ. Производство сухого клея в виде плиток имеет ряд недостатков:
– продолжительность сушки 7 – 11 дней;
– площадь сушильных камер занимает до 40 % производственной площади клеевого завода;
– требуются большие капиталовложения для оборудования желатинизации и сушилок канального типа;
– операция сушки является громоздким и трудоемким процессом;
– сушильные камеры являются опасным участком с точки зрения противопожарной безопасности (деревянные рамки, сетки, вагонетки в постоянном токе теплого воздуха);
– существующий метод сушки связан с сезонными условиями: в летнее время клей протекает (ввиду несоответствия летних температур точке плавления галерты) и медленно сохнет (ввиду высокой температуры и влажности наружного воздуха);
– применение плиточного клея является неудобным, вследствие необходимости его предварительно замачивать в течение 12-18 часов;
– расход пара на сушку 1 т сухого клея составляет около 4 т.
Поэтому лучше выпускать клей в виде мелких форм – порошка, гранул, таблеток. Порошкообразный клей получается путем распыления слабых или концентрированных растворов клея в распылительных дисковых сушилках. Сушка клея распылением – наиболее совершенный метод. Он имеет целый ряд преимуществ перед сушкой в канальных сушилках: сокращение продолжительности сушки с 7 – 11 дней до 8 – 10 минут; уменьшение затрат труда с 5 человеко-дней на 1 т клея до 1 человеко-дня; полное отсутствие зависимости от метеорологических условий; съем сухого клея с 1 м³ здания 7,5 т в год вместо 0,8 т.
Недостатком порошкообразного клея является его большая гигроскопичность, малый объем веса, кроме того, при его растворении образуются комки. Эти недостатки можно устранить, если брикетировать порошок в виде мелких таблеток.
Гранулированный (перловый) клей получают на специальных установках, в которых концентрированный клеевой бульон вытекает из сита капельницы, установленного в цилиндре высотой 5 – 6 м, в жидкую среду (бензин, керосин) в форме капель. При падении капли, под влиянием сил поверхностного натяжения, принимают форму, подобную гранулам. Температура жидкости 0 – 2 °С при непрерывной циркуляции растворителя. Гранулы, проходя слой охлажденной жидкости, желируются и застывшие падают на дно цилиндра. Образовавшиеся гранулы отводятся из цилиндра в другой сосуд, где отделяются от охлаждающей их жидкости. Отделившиеся гранулы поступают на сушку, а жидкость стекает для охлаждения.
В процессе сушки необходимо, чтобы быстро образовывалась защитная корочка, предохраняющая гранулы от слипания и протекания. Для этого гранулы обдуваются вначале воздухом комнатной температуры. Сушку производят на многоленточных сушилках или перфорированных столах в течение 14 – 16 часов. К нижней части перфорированной поверхности ленты подводится вначале холодный, а затем горячий воздух. Этот метод желатинизации и сушки имеет тоже преимущества перед желатинизацией на столах и сушкой в канальных сушилках, что и сушка в распылительных сушилках.
Существующая технологическая схема получения костного клея не совершенна из-за длительности процессов, больших затрат ручного труда при выгрузке и загрузке экстракторов и диффузоров, резке и раскладке плиток на сетки. В новой технологической схеме, предложенной Гипромясо и ВНИИМПом и осуществляемой на Брянском клеевом заводе, предусмотрены следующие изменения в принятом технологическом процессе.
1. Экстракция жира из кости бензином заменена на импульсный холодный метод обезжиривания измельченной кости. Процесс обезжиривания при этом сводится к пропусканию смеси воды и дробленой кости в соотношении 7:1 – 10:1 через импульсный аппарат, состоящий из цилиндрического корпуса и ротора с подвесными билами. Билы интенсивно ударяют по протекающей смеси, жир вытесняется из кости в результате гидравлических ударов. Вся смесь поступает в разделительную аппаратуру, где разделяется на обезжиренную кость, жировую массу и воду.
Процесс обезжиривания непрерывный, не требует применения огнеопасных растворителей. Обезжиривание совмещается с процессом полировки и замочки. Размер кости в основном 3 – 10 мм. При обезжиривании горячим методом происходит обезвоживание коллагена, кость подвергается вредному термическому воздействию, которое приводит к структурному изменению коллагена. Чтобы частично коллаген привести к первичному состоянию, перед обесклеиванием кость необходимо замачивать. При холодном же методе обезжиривания коллаген не претерпевает никаких химических изменений и сохраняет свою первоначальную структуру. В результате обеклеивания такой кости получается клей с более высокой вязкостью.
2. Обесклеивание кости производят во вращающихся автоклавах или стационарных малой емкости с боковой выгрузкой, так как кость самая мелкая и при работе в диффузоре большей емкости возможно слеживание ее. Продолжительность обесклеивания сокращается в два раза. Предусматривается более длительное отстаивание бульонов или центрифугирование их, так как в процессе обесклеивания в бульон частично переходит минеральная часть кости.
3. Процессы выпаривания, консервирования не изменяются.
4. Желатинизация консервированного и упаренного бульона на охлаждаемых столах или в формах и сушка в канальных сушилках заменена желатинизацией клея в виде гранул.
5. Применяемая очистка жира серной кислотой заменяется сепарированием. Такая очистка обеспечивает получение жира более высокого качества.
6. Сушка и измельчение обесклееной кости не изменяются.
Общая продолжительность процесса производства клея уменьшается с 15 суток до 3.
Правообладателям!
Это произведение, предположительно, находится в статусе 'public domain'. Если это не так и размещение материала нарушает чьи-либо права, то сообщите нам об этом.